Mobius® ADC Reactor Single-Use Components Chemical Compatibility

Antibody-drug conjugates consist of a highly cytotoxic and potent active pharmaceutical ingredient (API) payload linked to a monoclonal antibody (mAb) capable of targeting a surface antigen on cancer cells. Conjugation of the mAb to the small molecule via the linker requires safe handling and containment due to the toxic nature of the payload. When used for this conjugation step, the single-use Mobius® ADC Reactor not only increases operator safety and process efficiency, scalability, reproducibility, and flexibility, but also decreases the risk of contamination.
The conjugation step typically includes the use of organic solvents, and as such, it is important to evaluate compatibility with the reactor’s single-use components. The studies described below evaluated the physical compatibility of single-use components in the Mobius® ADC Reactor and the level of extractables when exposed to dimethyl sulfoxide (DMSO) and dimethyl acetamide (DMAc).
Single-use Components Evaluated for Physical Compatibility and Extractables
All single-use components were evaluated for extractables and physical compatibility following exposure to 100% or 20% DMSO, 100% or 20% DMAc, and Milli-Q® water. Typical solvent concentrations of DMSO and DMAc typically do not exceed 20% during conjugation. The various resins used in the molded plastic components of the ADC Reactor were evaluated as tensile bars (Table 1).
Single-use gaskets and tubing were also evaluated (Table 2).
Experimental Design
Tensile Bars and Tubing Compatibility
Type 1 tensile bars representing the materials used in molded components, along with 6” (15 cm) samples of tubing and 5” x 1” (12 x 2 cm) of the Ultimus® film, were evaluated for tensile strength. Each sample was secured in pneumatic tensile grips and stretched using an Instron machine at a speed of 2” (5 cm) per minute. The percent relative difference between control (gamma irradiated, without solvent exposure) and stretched materials was plotted for each material.
Silicone Gasket Compressibility
A dynamic mechanical analyzer (DMA) instrument was used to assess the compressibility of post-gamma irradiated gasket samples under different solvent extraction conditions. During testing, the gasket underwent a 2% compression relative to its original thickness; the force required to achieve this deformation was recorded and plotted.
Extractables Testing
Analysis of volatile and semi-volatile organic compounds in the 100% DMAc and 100% DMSO extracts was performed using direct inject gas chromatography-mass spectrometry (DI-GC/MS). DI-GC/MS analysis was not performed on the water, 20% DMAc, and 20% DMSO extracts.
Reversed phase HPLC (RP-HPLC) was used to detect non-volatile organic substances in the extraction solution. Absorbance at UV 214 nm was used for detection of extractables.
Physical Compatibility and Extractables Results
Tensile Bars and Tubing Compatibility
None of the post-gamma irradiated tensile bars (Figure 1), tubing material (Figure 2), or Ultimus® film (Figure 3) samples displayed a notable decrease in measured tensile strength compared to the respective controls. These results demonstrated compatibility of the materials with Milli-Q® water, 100% DMAC, and 100% DMSO solvents under extraction conditions (to the exception of Ultimus® film, which was tested with 20% DMSO / DMAC).

Figure 1a.Relative change in tensile strength of resins used in mAb addition ports following solvent exposure.
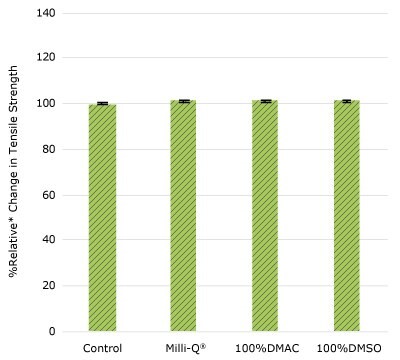
Figure 1b.Relative change in tensile strength of resins used in impeller cup following solvent exposure.

Figure 1c.Relative change in tensile strength of resins used in TC port following solvent exposure.
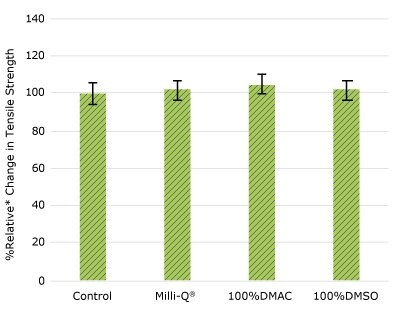
Figure 1d.Relative change in tensile strength of resins used in impeller following solvent exposure.

Figure 1e.Relative change in tensile strength of resins used in port plate following solvent exposure.
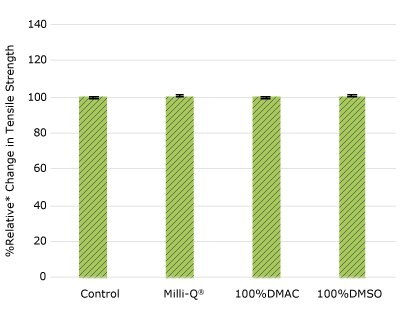
Figure 1f.Relative change in tensile strength of resins used in TC cap following solvent exposure.
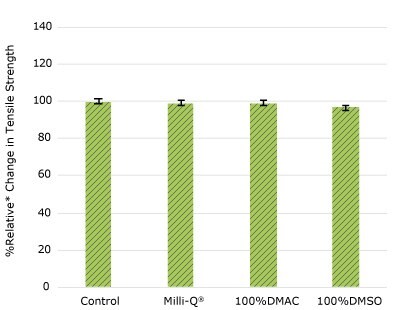
Figure 1g. Relative change in tensile strength of resins used in EJ female luer barbed fitting following solvent exposure.
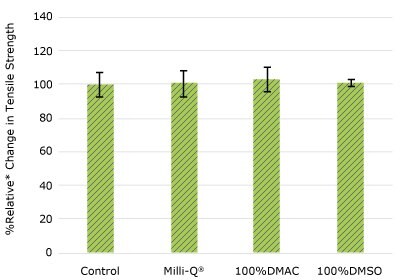
Figure 2a.Relative change in tensile strength of dip tube following solvent exposure.
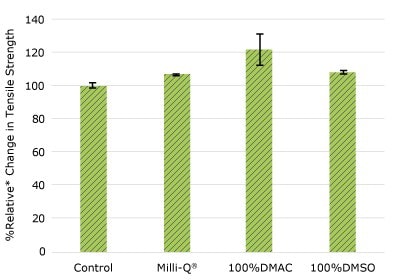
Figure 2b.Relative change in tensile strength of pharma 50 tubing following solvent exposure.
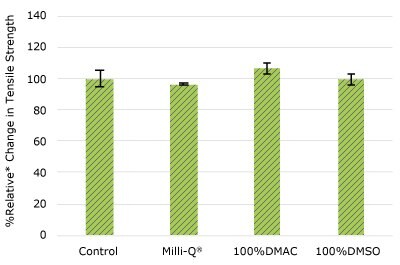
Figure 2c.Relative change in tensile strength of pharma 65 tubing following solvent exposure.
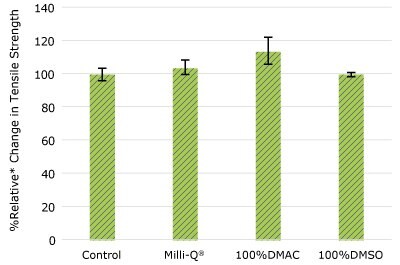
Figure 2d.Relative change in tensile strength of pharma 80 tubing following solvent exposure.
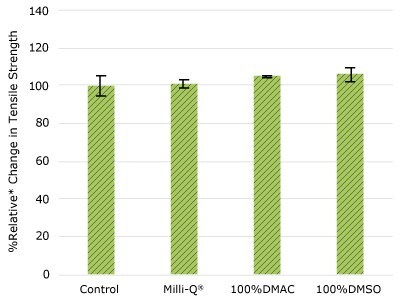
Figure 3.Relative change in tensile strength of Ultimus® film following solvent exposure.
As shown in Figure 4, none of the post-gamma irradiated gasket samples displayed a notable decrease in compression force compared to their respective controls. These results demonstrated compatibility of the gasket samples with Milli-Q® water, 100% DMAC, and 100% DMSO solvents under extraction conditions.
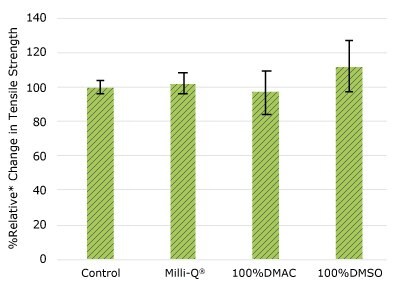
Figure 4.Relative change in compressibility of gasket samples following solvent exposure.
Extractables
The following tables summarize results of the extractables studies. As shown by RP-HPLC and DI-GC/MS, the resins had excellent resistance when exposed to 100% DMAc and DMSO at 40°C for up to 72 hours with no observed visual or functional defects (Table 3). Similar results were obtained for gaskets, tubing, and Ultimus® Film with RP-HPLC (Table 4) and DI-GC/MS (Table 5).
Conjugation being followed by further purification steps such as tangential flow filtration and typically a buffer exchange, additional reduction of leachable components is expected.
Conclusion
Single-use technologies offer many benefits for production of ADCs including increased operator safety, process efficiency, scalability, reproducibility, and flexibility. As with all single-use systems, understanding solvent compatibility is essential for a successful and safe implementation. As demonstrated by the results described above, the molded plastic components, tubing, gaskets, and Ultimus® film used in the Mobius® ADC Reactor are all compatible with concentrations of DMSO and DMAc that exceed typical conjugation conditions.
If you have questions about our ADC reactor offering, our experts can help you find the right product for your process.
Zaloguj się lub utwórz konto, aby kontynuować.
Nie masz konta użytkownika?