Molecular Layer Deposition of Organic and Hybrid Organic-Inorganic Polymers
Steven M. George1,2, Byunghoon Yoon1
1Department of Chemistry and Biochemistry, 2Department of Chemical and Biological Engineering, University of Colorado, Boulder, Colorado 80309
Material Matters 2008, 3.2, 34.
Introduction
Atomic layer deposition (ALD) techniques have emerged in the last ten years to meet various needs including semiconductor device miniaturization, conformal deposition on porous structures and coating of nanoparticles. ALD is based on two sequential self-limiting surface reactions.1,2 Because the surface chemical reactions are self-limiting, ALD can deposit very conformal ultra-thin films on high aspect ratio structures.3 The control of the ALD growth is ~1 Å per reaction cycle and the resulting ALD films are continuous and pinhole-free.4
ALD processes have been developed for a wide variety of inorganic materials. Because of the binary nature of the ALD reaction sequence, most ALD materials are binary compounds such as Al2O3 and TiN. For example, Al2O3 ALD is usually performed using Al(CH3)3 (TMA, Prod. No. 663301) and H2O as the two reactants.5,6 TiN ALD can be performed using TiCl4 (Prod. No. 254312) and NH3 (Prod. No. 294993) as the two reactants.7 The most common ALD materials are metal oxides and metal nitrides. Several reviews have detailed the many inorganic materials that have been deposited using ALD techniques.8,9
Molecular layer deposition (MLD) is closely related to ALD.10,11 MLD is also based on sequential, self-limiting surface reactions. However, a “molecular” fragment is deposited during MLD reactions as shown by the schematic in Figure 1.10 This molecular fragment is organic and can contain inorganic constituents. The deposition of purely organic polymer MLD films can be achieved using step-wise condensation reactions. The growth of these organic polymer MLD films was first demonstrated by several groups in Japan.11–15 Hybrid organicinorganic films can be deposited by simply mixing organic and inorganic reactants.

Figure 1. Schematic of the molecular layer deposition (MLD) method based on sequential, self-limiting surface reactions.
Molecular Layer Deposition of Organic Polymers
The initial investigations of the MLD of organic polymers concentrated on polyimides11 and polyamides.14 These early demonstrations of MLD were also known as alternating vapor deposition polymerization.14 The basic strategy was to utilize homobifunctional reactants with two chemical functionalities such as X-A-X and Y-B-Y. “X” and “Y” are chemical functional groups and “A” and “B” are organic fragments. A two-step AB cycle with two homobifunctional reactants is as follows:
(A) SBY* + XAX → SB–AX* + XY (1)
(B) SAX* + YBY → SA–BY* + XY (2)
where the asterisks indicate the surface species. The underlying substrate and deposited film are represented by “S”. In the A reaction, the X chemical functionality reacts with SBY* species to deposit SB-AX* species. In the B reaction, the Y chemical functionality reacts with SAX* species to deposit SA-BY* species.
Recent work has explored the MLD of two polyamides: nylon 66 (Prod. No. 429244)10 and poly(p-phenylene terephthalamide) (PPTA).16 The reactants for nylon 66 MLD are adipoyl chloride (ClOC-(CH2)4-COCl) (AC, Prod. No. 165212) and 1,6-hexanediamine (H2N-(CH2)6-NH2) (Prod. No. H1169-6).10 The reactants for PPTA MLD are terephthaloyl chloride (TC, Prod. No. 120871) and p-phenylenediamine (PD, Prod. No. 695106).16 In both cases, the acid chloride and amine functional groups react to form an amide linkage. Sequential exposures of AC and HD for nylon 66 MLD or TC and PD for PPTA MLD were used to deposit these polyamide films.10,16 A schematic of the surface chemistry during PPTA MLD is shown in Figure 2.16

Figure 2. Illustration of the surface chemistry for poly(p-phenylene terephthalamide) MLD using (a) terephthaloyl chloride and (b) p-phenylenediamine as the homobifunctional reactants.
One of the difficulties with using homobifunctional reactants for polymer MLD is that the homobifunctional reactant can react twice with two chemical groups on the surface.16 These “double” reactions remove two surface chemical groups from further reaction. The number of reactants that can react with the surface is reduced considerably after a number of double reactions. Consequently, future strategies for organic polymer MLD could employ heterobifunctional reactants or reactants with masked or protected functionalities.16
Extension to Hybrid and Organic-Inorganic Polymers
The MLD of hybrid organic-inorganic polymers can be achieved by using an inorganic reactant together with an organic reactant.17 This extension is achieved by combining one of the reactants used in a typical ALD process with one of the reactants used in a MLD process for an organic polymer. For example, Al(CH3)3, trimethylaluminum (TMA), is a very common reactant used for Al2O3 ALD.5,6 TMA reacts readily with oxygen containing species. A diol, such as ethylene glycol (HO-(CH2)2-OH), (EG, Prod. No. 324558) is a homobifunctional reactant that could be used together with a carboxylic acid or acid chloride to deposit a polyester in a step-wise MLD process. Together, TMA and EG can be used in a sequential, step-wise process to deposit a hybrid organicinorganic polymer known as an alucone.18
A new family of reactions is possible between metal alkyls such as TMA with diols such as EG. The general two-step MLD reaction between the metal alkyl and the diol can be written as follows.17
(A) SMR* + HOR’OH → SM-OR’OH* + RH (3)
(B) SR’OH* + MRx → SR’O-MRx–1* + RH (4)
In the A reaction, the reaction stops when all the SMR* species have completely reacted to produce SM-OR’OH* species. In the B reaction, the reaction stops when all the SR’OH* species have completely reacted to produce SR’O-MRx–1 * species.The sequential reactions of TMA and EG during MLD yield a polymeric film described by (Al-O-CH2-CH2-O-)n This new polymer is an alucone18 and can be called poly(aluminum ethylene glycol).17 A schematic illustrating the growth of poly(aluminum ethylene glycol) is shown in Figure 3.17

Figure 3. Illustration of the surface chemistry for poly(aluminum ethylene glycol) MLD using (a) trimethylaluminum as a homotrifunctional reactant and (b) ethylene glycol as a homobifunctional reactant.
Previous investigations have shown that alucone MLD using TMA and EG is very efficient.17 Ex situ x-ray reflectivity (XRR) analysis revealed that the MLD growth rate was temperature dependent.17 The alucone MLD growth rates decreased from 4.0 Å per TMA/EG cycle at 85 °C to 0.4 Å per TMA/EG cycle at 175 °C. Figure 4 shows that the alucone MLD is very linear versus number of TMA/EG cycles.17 The XRR analysis also determined that the density of these alucone films was independent of the deposition temperature and constant at ~1.5 g/cm3. This measured density for the hybrid organicinorganic alucone MLD film17 is much less than the density of ~3.0 g/cm3 for an Al2O3 ALD film grown at 177 °C.19
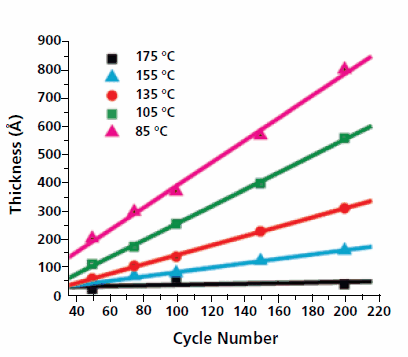
Figure 4. Thickness of the poly(aluminum ethylene glycol) MLD film versus number of cycles of trimethylaluminum and ethylene glycol at different growth temperatures determined using x-ray reflectivity measurements.
Many other organometallic precursors can be used to define hybrid organic-inorganic MLD polymers. For example, zinc alkyls such as Zn(CH2CH3)2, diethylzinc (DEZ, Prod. No. 668729), can react with diols such as EG in a similar MLD process.20 Various other metal alkyls that can easily react with oxygen are also possible candidates for hybrid organic-inorganic polymer MLD. For example, metal alkyls based on magnesium (Mg) and manganese (Mn) react readily with oxygen and are possible candidates to react with diols. Metal alkyls of Mg and Mn are available as Mg(Cp)2 (Prod. No. J100042) and Mn(Cp)2 (Prod. No. 415405) where Cp is the cyclopentadienyl ligand. Other possible metal alkyls are ferrocene, Fe(Cp)2(Prod. No. F408), nickelocene, Ni(Cp)2(Prod. No. N7524), and cobaltocene, Co(Cp)2(Prod. No. 339164). The possibilities are virtually unlimited given all the metals on the periodic table.
The reactions based on diols will produce hybrid organicinorganic MLD films that will be composed of a metal oxide and an organic constituent. Other homobifunctional organic reactants are possible that would further expand the generality of these reactions. For example, the homobifunctional organic reactant could be a diamine or a dithiol. For the diamines and the dithiols, the hybrid organic-inorganic MLD film would be composed of a metal nitride or metal sulfide and an organic constituent.
Future Prospects for Additional Organic and Organic-Inorganic Polymers
To prevent “double” reactions, MLD reactions can utilize heterobifunctional reactants.16 These reactants have two chemical functional groups that are different. One of the chemical functional groups can react with the surface species. The second chemical functional group cannot react with the surface species. The heterobifunctional reactants react only monofunctionally and prevent double reactions and polymer chain termination.
The simplest two-step AB cycle using heterobifunctional reactants is:
(A) SBZ* + WAX → SB–AX* + ZW (5)
(B) SAX* + YBZ → SA–BZ* + XY (6)
In the A reaction, the W chemical functionality (but not the X chemical functionality) reacts with the SBZ* species to deposit SB-AX* species. In the B reaction, the Y chemical functionality (but not the Z chemical functionality) reacts with the SAX* species to deposit SA-BZ* species. There are a variety of examples of heterobifunctional reactants that display two separate chemical reactivities on the same molecule. Possible chemical functional groups are amine, allyl, hydroxyl, isocyanate, epoxy, succinimide ester, maleimide and thiol.
In addition to heterobifunctional reactants, the reactant can also avoid a double reaction by containing a concealed functionality that only expresses itself upon reaction. There are a variety of ring-opening reactions that react to yield a new hydroxyl (-OH), amine (-NH2) or carboxylic acid (-COOH). For example, an epoxy ring can react with a surface amine to yield a hydroxyl group. A cyclic azasilane, such as 2,2-dimethoxy- 1,6-diaza-2-silacyclooctane, can react with a surface hydroxyl to yield amine groups.16 A cyclic carbonate, such as ethylene carbonate, can react with a surface amine to yield a hydroxyl group.16 Examples of various reactions involving ring-opening or heterobifunctional reactants are shown in Figure 5.

Figure 5. Examples of various reactions involving ring-opening or heterobifunctional reactants.
The MLD of organic and hybrid organic-inorganic polymers can also be accomplished using a three-step reaction sequence. Possible three-step ABC reactions increase the flexibility of MLD reactions to include various organic compositions. In addition, three-step ABC reactions also increase the number of different combinations of possible heterobifunctional reactants that can be utilized to define the MLD process. One example of a three-step ABC reaction is the sequential reaction of TMA, ethanolamine (EA, Prod. No. 398136) and maleic anhydride (MA, Prod. No. M188).21 This reaction sequence incorporates a metal alkyl reactant, a heterobifunctional reactant and a ring-opening reactant. A schematic of the three-step ABC reaction is shown in Figure 6.21

Figure 6. Illustration of the surface chemistry for the three-step ABC reaction involving (a) trimethylaluminum as a homotrifunctional reactant, (b) ethanolamine as a heterobifunctional reactant and (c) maleic anhydride as a ring-opening reactant.
This three-step ABC reaction sequence avoids the possibility of double reactions and leads to very robust and linear MLD growth. Recent studies have shown that this ABC alucone MLD film grows at temperatures of 90–150 °C and yields MLD growth rates of 23–8 Å per ABC reaction cycle, respectively.21 Other possible three-step ABC reaction sequences using heterobifunctional reactants, ring-opening reactants and reactants with masked or protected functionalities will offer a wide range of possibilities for the MLD of organic and hybrid organic-inorganic MLD films. These new combinations, together with previous ALD processes, will significantly increase the range of thin film materials that can be deposited conformally with precise thickness control.
Acknowledgments
This work was funded by the National Science Foundation under Grant CHE-0715552. Additional support was provided by the Air Force Office of Scientific Research. The authors also thank Dr. Arrelaine A. Dameron, Dragos Seghete, Nicole M. Adamczyk and Dr. Yijun Du for their previous contribution to our understanding of MLD.
Para seguir leyendo, inicie sesión o cree una cuenta.
¿No tiene una cuenta?