Kinetic Energy Harvesting by Magnetostrictive Materials
Daniele Davino
Department of Engineering University of Sannio, 82100 Benevento, Italy
Introduction
A significant limiting factor for wearable electronics and wireless sensors is the finite amount of energy that can be stored in on-board batteries. Currently, the most common solution is to change or recharge the batteries as often as necessary, but this strategy is neither practical nor economical. For example, the replacement or recharge of batteries used in remote wireless sensors located in far-away or difficult-to-access locations in the environment needs qualified technicians to reach the sensors. This can significantly increase maintenance costs.
Energy harvesting has the potential to be a strategic enabling concept for modern wireless electronic equipment.1 Several methods enable harvesting energy from the environment using methods that rely on the properties of suitable multifunctional materials. For example, magnetostrictive or piezoelectric materials have constitutive relationships that directly couple mechanical and/or thermal variables to electro- or magnetic-variables.
This article discusses the physics, engineering, and application of energy harvesting using magnetostrictive materials. These devices are conceptually simple since their characteristics are based largely upon the properties of the materials. As a result device performance can be improved based on optimized materials characteristics.
Magnetostrictives (or, in general, magnetoelastic materials) have the peculiar characteristic of showing a non-negligible coupling between macroscopic mechanical variables, stress σ and strain ε, and magnetic field H and induction B.2,3 This coupling is exploited for actuation purposes by applying a relevant magnetic field to obtain a macroscopic elongation, known as “magnetostriction.” The magnetostrictive effect is exhibited by several common materials, including iron and nickel, but its macroscopic effect is limited to about 12 ppm and –50 ppm, respectively. A positive magnetostriction indicates elongation; whereas, a negative magnetostriction indicates contraction. Alloys like Terfenol (terbiumdisprosium-iron alloy),5,6 Galfenol (gallium-iron alloy),7 and Alfenol (aluminium-iron alloy)8 exhibit giant magnetostriction with elongations up to 2,000 ppm. More information on magnetostrictive materials can be found in Reference 2. Magnetic coupling can also be exploited in reverse, and is then known as the “Villari effect”4 or inverse magnetoelastic effect.
Here a cyclic mechanical stress applied to magnetostrictive material leads to a cyclic magnetization. Since this effect is obtained over time because of the Faraday-Neumann induction law, a pick-up coil wound around the material experiences an induced voltage, and faster cycling leads to higher voltage. This forms the basis of kinetic energy harvesting (KEH) by magnetostrictive materials. If the varying stress is suitably driven by vibrations in the surroundings, then vibrational energy can be converted into electrical energy using this technique.
The first section of this article reviews the main macroscopic properties of magnetostrictive materials. The second section presents the principle of KEH using magnetostrictive materials, along with relevant material properties.
Magnetostrictive Materials Behavior
Magnetostrictive materials have some common macroscopic properties. Figure 1 shows the uniaxial magnetostrictive behavior of a Terfenol-d rod in which the effect is measured along a field applied along the rod axis. Figure 1A shows the magnetostriction curves (ε vs. H). The following features are noted: 1) the hysteresis; 2) the symmetric behavior with respect to H (as two butterfly wings); and 3) the dependence of curves on the applied compressive stress. It is worth noting that the dependence on the applied compressive stress is somewhat complex. Figure 1B shows the consequence of the Villari effect: the B vs. σ plot at different applied magnetic fields. Again, it is worth noting the hysteresis (except for the case at H = 0 kA/m, because of the very small magnetic induction) and the complex behavior with respect to applied stress and magnetic field. The latter characteristic is important to infer the harvesting potentialities of the material. Indeed, the larger magnetic induction variation, ΔB at a certain stress variation, Δσ yields better energy conversion. Other magnetostrictive materials like Galfenol show similar behaviors in same conditions.

Figure 1. A) Magnetostriction of a Terfenol-d rod at different compressive stresses. B) Cyclic magnetic induction due to cyclic compressive stress (Villari effect) at different magnetic fields.
Mechanical impedance matching of the harvester is another important property of magnetostrictive materials for KEH. Materials like Terfenol or Galfenol are quite rigid with a mechanical behavior near that of bulk iron (Figure 2). The ideal vibrations should have high stresses and low strains, in the 0−1,000 ppm range. The availability of softer magnetoelastic materials would enable vibration harvesting with lower stresses and higher strains, in the 0.1−1% range, with a rubber-like behavior.
Another magnetoelastic material, Metglass, has been proposed for energy harvesting.9,10 The main advantage of Metglass is that it can be laminated to achieve a higher energy density. The material is a Fe-based amorphous ribbon with excellent magnetic softness and elastic response, and its production is in principle cheaper than Fe-Ga and Fe-Tb-Dy alloys.

Figure 2.Mechanical characteristic of a Terfenol-d rod at different constant magnetic fields.
Kinetic Energy Harvesting Devices
The Villari effect is the principle behind the construction of any kinetic energy harvesting device based on magnetostrictive materials. The full exploitation of the process requires several functional components—from the environment to the end user (Figure 3). A suitable mechanical frame is needed to channel the environmental vibrations to the magnetostrictive material and, therefore, its design is of paramount importance to achieve maximum transfer of the mechanical energy.
Two conceptual implementations of the mechanical part are sketched in Figure 4. Figure 4A shows where active material is used between the source of vibrations and a reference frame.11 The magnetostrictive rod (gray) is bound to a rigid frame and undergoes a time-variable uniform z-axis force. Then, z-axis directed compressive stress appears, and the material generates a time-variable magnetization. Figure 4B is suitable when a vibrating frame is available.12 Here a magnetostrictive cantilever beam is rigidly connected to the vibrating frame on one end and to a heavier mass on the other end. Because of the induced oscillations over the mass, the material undergoes a longitudinal stress that leads to timevariable magnetization. Both methods share some common needs: a coil wrapped around the magnetostrictive material and a magnetic circuit to convey and close the magnetic flux lines. The latter is not shown in Figure 4 for the sake of clarity.
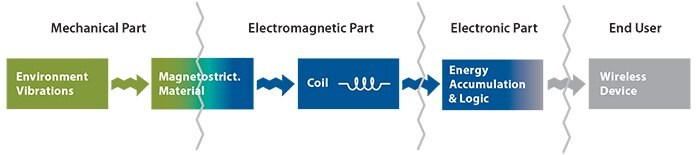
Figure 3.Schematic representation of the functional process behind the kinetic energy harvesting by magnetostrictive materials.

Figure 4. Two schemes for kinetic energy harvesting with magnetostrictive materials: A) forcedriven and B) velocity-driven.
Both methods have their advantages. Figure 4A has no lower bound frequency limit, but it is usually bulkier than Figure 4B. The latter has a passband frequency character because of the intrinsic resonant behavior of the cantilever beam-mass system, and it operates best with vibrations around the resonant frequency of the system. Of course, several solutions have been adopted to expand the operating band and circumvent the issue.13
Figure 3 shows that the electronics aimed for the optimization and accumulation of electric energy represent the “electric load” of the harvesting device. Its development for KEH devices based on magnetostrictives is still in an early stage, while much research and many applications have been proposed for KEH based on piezoelectrics.14 In general, any kinetic energy harvester is an unregulated AC power supply that must be followed by an electronic circuit with a suitable strategy in order to accumulate electric energy. Moreover, the presence of a magnetostrictive material gives some further peculiarities; however, in principle, the development could follow, mutatis mutandis, that has been already done for piezoelectrics.
The system can also be understood from the electro-mechanical point of view by considering it as a spring-mass-damper system. The damping is due to both the mechanical friction and the energy harvesting as the Villari effect also dissipates part of the mechanical energy.15 The material acts as a sort of electro-mechanical transformer where on the “primary” we have complementary mechanical quantities (force and velocity), while on the “secondary” we have complementary quantities (voltage and current) at the coil terminals.16 The voltage v(t) is proportional to the rate of change of the magnetic induction, ∂B/∂t and to usual geometrical and magnetic parameters such as the number of windings, the area of the coil, the magnetic circuit characteristics, etc. By exploiting this property, the following relation holds (Equation 1):

The factor ∂σ/∂t is related to the frequency of vibrations and it is controlled by the vibrations source. The first factor is called “piezomagnetic coefficient” and it is a characteristic of the material, discussed in the next section.
The Piezo-magnetic Coefficient
The definition of the piezo-magnetic coefficient is the following (Equation 2):17,18

In other words, it is the rate of change of B with respect to σ at constant H. This parameter is usually considered constant in datasheets and in linear models of the materials.18 Such an approximation is acceptable in some cases; for example, if the material is employed in actuators where, usually, a mechanical pre-stress higher than the maximum allowed external stress is applied to the device.19 On the other hand, if unknown dynamic conditions are considered, as in the case of energy harvesting applications, then the general definition must be exploited. The piezomagnetic parameter, being a particular derivative function of the material characteristics, is nonlinear with respect to the (H,σ) couple and, moreover, shows hysteresis. Nevertheless, it can be obtained from a numerical derivative of the experimental hysteresis loops.17 A result of this operation is shown in Figure 5 for a Terfenol-d rod. Its value is in the range of 10–8 m/A, as reported in literature,20 but it is not constant and strongly depends on the applied (H,σ) couple. The maximum peak moves at higher H field for higher σ and this confirms nonlinear modeling results.11 The maximum values are achieved at relatively low σ and H, within the ranges σ∈(–10,0) MPa and H∈(10,20) kA/m. Those ranges are useful to optimize the device and to choose the best magnetic bias and mechanical prestress. This analysis shows that any KEH device based on magnetostrictives must have a magnetic bias; for example, a suitable permanent magnet in the magnetic circuit and a tool to apply a static prestress21 in order to reach the best working point for the piezomagnetic parameter.

Figure 5.The piezo-magnetic coefficient of a Terfenol-d rod.17
Optimizing the Harvesting Cycle
The energy density of a KEH device can be calculated based on the area enclosed by the B-H cycle within the B-H plane (Figure 6). This area represents an energy gain for a clockwise cycle and an energy loss for a counterclockwise cycle. A KEH device can effectively be optimized by properly selecting parameters such as magnetic bias and prestress in order to maximize the area enclosed by the B-H cycle.
It is interesting to examine the behavior of clockwise-rotating cycles in the B-H plane with respect to the magnetic cycles of the material obtained at constant stress. The plot of Figure 6A shows the counterclockwise magnetic characteristics of a Galfenol rod at constant stresses of 1.58 and 48.2 MPa. The lines within the cycles represent the clockwise rotating loops due to harvesting tests when a simple resistor of 1 MΩ is employed as electric load. The cyclic stress variation is between σ = 1.58 and σ = 48.2 Mpa (the time period is 1.25 s) and three different magnetic field biases (8.7 kA/m–orange, 14.8 kA/m–brown, and 23 kA/m–red) are shown. It is noted the B-H loops obtained at different bias fields are within the range of the magnetic characteristics, as it was theoretically foreseen.22 Moreover, this is still true in Figure 6B where different resistors, at H = 14.8 kA/m, are employed. The loops are wider for smaller resistors because a larger current circulates in the pick-up coil and a larger magnetic field variation is then introduced. This result shows efforts to improve material harvesting behavior should concentrate on the static magnetic characteristics at different stresses as much as possible in order to improve the available area among limit cycles.

Figure 6. A)Magnetic characteristics of a Galfenol rod at 1.58 Mpa (black line) and 48.2 MPa (gray line) constant stresses; harvesting cycles lines, T = 1.25 s, H = 8.7 kA/m–orange, H = 14.8 kA/m–brown and H = 23 kA/m–red, R = 1 MΩ. B) Harvesting cycle lines: T = 1.25 s, R = 4.1 Ω–orange, R = 20 Ω–brown and R = 1 MΩ–red).
Conclusions
Kinetic energy harvesters based on magnetostrictives are simple devices in which the performance is mainly influenced by characteristics such as the piezo-magnetic coefficient and the magnetic B-H cycle behavior at constant applied stresses. New improved material can improve the performance in energy harvesting applications. The macroscopic analysis of the device suggests the research should focus on maximizing the piezo-magnetic coefficients: create more space for harvesting cycles within static limit cycles in the magnetic plane.
Acknowledgment
The work presented here has been supported by Italian research project PON “Low Noise” grant PON01_1878.
References
To continue reading please sign in or create an account.
Don't Have An Account?