Nanostructured Materials Through Ultrasonic Spray Pyrolysis
Jin Ho Bang1, 2, Yuri T. Didenko3, Richard J. Helmich1, 4, Kenneth S. Suslick1
1School of Chemical Sciences, University of Illinois at Urbana-Champaign, 2Current address: Department of Chemistry and Applied Chemistry, Hanyang University, 55 Hanyangdaehak-ro, Sangnok-gu, Ansan, Kyeonggi-do 426-791, Republic of Korea, 3UT Dots, Inc., 4Current Address: Dept. of Labor, Mine Safety and Health Administration, 6th Ave. and Kipling Pkwy, Bldg 25, Denver, CO 80225
Introduction
Advances in materials have often been led by the development of new synthetic methods that provide control over size, morphology and structure. The preparation of materials in a scalable and continuous manner is critical when development moves beyond lab-scale quantities. The ease and scalability for preparing materials has been a driving force for the development of new methodologies for several decades.1 In this respect, the development of aerosol syntheses has been particularly successful.2 Spray pyrolysis has been widely used in industry for preparing fine powders, in addition to thin film deposition. This technique has been generally accepted because the apparatus is simple, continuous, and easily scaled up to mass production. In general, spray pyrolysis involves the thermal reactions of aerosols (i.e., solid or liquid droplets suspended in a gas) generated by a nebulizer (e.g. pneumatic, ultrasonic, or electrostatic) carried in a gas flow through a furnace.
Among the various nebulization techniques available (Table 1), the use of ultrasonic nebulizers has been favored because of their outstanding energy efficiency in aerosol generation, affordability, and the inherent low velocity of the initially formed aerosol. Ultrasonic spray pyrolysis (USP) has been shown to be particularly effective for the preparation of a wide array of materials, and it has the advantage of being highly scalable and continuous.3,4 Like sol gel process, USP technique is also a solution based method wherein high frequency ultrasound is passed through a liquid precursor solution, impinging on a liquid-gas interface, which forms an aerosol of micron-sized liquid droplets. The ultrasonically generated droplets of reaction precursors thus become individual chemical microreactors as they are carried by gas flow into a heated furnace where reactions occur. Evaporation of volatile solvent can be followed by chemical reactions either of the remaining solid or, in the presence of high boiling co-solvents or molten salts, in submicron-sized liquid droplets. Such reactions can occur in the interior of the droplet or on the droplet surface. A very wide range of nanomaterials have been prepared by USP, including nanoporous metal oxides and sulfides, nanocomposites, very high surface area carbons, semiconductor quantum dots, and conductive metal inks.
Ultrasonic Nebulization and Aerosol Formation
In ultrasonic spray pyrolysis, ultrasound does not induce reactions such as those commonly found in sonochemical reactions,4,5 but instead generates a low-velocity aerosol.6 The ultrasound used for these techniques is typically low intensity and high frequency, ~2 MHz. The droplet formation by ultrasound was first described by R. W. Wood and A. L. Loomis in 1927, and in 1962, Lang experimentally established the relationship between ultrasonic frequency and average droplet size:

where Dd is average droplet diameter, γ (N m-1) is the liquid’s surface tension, ρ (kg m-3) is the solution density, and f(MHz) is the ultrasonic frequency.
Ultrasonic aerosol fountains (Figure 1A) are the result of capillary waves (i.e., waves travelling along the interface between two fluids) at the surface of liquids, and the aerosol generation is a result of momentum transfer. When the amplitude of the surface capillary waves is sufficiently high, the crests (peaks) of the waves can break off, resulting in liquid droplets. Since capillary wavelength is inversely proportional to wavelength, smaller droplets can be generated with higher frequencies.

Figure 1. A) Photograph of an ultrasonic aerosol fountain produced using 1.7 MHz ultrasound. Schematic illustration of B) a typical laboratory scale USP apparatus, C) and D) simplified gas-solid USP and gas-liquid CAFS reaction processes, respectively.
USP and CAFS Apparatus
A typical USP reactor (Figure 1B) is composed of a high frequency ultrasonic transducer (like that found in a household humidifier) submerged in water below the base of a nebulization vessel containing the precursor solution. A thin, flexible polymer film (e.g. polyethylene, polypropylene, or polytetrafluoroethylene) is used at the base of the reactor reservoir to separate the precursor solutions from the ultrasonic transducer. This configuration allows ultrasound to be effectively transmitted through the polymer membrane into the precursor solution allowing nebulization to occur, while sequestering the solution under an inert or reactive gas of one’s choosing. The nebulization vessel is fitted with a gas stream to carry the aerosol into a tubular furnace, and out to a collector (e.g., a bubbler, filter, electrostatic precipitator, etc.).
The USP process involves the sequence of (1) droplet generation, (2) evaporation of solvents in the heated zone, (3) diffusion of reactants, (4) reaction or precipitation, and (5) escape of any product volatiles. The nature of the final state is critically dependent on the phase of the material that remains after loss of the volatile solvent. USP has most commonly been used to produce solid particulates (i.e., spray drying) that may undergo solid state pyrolysis while in the tube furnace (Figure 1C). More recently, several groups have used high boiling co-solvents, ionic liquids, or molten salts to keep the droplets of the reacting aerosol in a liquid state throughout the heated zone; such droplets then serve as isolated micron-sized chemical reactors (Figure 1D). The use of liquid droplets has been referred to as salt-assisted7,8 USP or more generally, as chemical aerosol flow synthesis (CAFS).4,9-11
Nanostructured Materials via Ultrasonic Spray Pyrolysis
Metal Oxides
Historically, the formation of metal oxides by USP has been heavily studied.2,12 By nebulizing precursor solutions containing water soluble metal salts (e.g. chloride, nitrate, acetate, hydroxides) or metal coordination complexes (e.g. peroxo-, ammonium, lactate, oxo-), a myriad of mono- and multi-metallic oxide powders have been created by USP. With the addition of polymers, colloidal silica, or other composites forming materials, new and complex architectures can be easily added to many of the simple oxide particles previously reported. For instance, utilizing an aqueous solution containing a titanium complex and colloidal silica, Suh and Suslick have prepared various forms of nanostructured titania (Figure 2).13-14 This combination of precursors produces porous titania microspheres after selectively etching the silica template with HF (Figure 2B). Interestingly, the addition of transition metal ions to the precursor solution caused an unusual phase separation to occur during USP, resulting in the outer shell becoming enriched in titania with the core of the particles consisting of silica. Etching the transition metal containing composites with HF for short periods of time yielded particles with a ball-in-ball morphology (Figure 2C), and further etching completely removed the silica leaving a hollow, porous titania spheres behind.14 Cytotoxicity studies revealed the microspheres had little effect on the viability of various cell lines. Further studies using these materials for delivery of a potent drug for the treatment of Alzheimer’s disease (dehydroevodiamine) showed excellent selectivity for delivery to the cell cytosol rather than cell nuclei.15
Other examples of nanostructured oxide composites created by USP were pioneered by Okuyama and coworkers using polymer beads in the nebulized droplets as templates for creating macroporous oxide particles.16 One may expand upon this work by using inexpensive organic monomers (e.g., styrene), instead of expensive polymer beads, to generate interesting macroporous morphologies.13 One may also include Co2(CO)8 (Prod. No. 60811) in the precursor solution to form ferromagnetic microsphere composites with nanoparticles of Co encapsulated in silica; these show no loss of magnetic susceptibility due to the oxidation of Co even after 6 months.13 More recently, the ultrasonic spray synthesis of oxides has been aimed at creating materials with specific applications, such as sensors for the detection of toxic industrial gases and photocatalysts for solar energy conversion.17 For example, chemically responsive inks, which have important applications to chemical sensing, have been made using a CAFS method by the condensation reaction of tetramethoxysilane (Prod. Nos. 679259, 341436) and methyltrimethoxysilane (Prod. No. 679232, 246174, 440175) around soluble dye molecules, producing an organically modified silica (ORMOSIL) pigment within the aerosol droplets.11
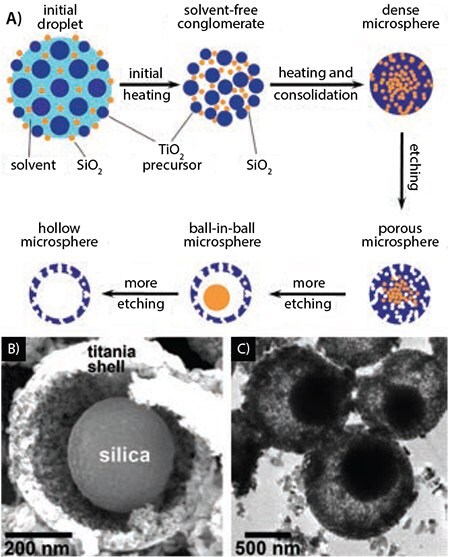
Figure 2. A) Schematic of the USP synthesis of porous, hollow, and ball-in-ball titania spheres, and electron micrographs of B) SEM and C) TEM images of ball-in-ball silica-titania composite decorated after partial etching with HF.
Metal Sulfides and Other Chalcogenides
While ultrasonic spray has proven to be a versatile route to many different oxide materials, a variety of nanostructured sulfides and other chalcogenides can be prepared using both USP and CAFS methods. For example, Skrabalak and Suslick,18 pyrolyzed aerosol solutions of (NH4)2MoS4 (Prod. No. 323446) and prepared a highly effective MoS2 (Prod. No. 234842, 69860) catalyst for hydrodesulfurization (HDS), the critical process for the removal of sulfur from petroleum. Porosity was induced in the MoS2 microspheres by adding colloidal silica to the precursor solution and subjecting the material to a post-synthesis etching step (Figure 3). MoS2 is a layered material with S-Mo-S---S-Mo-S layers; the catalytically active sites, however, are only the exposed Mo atoms at the edges of these layers. The nanoporosity induced by the silica template dramatically increases the number of active edge sites and the catalytic activity for hydrodesulfurization. When the porous MoS2 was salt impregnated with Co as a promoter, the activity increased well above that of RuS2, which is known to be the most intrinsically active metal sulfide for the HDS process.

Figure 3. Porous MoS2 prepared by USP for catalytic hydrodesulfurization. A) SEM and B,C) TEM of porous MoS2
CAFS has been used to prepare, on large scale, metal chalcogenide quantum dots (QDs).9,19 Didenko and Suslick developed a novel CAFS method using simple, low toxicity cadmium and chalcogenides precursors nebulized with a surfactant capping agent in a combination of toluene and high boiling point solvents (e.g., trioctylphosphine oxide). In this way, the individual droplets of solution act as reactors forming surfactant passivated CdS ( Prod. No. 662550), CdSe (Prod. No. 662356), and CdTe (Prod. No. 716669) QDs. Compared to prior batch processing, which use large volumes of high boiling point solvents into which aggressive and toxic chemicals must be injected quickly and reproducibly, the CAFS method provides a useful flow reactor alternative. The micron-sized droplets of the CAFS precursors are sufficiently small that fast, uniform heating occurs and high quality QDs are obtained as the volatile toluene co-solvent rapidly evaporates. The QDs prepared by CAFS were highly fluorescence with a quantum yield of ~25%, and were tunable over a broad spectra region by simply changing the temperature of the furnace.
Carbon Materials
Porous carbon materials are of interest for their potential use in electrochemical, catalytic, adsorbent, and gas-storage applications. Until recently, most porous carbons were prepared by carbonization of raw natural materials. Recent research efforts emphasize the use of templates and their subsequent removal to produce meso- and macroporous carbons with controlled, and in some cases, periodic pores. With this approach, a carbon precursor/inorganic template composite is first formed, followed by carbonization, then chemical leaching of the template material. Such methodology is tedious, requiring multiple synthetic steps, caustic chemical treatments, and long curing times; scale-up has also proven difficult and is not cost effective due to the destruction of (relatively) expensive templates.
CAFS provides an alternative approach for adding porosity, using molten salts within the droplets to form porous nanostructured carbon as reaction gases are released during the carbon formation. Skrabalak, Fortunato, and Suslick found that by nebulizing aqueous solutions of various organic salts (e.g. alkali metal chloroacetate and dichloroacetate) or even simple sugar mixed with alkali carbonate salts and pyrolyzing the aerosol droplets, they were able to create microspheres of carbon with diverse morphologies (Figure 4).20-21 The choice of precursors is based on compounds in which a single carbon remains after the likely leaving groups (e.g., CO2, HCl, H2O) have been pyrolyzed away. These carbon materials have proved useful as catalyst supports in direct methanol fuel cells (DMFCs).22 By loading the porous carbons created by USP with catalysts consisting of PtRu (Prod. No. 738573) and Pt (Prod. Nos. 204013, 327441, 327476) alone for the anode and cathode, respectively, it was shown that the USP carbon microspheres could improve the electrical output of DMFCs when combined with traditional support materials in the anode and cathode.

Figure 4. TEM images of carbons prepared by ultrasonic spray pyrolysis from 0.5 M sucrose and A) 1.0 M Na2CO3, B) 0.5 M Na2CO3, C) 0.5 M NaHCO3, and D) 1.5 M sodium chloroacetate (H2ClCCO2Na). Furnace residence time is 9 s at 800 °C for A, B, and C, and 700 °C for D. These carbon materials have high surface areas (up to 800 m2/g) and very narrow pore size distributions.
Metals
USP can also be used to prepare metal nanoparticles and nanostructures for many precious and nonprecious metals, almost always by the use of metal oxides that decompose at temperatures below 1000 °C or by high temperature reduction with hydrogen in the flow gas.23 Silver nanoparticles (of interest as printable conductive inks) (Prod. No. 675318) have been made by Hong and coworkers using a liquid phase microreactor for the thermal reduction of silver pentafluoropropionate (Prod. No. 326216) in isoamyl ether (Prod. No. 260649) in the presence of trioctylamine24 (Prod. No. T81000) and a similar process was then scaled up using USP by Didenko and Ni.19 Forming highly reactive metal nanostructures (i.e., metals whose standard reduction potential is less than hydrogen) has remained a serious challenge, however, one that Helmich and Suslick recently addressed in a CAFS synthesis of metallic aluminum (Prod. Nos. 518573, 653608).25 Hollow, metallic aluminum particles were prepared by reacting trimethylamine aluminum hydride solution droplets with TiCl4 (Prod. Nos. 697079, 208566, 254312) vapor. Depending on the solution concentration and reaction temperature the morphology of the hollow microspheres could be changed from macroporous to nonporous. Ultrafine and nanoparticles of metallic aluminum have historically found use in propellants and pyrotechnics26 and more recently as nanothermites.27 The hollow morphology of the aluminum particles prepared by CAFS could easily be developed into similar applications.
Scale-Up and Industrial Applications
Ultrasonic spray pyrolysis on the laboratory scale at high frequencies (~2 MHz) as described earlier is very useful for rapid hypothesis testing and can easily prepare new and exotic materials on a small scale. The ultrasound intensity on the surface of the high frequency transducer, however, is not sufficient to atomize viscous, dense, or very high boiling solvents and slurries. In order to increase product throughput and spray larger amounts of liquid precursors, industrial scale setups for generation of small droplets of liquids using high intensity ultrasound are commercially available. Such ultrasonic nozzles work at frequencies from 20 to 120 kHz to create different droplet sizes (down to ~10 μM) and can spray up to ~100 mL/min of liquids with high viscosities, low vapor pressures and even slurries.19 An example of an industrial scale-apparatus equipped for ultrasonic spray pyrolysis is shown in Figure 5.

Figure 5. A) A pilot plant apparatus diagram with ultrasonic sprayer; B) photograph of the furnace with the inserted glass reactor (one of authors (Y.T.D., 6 ft tall) is shown for scale); C) fluorescence of CdSe quantum dots is controlled by particle size, which is tunable from 2 to 4 nm by use of the tube furnace temperature with fluorescence quantum yields of ~50%.
The yield and the quality of final products depends on the gas and liquid flow rates through the reactor, temperature inside the reactor, ultrasound power, solvents used and chemical composition of the mixture of precursors. By varying parameters of the experiments, it is possible to get very high yields. A variety of products can be obtained in this setup, including cadmium chalcogenide quantum dots (both core and core/shell), metal nanoparticles (silver, copper, nickel, copper/nickel and copper/silver alloys), and metal oxides. Many nanomaterials have been synthesized in a continuous-flow process using this apparatus.
The commercial market for quantum dots is currently dominated by biomedical applications and was worth of $67 million in 2010 and is projected to grow to $670 million by 2015.28 Biomedical applications include bioimaging, flow cytometry, fluorescent labeling for cancer detection and intracellular imaging. The optoelectronics market for quantum dots is small at present, but likely to grow substantially with development of quantum dots for large scale industrial applications including solar energy harvesting, optical filters, displays, LEDs, etc.
The USP production of 10 nm silver nanoparticles (Prod. No. 730785), and 4 nm gold nanoparticles have commercial applications as the base for high quality, inexpensive, low temperature sintering nanometallic inks, which opens the door for large-scale production of printable electronics as well as antimicrobial uses. The largest application of nanometals industrially is the nanosilver market, which is expected to grow from $290 million in 2011 to ~$1.2 billion in 2016.29-30 Nanosilver is used as an antibacterial material in filters for air and water purification, in textiles, and for wound treatment.30-31 Other large scale applications of nanosilver include conductive nanoinks for printed circuits, front-side metallization of solar cells, thin film electronics, sensors, and catalysts. In addition, the market for other nanometals, such as gold, platinum and palladium may grow at an even higher rate than silver, specifically for biomedical applications.
As a final example, there are widespread and increasingly large markets for nanostructured metal oxides, from biomedical to photovoltaics and photocatalysts to lithium batteries.30, 32-33 Nanostructured silica, titania, iron oxides, zinc oxides, and a variety of binary/ternary metal oxides can all be produced via USP,12-16 and they have a variety of therapeutic applications and some are finding new applications in drug delivery forumulations.33-35 Design of biodegradable and biocompatible nanocarriers based on these materials is under active development.31, 33-35
Concluding Remarks and Future Outlook
Ultrasonic spray methods for preparing nanostructured materials have proven to be powerful tools and the revival of interest in USP over the past decade has been substantial. We have highlighted the diversity of applications and nanostructured materials accessible using ultrasonic spray methods. We expect that future work in this field will focus increasingly on the preparation of novel functional materials developed with specific purposes in mind (e.g., sorbents, catalyst and catalyst supports, sensors, and energetic materials) where the relationship between morphology and function can be readily pursued by exploring new precursors and aerosol synthetic routes.
Acknowledgments
This work was supported in part by the NSF DMR 09-06904, OII-0539385, IIP-0637721, and IIP-0823029. Materials characterizations were carried out in the Center for Microanalysis of Materials at the University of Illinois at Urbana-Champaign, which is partially supported by the U.S. DOE under grants DE-FG02-07ER46453 and DE-FG02-07ER46471.
References
Para continuar lendo, faça login ou crie uma conta.
Ainda não tem uma conta?