Lightweight Metal Matrix Nanocomposites
Prof. P. K. Rohatgi, B. Schultz
University of Wisconsin–Milwaukee
Material Matters 2007, 2.4, 16.
Introduction
Composite materials that traditionally incorporate micron scale reinforcements in a bulk matrix offer opportunities to tailor material properties such as hardness, tensile strength, ductility, density, thermal and electrical conductivity, and wear resistance. With the advent of nanomaterials, nanocomposites are envisioned, and are being developed, with properties that overcome the limitations for metals or composites that contain micron scale reinforcements. For example, carbon nanotubes have been shown to exhibit ultra-high strength and modulus, and have anisotropic electrical conductivity. When included in a matrix, carbon nanotubes could impart significant property improvements to the resulting nanocomposite.1
In the past decade, much work has gone towards developing polymer matrix nanocomposites and many such materials are already used in various applications.2 Metallic composites containing nanoparticles or carbon nanotubes could offer distinct advantages over polymeric composites due to the inherent high temperature stability, high strength, high modulus, wear resistance, and thermal and electrical conductivity of the metal matrix. Aluminum nanocomposites are predicted to surpass the weight reduction currently realized through the use of polymer-based nanocomposites and polymer-based fiber composites in aerospace applications primarily because these metal matrices have higher strength and stiffness (Figure 1). They also have much better thermal stability.

Figure 1.Comparison of potential materials and reinforcements for aerospace applications. (Data for Al-70% CNT is theoretical)
The development of Metal Matrix Nanocomposites (MMNCs), however, is still in its infancy. The MMNCs synthesized to date include Al-B4C, Mg-SiC, Al-CNT, Cu-CNT and Ti-SiC, prepared using powder metallurgy, and Al-SiC, Mg-SiC, Al-Al2O3, Al- CNT, Mg-Y2O3, Al-Diamond, and Zn-SiC, prepared using solidification processing.
Though there is great potential for the use of MMNCs in a variety of applications, their use is hindered by their cost, difficulty in the manufacture of large complex shaped parts and their often poor ductility. This article briefly reviews the state-ofthe- art in metal matrix nanocomposites, with specific emphasis on how these drawbacks are being overcome through proactive design of nanostructures and processing techniques.
Synthesis, Processing and Properties of Metal Matrix Nanocomposites
The greatest challenges facing the development of MMNCs for wide application are the cost of nanoscale reinforcements and the cost and complexity of synthesis and processing of nanocomposites using current methods. As with conventional metal matrix composites with micron-scale reinforcements, the mechanical properties of a MMNC are strongly dependent on the properties of reinforcements, distribution, and volume fraction of the reinforcement, as well as the interfacial strength between the reinforcement and the matrix. Due to their high surface area, nanosize powders and nanotubes will naturally tend to agglomerate to reduce their overall surface energy, making it difficult to obtain a uniform dispersion by most conventional processing methods. In addition, due to their high surface area and surface dominant characteristics, these materials may also be highly reactive in metal matrices. For example, in Al/CNT composites there are concerns that brittle aluminum carbide phases could form during processing, impairing the mechanical properties and electrical conductivity of the nanocomposite. Because of these concerns, processing methods are being developed to produce MMNCs with uniform dispersions of nanomaterials and little deleterious interfacial reactions.
The methods that have been used to synthesize metal matrix nanocomposites include powder metallurgy, deformation processing, vapor phase processing, and in some cases solidification processing. Powder metallurgy involves the preparation of blends of powders of metal and reinforcements, followed by consolidation and sintering of the mixtures of powders to form the part. Deformation processing involves subjecting a metal to high rates of deformation to create nanostructured grains in a metal matrix. Vapor phase processing methods such as chemical vapor deposition (CVD) can be used to deposit thin films creating dispersed multiphase microstructures, multilayered microstructures, or homogeneous nanostructured coatings. Each of these methods can create very desirable microstructures, however they are expensive and difficult to scale up to manufacture large and complex shapes in bulk.
Of the processing methods available for synthesis and processing of MMNCs, the least expensive method for production of materials in bulk is solidification processing. There are various avenues by which researchers have created nanostructures and nanocomposite materials using solidification and these can be divided into three categories
- rapid solidification,
- mixing of nanosize reinforcements in the liquid followed by solidification and
- infiltration of liquid into a preform of reinforcement followed by solidification.
Rapid solidification (implying solidification rates of up to 104–107 °C/s) through methods such as melt spinning (a liquid metal stream is impinged on a spinning copper drum), or spray atomization (a superheated liquid metal is atomized with gas jets and impinged on a substrate) can lead to nanosize grains as well as amorphous metals from which nanosize reinforcements can be precipitated in the amorphous matrix during heating to form nanocomposites.3,4 Mixing techniques involve adding particulate reinforcements and mechanically dispersing them in the matrix. Mixing methods that have been applied to synthesize MMNCs include stir mixing, where a high temperature impeller is used to stir a melt that contains reinforcements, creating a vortex in the melt, and ultrasonic mixing, where an ultrasonic horn is used to create cavitation in the melt that disperses the particulate reinforcements by a gas streaming effect that occurs through the collapse of bubbles within the melt. Infiltration techniques entail infiltrating a preform or partial matrix containing the reinforcements with a liquid metal. The preform consists of particles formed in a particular shape with some binding agent, and can be composed of the additives and binding agent alone or with some portion of the matrix added as a partial filler. Infiltration methods that have been used include ultra high pressure, where the pressure used to infiltrate a high-density preform of nanoparticles is in excess of 1 Gpa, and pressureless infiltration, where a block of metal is melted on top of a lower density preform of nanoparticles and allowed to seep into the preform.5,6
Figure 2 illustrates examples of the different microstructures of Aluminum Alloy-Al2O3 nanoparticle (Product No. 544833) composites that have been produced by different processing methods. Figure 2 A shows a microstructure exhibited by a cast nanocomposite synthesized at UW–Milwaukee by the authors. This MMNC was made using a unique casting method combining the use of stir mixing, and ultrasonic mixing, with a wetting agent added to the molten alloy to incorporate nanoparticles in a metal matrix. This process resulted in the incorporation of nanoparticles within microscale grains of aluminum, and formed a bimodal microstructure. Ceramic nanoparticles may be uniformly dispersed in metal matrices to increase the tensile strength and wear resistance, using methods such as ultrasonic cavitation of the melt to further disperse the particles.7 The influence of nanoscale reinforcements on formation of solidification microstructure including their influence on nucleation, growth, particle pushing, solute redistribution, heat and fluid flow, however, will have to be understood to reproducibly create desired structures. While there is some understanding of the influence of micron size particles on the formation of solidification microstructures, the influence of nanoscale reinforcements on each of the constituents of solidification structure formation need to be studied using both theoretical and experimental research. Figure 2 B shows a transmission electron microscope (TEM) micrograph of the microstructure obtained by ball milling pure metals and nanopowders, followed by hot pressing/sintering to form a nanocomposite. The matrix aluminum and the Al2O3 powders are nanosize in this TEM micrograph and the reinforcement phases are mainly restricted to the grain boundaries, which will likely have a grain boundary pinning effect. Since a much higher percentage of Al2O3 has been added using this process, the resulting sample exhibited a substantial improvement in its wear properties.
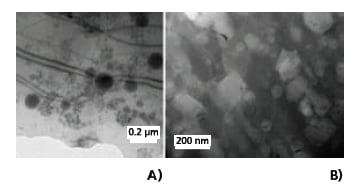
Figure 2.TEM of Aluminum Alloy-Al2O3 nanocomposites produced by liquid and solid based methods. A) Stir cast A206- 2 vol % Al2O3 (47 nm) nanocomposite produced by the authors at UW–Milwaukee.7 B) Powder metallurgy based Aluminum alloy-15 vol% Al2O3.
Great improvements can be achieved in specific material properties by adding only a small percentage of a dispersed nano-phase as reinforcement. Table 1 presents selected studies on MMNCs, the processing techniques used and their respective properties. When the reinforcement in a metal matrix is brought down from micron-scale to nano-scale, the mechanical properties are often substantially improved over what could be achieved using micron-scale reinforcements. This is possibly due to the exceptional properties of the individual nano-phase reinforcements themselves, smaller means free path between neighboring nanoparticles and the greater constraint provided by the higher surface area of nano-phase reinforcements. Nano-phase reinforcements like CNT and SiC (Product No. 594911) have much higher strengths than similar micron-scale reinforcements. In some cases, the nanoscale reinforcement leads to property changes in the matrix itself. For instance, nanoscale reinforcements can lead to nanosize grains in the matrix, which will increase the strength of the matrix. Due to their size, properties of nanomaterials are dominated by their surface characteristics, rather than their bulk properties, which is the case in micronscale reinforcements. The potentially unique interfaces between nanosized reinforcements and the matrix can lead to even greater improvements in the mechanical properties due to the strong interface between the reinforcement phase and the matrix, and through secondary strengthening effects such as dislocation strengthening. Figure 3 shows that as the particle size of Al2O3 goes from micron to nanosize, there is significant decrease in the friction coefficient and wear rate of aluminum composites. In addition, the incorporation of only 10 volume percent of 50 nm sized Al2O3 particles to the aluminum alloy matrix resulted in an increase of the yield strength to 515 MPa.8 This is 15 times stronger than the base alloy, 6 times stronger than the base alloy with 46 volume percentage of 29 micron size Al2O3 and over 1.5 times stronger than AISI 304 stainless steel.

Figure 3.Effect of particle size on wear rate and coefficient of friction of Al-15vol% Al2O3 metal matrix composites. Both the wear rate and coefficient of friction are dramatically reduced when the particle size is reduced below 1 μM
Recently, an aluminum alloy specimen reinforced with CNTs was synthesized using pressureless infiltration.6 CNTs were mixed together with aluminum and magnesium powders using ball milling and then pressed into preforms that were subsequently infiltrated by melts of the aluminum alloy matrix at 800 °C in a nitrogen atmosphere. The CNTs were observed to be well-dispersed and embedded in the matrix. Further experiments showed that up to 20 volume percent of nanotubes could be incorporated in the matrix of aluminum alloys using this process. The wear data also suggests that the presence of CNTs in the matrix can reduce the direct contact between the aluminum matrix and the steel pin and thereby decrease the friction coefficient due to the presence of carbon nanotubes. By reducing the friction coefficient, the energy loss experienced by components in frictional contact will be reduced, improving efficiency of mechanical systems. In addition, the authors believe that the incorporation of CNTs having relatively short tube lengths may allow them to slide and roll between the mating surfaces and result in a decrease of the friction coefficient.6 Ploughing wear appeared to be the dominant wear mechanism under the dry sliding condition. The depth of the wear grooves caused by ploughing wear decreased with increasing CNT content, suggesting that the strengthening effects of nanotubes increased the wear resistance of aluminum alloy-CNT nanocomposite.
Though nanocomposite materials exhibit ultra high-strength, there is often a trade-off that results in decreased ductility. This may be attributed to currently used processing methods that result in the formation of voids and defects, as well as to the inability of nanostructured grains or additives to sustain a high rate of strain hardening. These shortcomings, among other microstructural effects, lead to instabilities upon plastic deformation. One of the methods that has been used to overcome the lack of ductility in nanostructured materials is to incorporate nanosize dispersoids in a bimodal or trimodal microstructure. In the case of nanostructured grains, the presence of hard precipitates or nanoparticles in a metal matrix may act to initiate, drag and pin dislocations, reducing dynamic recovery, and thus resulting in a high strain-hardening rate that, in turn, produces larger uniform strains and higher strengths in the MMNC, along with higher ductility.15
The potential for achieving much higher strengths in combination with acceptable ductility in MMNCs has been demonstrated by E. Lavernia and coworkers.16 A mixture of a 5083 aluminum alloy powder and micron-sized boron carbide particles that had been coated with a powdered, nanostructured aluminum alloy were milled at cryogenic temperatures (cryomilled). This cryomilled powder was then mixed with regular 5083 alloy and consolidated and extruded to form nanocomposites with almost double the strength of the monolithic 5083 alloy. Cigar-shaped nanocomposite volumes of material that contained micron-sized B4C reinforcements were observed to be dispersed in nanograin sized aluminum matrix regions that were embedded in micro-grain sized 5083 aluminum matrix having no B4C reinforcements. This combined bimodal and trimodal microstructure (Figure 4) is presumed to be the source of the exceptional combination of strength and ductility in aluminum matrix nanocomposites that had micron size B4C particles used as reinforcements. Apparently, the micron grain-sized aluminum matrix that did not contain any reinforcement, enabled dislocation motion and improved ductility. This type of combined bimodal and trimodal microstructure in MMNCs will need to be synthesized using less expensive solidification processing routes that can enable processing of large components having complex shapes. By exploring lower cost and more versatile methods to manufacture metal matrix nanocomposites with improved ductility, these materials are expected to become commercially viable for a variety of applications, particularly where weight savings is essential.

Figure 4.TEM micrographs showing alternate stacking of course grain size Al and nanostructured Al regions. The B4C particles are uniformly distributed within the nanostructured aluminum exclusively.
Current and Future Applications
Metal matrix composites with micron-size reinforcements have been used with outstanding success in the automotive and aerospace industries, as well as in small engines and electronic packaging applications. In the case of metal matrix nanocomposites, incorporation of as little as one volume percentage of nanosize ceramics has lead to a much greater increase in the strength of aluminum and magnesium base composites than was achieved at much higher loading levels of micron-sized additions. Such potential improvements have great implications for the automotive and aerospace, and, in particular, the defense industries due to the drastic weight savings and exceptional properties that can be achieved. Potential aerospace applications may include ventral fins for aircrafts, as well as fan exit guide vanes for commercial airline jet engines. Both components require high stiffness and strength, low weight as well as resistance to erosion from rain, airborne particulates and hail. Components used in the automotive industry where bulk nanocomposites would likely be valuable include brake system components, which require high wear resistance, and thermal conductivity, intake and exhaust valves, which require high creep resistance and resistance to sliding wear, as well as piston liners, which require high wear resistance, good thermal conductivity and low coefficient of thermal expansion. In addition, exceptionally high thermal conductivities, possible in selected nanocomposites, will find applications in thermal management applications in computers. Metal matrix nanocomposites can be designed to exhibit high thermal conductivity, low density, and matching coefficient of thermal expansion with ceramic substrates and semiconductors, making them ideal candidates for such applications.
Concluding Remarks
There are exciting opportunities for producing exceptionally strong, wear resistant metal matrix nanocomposites with acceptable ductility by solidification processing and powder metallurgy. A fundamental understanding, however, must be gained of the mechanisms that provide these improvements in properties if such materials are to find wider commercial application. Moreover, processing methods must be developed to synthesize these materials in bulk, at lower cost, with little to no voids or defects, and with improved ductility, possibly as a result of bimodal and trimodal microstructures. Metal matrix nanocomposites can lead to significant savings in materials and energy and reduce pollution through the use of ultra-strong materials that exhibit low friction coefficients and greatly reduced wear rates.
References
Per continuare a leggere, autenticati o crea un account.
Non hai un Account?