Tips & Tricks for IC: A Quick Overview on IQ/ OQ/PV(PQ) of Ion Chromatography Instruments
Dr. Holger Keller, Sr. Product Manager Service1, Matthias Nold, Product Manager, Reference Materials2
1Metrohm AG, 2Merck
Supelco® IQ/OQ/PQ Kit enables an efficient and reliable Instrument Qualification
Introduction
Reliability and consistency of analytical results requires a proper instrument qualification at the time of installation as well as periodic performance checks. This article outlines the tests that should be part of the instrument qualification process for ion chromatography instruments.
Ion (-exchange) chromatography (IC) is a well- established analytical technology that separates ions and polar molecules based on their respective charged groups. Ion chromatography systems consist of the following main components (Figure 1): A pump that moves the mobile phase (eluent; e.g. water), an injector that introduces the sample containing the ions into the mobile phase, a separation column as a stationary phase that holds the ion exchanger material, and finally a detector that registers the ion load after release from the column.
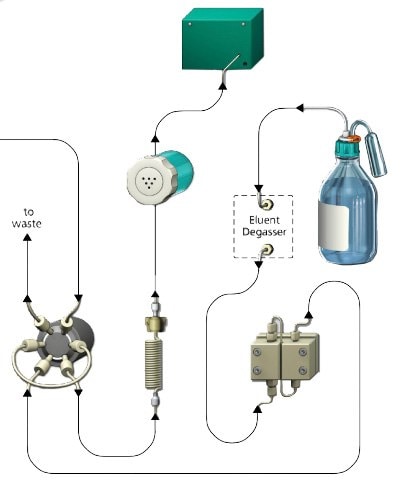
Figure 1.Functional principle IC (example)
IC can handle a wide range of varying analyte concentrations, from parts per trillion to the percent range. IC is commonly used in the pharma, food, and environmental sectors to analyze samples for specific components and to verify compliance with norms and standards.
Today's Ion Chromatographs are sophisticated analytical instruments. To guarantee reliable, reproducible, and traceable results from day one, professional installation and system qualification are key to their success. To keep the instrument in its peak performance over time, regular maintenance and periodic requalification are strongly advised.
During initial qualification or periodic requalification, the system undergoes a range of standardized tests to evaluate performance characteristics of individual and critical system components. Next to mechanical and electronical quality parameters, performance is also tested and evaluated in a series of measurements using traceable Certified Reference Materials (CRMs).
Steps of Instrument Qualification (quick introduction)
Especially in the pharmaceutical industry, instrument qualification and documentation of the findings is a must to fulfill the requirements of the various regulatory bodies. USP <1058> for instance defines the Analytical Instrument Qualification (AIQ) as “the collection of documented evidence that an instrument performs suitably for its intended purpose”. To support customers in this task, the Metrohm Compliance Service has developed standardized test procedures and extensive documentation to comply with these regulatory demands.
Analytical Instrument Qualification Steps (Overview):
- User Requirement Specification (URS) / Risk Assessment (RA)
- Design Qualification (DQ)
- Installation Qualification (IQ)
- Operational Qualification (OQ)
- Performance Qualification (PQ)
- Instrument Discontinuation
Major instrument upgrades: Steps 1 to 5
On going requalification: Steps 4 to 5
This procedure focuses on two key elements of the overall qualification process - Installation Qualification (IQ) and Operational Qualification (OQ).
IQ documents the installation process of the system and ensures that the instrument, software, and accessories have been delivered and are set up correctly at a suitable workplace environment.
OQ encompasses a mechanical/electrical component test, including the calibration of all relevant hardware components, functional specification testing of the installed software, and a holistic system test where the main components are used to execute predefined test sequences with traceable CRM solutions.
To focus as much as possible on the performance evaluation of the system itself, it is essential to exclude or at least minimize as much as possible, sources of error that are not directly linked to the tested components.
One source of error that can easily be controlled, are the standard solutions used in the holistic system tests. Relying on prepared CRM solutions is the safest way to exclude critical sources of error related to standards preparation from raw materials or stock solutions. Such sources of error could be originating from pipetting, weighing, and dilution steps, in addition to other risk factors like possible contamination of glassware and/or tools, and operator performance.
Specific Tests involving Standard Solutions
The holistic test procedures used during IQ/OQ of Ion Chromatography systems can also be applied to periodic system checks to satisfy recommendations and requirements based on GLP (Good Laboratory Practice).
Performance assessment of key components and statistical evaluation of achieved results (e.g., reproducibility and accuracy) should be carried out using a PEEK capillary (0.18 mm ID, 10 m) instead of a column, and pre-prepared TraceCERT® CRM standard solutions.
Test procedures for the main system components include (Table 1):
- Linearity test of detector modules
- Injector tests such as precision, retention time stability, and cross contamination
- Injection volume linearity (e.g. for Metrohm Inline Sample Preparation (MiPT) technique)
- Reproducibility of suppressor chambers

Example 1.Detector test – linearity

Example 2.Injector test - repeatability

Example 3.Injector test - cross contamination

Example 4.Injector test - linearity of injection volumes
IQ/OQ/PQ Kit for Ion Chromatography
This ready to use TraceCERT® IQ/OQ/PQ Kit for Ion Chromatography (Cat. No. 12674) contains six certified bromide standard solutions with nominal concentrations between 5 and 1000 mg/kg as required for the IC instrument qualification tests as described above. The standards are manufactured under ISO 17034 accreditation (accreditation for CRM manufacturers) using high purity sodium bromide and high-purity water (18.2 MΩcm, 0.22 µm filtered) as starting materials.
The product features include:
- Values traceable to NIST SRM
- Expanded Uncertainty provided considering all contribution factors (Figure 5)
- Stability and Homogeneity tested
- The kit includes 6 sodium bromide solutions (See concentrations on next page):
- Bromide Standard 1: 5.00 mg/kg
- Bromide Standard 2: 10.00 mg/kg
- Bromide Standard 3: 20.00 mg/kg
- Bromide Standard 4: 50.00 mg/kg
- Bromide Standard 5: 100.00 mg/kg
- Bromide Standard 6: 1000.0 mg/kg

Figure 5.Contribution factors of uncertainty
To guarantee top reliability of the values for these TraceCERT® certified reference materials, three independent procedures were followed.
After the purity of the starting material is confirmed and if contamination and loss of material are strictly prevented, the solutions are produced gravimetrically. This approach allows the highest accuracy and small uncertainties. The certified value of TraceCERT® reference materials is based on this approach and is directly traceable to the SI unit of kilogram.
The starting material (sodium bromide) is measured against the NIST Standard Reference Material 999 (using argentometric titration), followed by gravimetric preparation using balances calibrated with SI-traceable weights. Consequently, the value calculated by this unbroken chain of comparisons is traceable to the reference to which the starting material is compared.
To underpin the certified gravimetric value, the bottled TraceCERT® solution is compared to a second reference material (NaCl, certified by BAM, Cat No. 71387) by argentometric titration.
For more standards and eluents for ion chromatography visit SigmaAldrich.com/ic
若要繼續閱讀,請登入或建立帳戶。
還沒有帳戶?