Silicon Carbide: The Return of an Old Friend
Nicholas G. Wright, Alton B. Horsfall
School of Electrical, Electronic and Computer Engineering Newcastle University Newcastle upon Tyne, UK
Material Matters Volume 4 Article 2
In recent years silicon carbide, SiC, has re-emerged as a vital technological material that is crucial in many materials and engineering applications. Interestingly, SiC is one of the few minerals that were first created synthetically and subsequently discovered in nature. It was first artificially synthesized in 1891 by Edward Acheson as a result of unexpectedly discovering small black crystals of SiC in an electrically heated melt of carbon and alumina.1 The subsequent refinement of this technique (the so-called Acheson process) led to the commercial production of large volumes of small SiC crystals (ground into powder form) for use as an industrial abrasive.2 In 1905, silicon carbide was observed in its natural form by the Nobel-prize-winning chemist Henri Moissan in Diablo Canyon, Arizona. The transparent mineral, now known as moissanite, is almost as brilliant and as hard as diamond, and is therefore often used as a gemstone. To date, no large natural deposits of SiC have ever been found in nature so all SiC used today is synthetic.
In the present day, SiC is one of the most widely used materials that plays a critical role in industries such as: aerospace, electronics, industrial furnaces and wear-resistant mechanical parts among others. Although SiC is widely used in electronics and other high technology applications, the metallurgical, abrasive, and refractory industries are dominating by volume.
Crystal Structure
Silicon carbide has a layered crystal structure which occurs in a number of different forms or polytypes. Composed of carbon and silicon, in equal amounts, each atom is bonded to four atoms of the opposite type in a tetrahedral bonding configuration. There are three possible arrangements of atoms in a layer of SiC crystal known as the A, B and C positions, and each polytype has the same layers but a different stacking sequence (Figure 1).3 As a given layer may be stacked on top of another in a variety of orientations (with both lateral translations and rotations being feasible energetically), silicon carbide may occur in a wide variety of stacking sequences—each unique stacking sequence generating a different polytype (e.g., cubic, hexagonal and rhombohedral structures can all occur). The hexagonal and rhombohedral structures, designated as the α-form (noncubic), may crystallize in a large number of polytypes whilst, to date, only one form of cubic structure (designated as the β-form) has been recorded. Designation4 is by the number of layers in the sequence, followed by H, R, or C to indicate whether the type belongs to the hexagonal, rhombohedral, or cubic class. To date, over 215 polytypes have been recorded— although only a limited number are of interest technologically (principally the 4H and 6H hexagonal plus the 3C cubic forms).5 This interest is driven by the commercial availability of substrates and the low mobility anisotropy (difference in carrier mobility with crystallographic direction) for these polytypes.
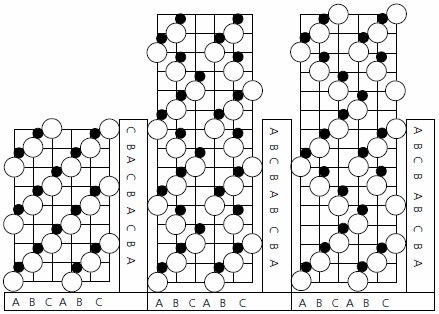
Figure 1. Stacking sequences of the Crystal structures of (a) 3C SiC, (b) 4H SiC, and (c) 6H SiC.
The term “silicon carbide” is commonly used to describe a range of materials that are in fact quite distinct. Mechanical engineers may use it to describe ceramics which are fabricated from relatively impure SiC crystallites bonded together with various binders under temperature and/or pressure, while electrical engineers may use the term to describe high purity single crystal wafers of SiC.
Applications Based on Mechanical Properties
All forms of silicon carbide are well known as hard materials occupying a relative position on Mohs’ scale between alumina at 9 and diamond at 10.6 Because of its high thermal conductivity and low thermal expansion, silicon carbide is very resistant to thermal shock as compared to other refractory materials.6 Until the recent emergence of silicon carbide as a significant material for electronics, the mechanical properties of SiC-ceramics were the dominant commercial interest.
The formation of SiC powder is an essential pre-requisite to the manufacturing of many types of ceramic articles, which are subsequently obtained by shaping the manufactured silicon carbide powder. SiC powders with variable purity levels, crystal structures, particle sizes, shapes, and distributions can be prepared via several routes. Methods that have been examined include: growth by sublimation carbothermic reduction (the Acheson Process), conversion from polymers and gas phase chemical reactions.
Although brittle in nature, silicon carbide ceramics are leading materials for rotating and static components in many mechanical applications. They are characterized by low fracture toughness and limited strain-to-failure as compared to metals. The strength of a silicon carbide ceramic component is generally determined by pre-existing flaws introduced into the material during processing. The type, size, shape, and location of the flaws vary considerably and, consequently, so does the strength. Silicon carbide ceramics made by different techniques also have quite distinct mechanical properties. For example, sintered silicon carbide retains its strength at elevated temperatures and shows excellent time-dependent properties such as creep and slow crack growth resistance. In contrast, reaction-bonded SiC, because of the presence of free silicon in its microstructure, exhibits slightly inferior elevated temperature properties.7
The extreme hardness of silicon carbide leads to its use as a coating when wear resistance is important, such as brake linings and electrical contacts, and in non-slip applications such as floor or stair treads, terrazzo tile, deck-paint formulations, and road surfaces. SiC is also commonly used in mechanical seals found in pumps, compressors, and agitators in a wide variety of demanding environments including highly corrosive ones. Silicon carbide is harder, yet more brittle, than other abrasives such as aluminum oxide (Prod. No. 202606). Because the grains fracture readily and maintain a sharp cutting action, silicon carbide abrasives are usually used for grinding hard, low tensile-strength materials such as chilled iron, marble, and granite, and materials that need sharp cutting action such as fiber, rubber, leather, or copper. Silicon carbide is also used in a loose form for lapping; mixed with other materials to form abrasive pastes, or used with cloth backings to form abrasive sheets, disks, or belts.6
Applications Based on Electronic and Optical Properties
In recent years, SiC has emerged as a promising material for electronics.8,9 Silicon carbide is considered a wide bandgap material since the electronic bandgaps of the different polytypes range from 2.4eV to 3.3eV (c.f., silicon with a bandgap of 1.1eV).10 In some respects, such a wide range of bandgaps is unexpected— particularly when the crystal structures of the polytypes differ only in the stacking sequence of otherwise identical bilayers (Figure 1). Research in recent years has enabled the development of processing techniques that enable the material properties of silicon carbide to be modified successfully for electronics, in particular power electronics and sensors.11 In addition, silicon carbide is commonly used as a substrate material for light emitting diodes where it acts as a foundation on which optically active layers can be grown. This growth utilizes the close lattice match between 6H SiC, gallium nitride and the high thermal conductivity of SiC to remove the heat generated in the LED.
One application where silicon carbide is making a big impact is gas sensors.12 Its wide band gap gives it very low intrinsic carrier concentration, making sensing possible in very hot gases, such as the pollutants released in combustion engines and the sulphurous emissions from volcanic vents. A typical silicon-carbide gas sensor is about 100 μm across and a fraction of a millimeter thick, and are typically based on a capacitor (MIS structure) with a catalytic contact as shown in Figure 2.13 The dielectric layer allows these devices to operate at temperatures in excess of 900°C,14 by separating the metal from the silicon carbide. In this technology, dielectric layers are typically metal oxide materials such as TiO2, or HfO2 (Prod. Nos. 203394 and 202118), which can be deposited in a variety of manners—including in-situ oxidation of metal layers or more sophisticated techniques such as Atomic Later Deposition with relevant precursors.15 When the metal surface is exposed to a gas mixture, it speeds up the breakdown of the gas molecules, releasing ions that modify the electrical properties of the device. For hydrogen and hydrogen containing molecules, the hydrogen atoms can diffuse easily through thick or dense catalytic contacts to form the charged layer following decomposition of the gas molecule that occurs at temperatures above 150 °C in the sub-millisecond time scale.16 The response of the sensor can be measured via a number of methods including: capacitance shift, voltage shift required to maintain capacitance, or the leakage current through the dielectric layers. The high electrical response speed makes silicon carbide sensors suitable for the detection of gas species in rapidly varying environments, such as close to the manifold region in car exhausts,17 unlike conventional ceramic based sensors, which have a response time in the region of 10 seconds under these conditions.18

Figure 2. Cross-section of a SiC gas sensor. The SiO2 layer is used to reduce the leakage current at high operating temperatures, due to the high band offsets and to reduce the defect density at the SiC/SiO2 interface (Figure reproduced with permission from ref. 14. © 2007 IEEE). The SiC comprises a heavily doped substrate, which is typically 350μm thick and a lightly doped epilayer of a few μm thickness.
Disentangling the effects of the different gases to determine the composition of a mixture is not easy. At temperatures above 600 °C the gas species dissociate completely at the metal surface, making it impossible to identify individual gases. For example, molecules of methane and ethane produce four and six hydrogen ions, respectively, when completely dissociated. This means that we cannot distinguish between a given concentration of methane and two-thirds of that concentration of ethane since both produce the same number of hydrogen ions. Below a temperature of 150 °C, the dissociation of gas species at the catalytic surface does not occur and the sensors do not respond to the gas at all. Between 150 °C and 600 °C the gas species dissociate only partially, and an array of sensors, with different characteristics to uniquely identify the gases present, can be used. For example, palladium is more sensitive to hydrogen and platinum to ammonia, so using one sensor with each metal allows these gases to be distinguished. Complex computer algorithms such as “Gaussian mixed modes” and “primary component analysis” are then used to decompose the measured electrical response of the devices into the known responses to each individual gas. As a consequence of these effects, the sensitivity of such devices to different gases does vary with temperature, although calibration can be used (as with all sensors) to produce accurate and reproducible readings (Figure 3).

Figure 3. Variation in sensitivity with temperature for a typical SiC gas sensor (Figure reproduced with permission from ref. 14. © 2007 IEEE).
Conclusion
Silicon carbide has emerged as a crucial technological material in recent years; not just for mechanical use, but also as an electronic and optical material. Its excellent material properties and the emergence of underpinning material processing techniques promise a bright future for silicon carbide in many areas of science and engineering.
References
如要继续阅读,请登录或创建帐户。
暂无帐户?