Die Entwicklung robusterer Folien und damit letztendlich auch widerstandsfähigerer Einwegbeutel erforderte jahrelanges Tüfteln, Ausprobieren und Testen von Tests.
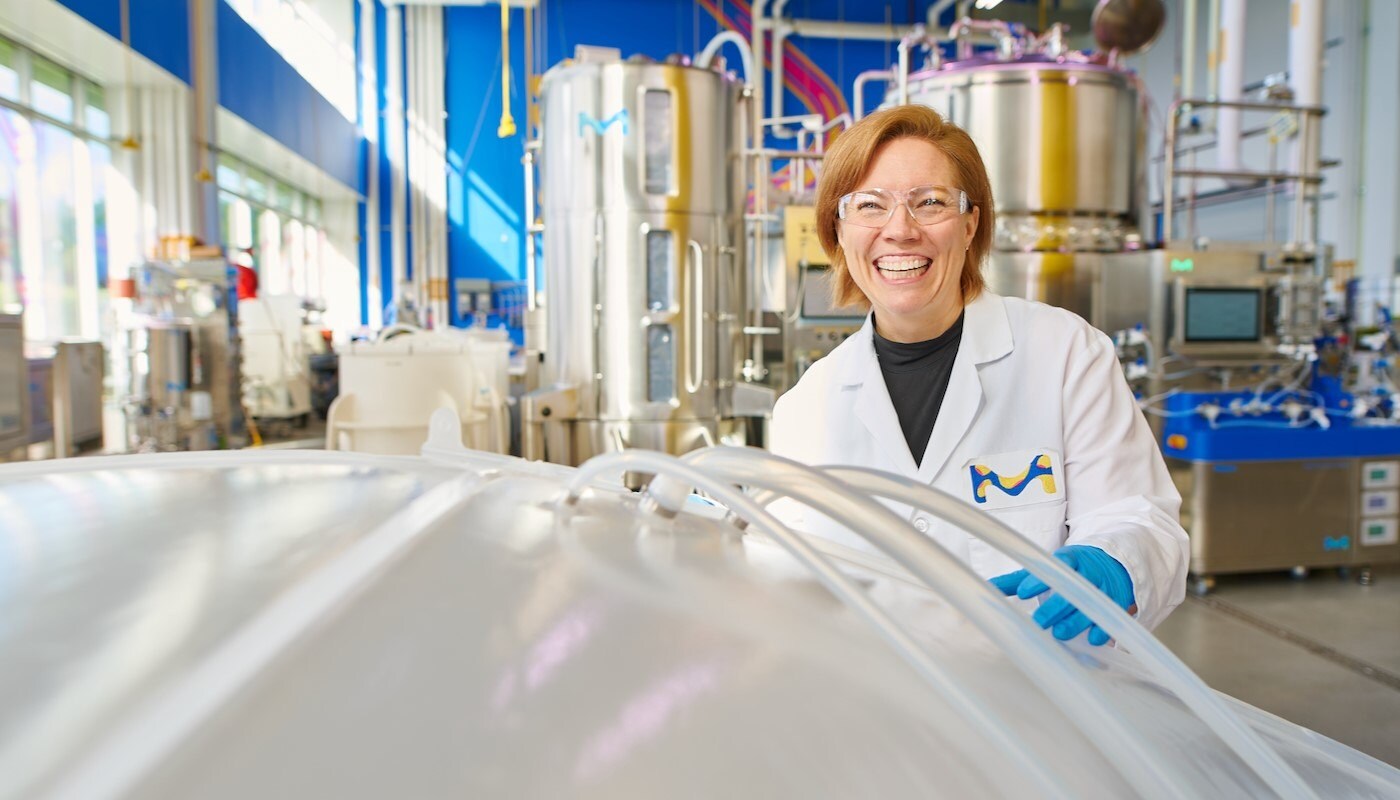
Shannon Cleveland hält im M Lab einen Einwegbeutel aus Ultimus-Folie in der Hand.
18. September 2023 | 6 Min.
Hier steckt mehr dahinter, als man auf den ersten Blick vermuten würde.
Bei mehrschichtigen Materialien dienen die verschiedenen Lagen unterschiedlichen Zwecken. Manche sorgen für strukturelle Stabilität. Andere machen Werkstoffe widerstandsfähiger gegen Temperaturschwankungen oder biegbar. Das trifft auf die Reifen unserer Autos, die Raumanzüge von Astronauten – oder einen neuen Einwegbeutel für die Hersteller von Biopharmazeutika zu.
Mehrere Jahre lang beschäftigten sich die Ingenieure von Merck – darunter Shannon Cleveland und David DeCoste – mit dem Design neuer Einwegbeutel, die in der Arzneimittelherstellung zur Auskleidung diverser Anlagen und Geräte zum Einsatz kommen. Die Entwicklung der Einwegbeutel war keine leichte Aufgabe. Zunächst musste das Team herausfinden, welche Materialien überhaupt verwendet werden sollten. Im nächsten entscheidenden Schritt galt es dann, sicherzustellen, dass diese Schichten perfekt zusammenpassen.
„Die Folie besteht aus dreizehn verschiedenen Lagen, und jede Schicht erfüllt einen bestimmten Zweck“, erklärt DeCoste, Research and Development (R&D) Director des Teams. Bestimmte Schichten schaffen das geeignete Umfeld für Zellwachstum, während andere für Festigkeit und Flexibilität sorgen. Damit das Produkt auf den Markt gebracht werden konnte, war ein großes Entwicklungsteam erforderlich, in dem viele Abteilungen mitarbeiteten.“
Zu Beginn schon das Endergebnis vor Augen haben
In vielen biotechnologischen Produktionsanlagen dienen Einwegbeutel dazu, Bioreaktoren auszukleiden – Gerätschaften, die häufig großen Gärbehältern in Brauereien ähneln. In den Bioreaktoren werden Zellen und andere Materialien aufbewahrt, die zur Herstellung lebensrettender Medikamente benötigt werden. Einwegbeutel beschleunigen die Arzneimittelherstellung, da sie neben vielen anderen Vorteilen den Reinigungsaufwand zwischen den einzelnen Chargen verringern. Das bedeutet, dass die Produktionsstätten in kürzerer Zeit mehr Medikamente herstellen können.
Wenn ein Einwegbeutel mit einer pharmazeutischen Mischung undicht wird, ist das enorm frustrierend und kostspielig. Da die Beutel mit großen Mengen an Flüssigkeit gefüllt und unterschiedlichen Temperaturen ausgesetzt sind und im Betrieb hin- und herbefördert werden, besteht permanent die Gefahr, dass sie durchgescheuert oder durchstochen werden.
Für Cleveland und andere Beteiligte macht der Gedanke daran, dass ihre Arbeit letztendlich den Patienten zugute kommt, auch einen langen Arbeitstag lohnenswert. „Zu wissen, dass ich an der Entwicklung von Produkten mitarbeite, die etwas bewirken, erfüllt mich mit großer Befriedigung“, sagt sie.
Die Suche nach der richtigen Materialkombination
Mehrere Jahre lang beschäftigte sich das Forschungs- und Entwicklungsteam von Merck in Bedford, Massachusetts, USA – darunter auch Cleveland und ihre Kollegen – intensiv mit der Entwicklung und dem Vergleich verschiedener Materialkombinationen für eine neue Folie für Einwegbeutel. Schon recht früh fanden Sie heraus, dass eine gewebte Nylonstruktur den Beuteln größere Festigkeit und Widerstandsfähigkeit verleiht.
Folien, die Nylon enthielten, erwiesen sich als besonders geeignet, doch die einzelnen Schichten wollten nicht zusammenhalten, so dass die Suche nach anderen Polymeren ihren Anfang nahm. Das Team brauchte eine Verbindungsschicht – oder eine Schicht, die die Struktur zusammenhalten würde. Also begannen sie, Kombinationen eingehend zu testen.
Die Ingenieure setzen eine Folie im Labor einer enormen Belastung aus. Dabei wird sie immer wieder verdreht und zusammengedrückt – 2.700 Mal, um genau zu sein.
Nachdem ein Stück der Folie „durch die Mangel gedreht“ war, wie Cleveland den Prozess treffend beschreibt, analysierte sie, wie stark die Drehbewegungen das Material beanspruchten. Für einen anderen Test berechneten Cleveland und Kollegen, wie lange es dauerte, bis eine Metallspitze die Folie durchstochen hatte.
Diese Tests – und noch eine Reihe anderer – brachten die Forscher zu einer unbefriedigenden Schlussfolgerung: Die Polymere, die es in die Endauswahl geschafft hatten, schnitten alle in gleicher Weise ab. Bei den Tests konnte kein Unterschied zwischen den verschiedenen Polymeren in der Verbindungsschicht festgestellt werden. Doch Cleveland konnte einen visuellen Unterschied zwischen den strapazierten Materialien ausmachen. Sie erkannte, dass mehr dahinter stecken musste.
„Ich brauchte neue Daten, um Unterschiede zwischen den Folien feststellen zu können. Also musste ich mir einen neuen Test überlegen“, erklärt Cleveland.
Ein getrübter (Durch-)Blick
Nach sorgfältiger Lektüre der einschlägigen Fachliteratur beschloss Cleveland, etwas anderes auszuprobieren. Die richtige Kombination von Polymeren zu finden und das Verfahren zum Zusammenfügen der Folienschichten zu optimieren, war von entscheidender Bedeutung – ohne Zweifel. Ein ganz wichtiger Durchbruch und Schlüsselmoment war es jedoch, als sie eine Möglichkeit gefunden hatte, die verschiedenen Materialkombinationen zu evaluieren.
Anstatt die Folien mit einem spitzen Gegenstand zu durchstechen, entschied sich Cleveland dazu, die verschiedenen Folien mit einer stumpfen Spitze zu dehnen. Die dislozierten Materialien sahen leicht getrübt aus, so dass Cleveland beschloss, diesen Effekt zu quantifizieren. Je stärker die Folie gedehnt wurde, desto trüber und dünner wirkte sie.
Niemand in ihrem Labor hatte dies zuvor ausprobiert, daher stand ihnen nicht gleich die passende Ausrüstung zur Verfügung. Als Glücksfall erwies sich ihre frühere Tätigkeit im Forschungs- und Entwicklungslabor für Filtration, das sich ganz in der Nähe ihres jetzigen Labors befindet und in dem das Thema Trübung tatsächlich untersucht wird und dazu auch Tests durchgeführt werden. Zwar werden dort Flüssigkeiten und keine Folien getestet, aber Cleveland wagte dennoch einen Versuch.
Sie quantifizierte damals die Trübung des Wassers, warum also nicht auch die von Kunststoff?
Mit einer Fülle von Fachliteratur im Hinterkopf, einer Schere und Etiketten bewaffnet, machte sich Cleveland an die Arbeit. Sie schnitt winzige Kunststoffstückchen ab, füllte sie in Küvetten und ließ das Trübungsmessgerät seine Arbeit erledigen. Nach ein paar Durchgängen wusste sie, dass sie auf der richtigen Spur war. Sie hatte einen Weg gefunden, zu quantifizieren, welche Folien weniger trüb – und dadurch widerstandsfähiger – waren als andere Folien. Anhand dieses neuen Tests konnte das Team das Erscheinungsbild und die Eigenschaften der Folie weiter verfeinern und optimieren.
Sie mag Herausforderungen wie diese. Problemstellungen, die ein iteratives Vorgehen und unkonventionelles Denken erfordern. „Es macht mich glücklich“, sagt sie und lässt den kreativen, wenn auch etwas unorthodoxen Denkprozess Revue passieren, aus dem die Folie hervorgegangen ist. „Ich bin dankbar, dass ich auf meine Weise denken und damit etwas bewirken kann.“
In der Schule wird angehenden Wissenschaftlern beigebracht, Hypothesen aufzustellen, zu testen, zu testen und nochmals zu testen. Manchmal brauchen sie auch Tests für Tests. Genau diese Puzzlearbeit spornt Cleveland und ihre Kollegen an. Von den Anfängen im Labor über das Upscaling mit dem Produktionsteam bis hin zur Markteinführung arbeiteten weit über hundert Menschen zusammen, um die Ultimus-Folie – und die neuen Einwegbeutel – zu realisieren.
Mit der Ultimus-Folie hat ihre Arbeit allerdings nicht aufgehört. Das Team ist bereits auf der Suche nach neuen Lösungen, darunter Beutel, die sich besser versenden und verpacken lassen. Bei allem, was sie tun, haben sie ein gemeinsames Ziel vor Augen: Hersteller von Biopharmazeutika dabei zu unterstützen, lebensrettende Medikamente schneller herzustellen. Am Horizont zeichnen sich sogar noch bessere Folien und Beutel ab. Und wahrscheinlich auch mehr Tests.
Mehr über Ultimus
Die Ultimus® Folie ist für Mobius® 3D-Einweg-Bioprozessbeutel erhältlich und stellt eine robustere und strapazierfähigere Lösung für alle Herausforderungen in Verbindung mit der auf Single-Use-Systemen basierenden biopharmazeutischen Herstellung dar. Erfahren Sie mehr über die Ultimus® Folie. Finden Sie heraus, wie sie zusätzliche Robustheit und Sicherheit für Bioprocessing-Anwendungen bieten kann und informieren Sie sich über die Spezifikationen und vieles mehr.
Besonderer Dank
Shannon Cleveland und David DeCoste danken allen Kolleginnen und Kollegen, die maßgeblich an der Entwicklung der Folie beteiligt waren, allen voran Joe Cianciolo, Joe Muldoon, Brian Pereira, Diana Perez, Marissa Maher und Kate O'Brien aus der Forschung & Entwicklung.
Mehr Stories lesen

Mike D'Acquisto II, ein wissenschaftlicher Glasapparatebauer, richtet die Flamme auf den Hals eines Rundkolbens.
Glasfläschchen und Bechergläser werden in Serie gegossen. Maßgefertigte Glaswaren für wissenschaftliche Zwecke werden hingegen von hochqualifizierten Glasbläsern in Handarbeit hergestellt und ausgebessert – ein Prozess, bei dem Funken sprühen, es knallt und Momente voller Anspannung gibt.
Lesen Sie, wie Glasbläser für die Wissenschaft die Hitze im Griff haben.
Um weiterzulesen, melden Sie sich bitte an oder erstellen ein Konto.
Sie haben kein Konto?