Recent Advances in Scalable Synthesis and Processing of Two-Dimensional Materials
Deep Jariwala, 1, Jian Zhu2, Jung-Woo Seo3, Mark C. Hersam3
1Department of Electrical and Systems Engineering, University of Pennsylvania, Philadelphia, Pennsylvania, 19104, USA, 2School of Materials Science and Engineering, Nankai University, Tianjin, 300350, China, 3Department of Materials Science and Engineering, Northwestern University, Evanston, Illinois, 60208, USA
Material Matters, 2018, 13.1
Introduction
The isolation of two-dimensional (2D) crystals from layered van der Waals bonded materials has brought about transformational progress in materials research for electronic, photonic, and energy device applications.1–5 These applications require large area and high volumes of active component materials to enable manufacturing and operation at practical scales. In particular, traditional energy generation, transport, and storage devices require large quantities of 2D materials, whether it is the conductive electrode layer material such as graphene or semiconducting absorber or catalyst layer materials such as transition metal dichalcogenides (TMDCs). While most early device demonstrations have used mechanically exfoliated samples, several advances have since been made on roomtemperature solution-phase processing6–8 and high-temperature chemical vapor deposition9–13 for the synthesis and processing of 2D materials. While much of the early effort in this regard was applied to graphene, more recent large-scale synthesis and processing developments have focused on a wider set of 2D materials in addition to achieving precise control over their structure and properties. In this article, we provide a brief review detailing the most recent advances in synthesis and processing of 2D materials using solution phase and chemical vapor deposition methods, with particular emphasis on semiconductor materials beyond graphene.
Room-Temperature Solution-Phase Methods
Scalable production of 2D materials can be achieved by solution-based exfoliation methods.7,14–17 The relatively weak van der Waals interactions between layers in 2D crystals allow the peeling-off of nanomaterials consisting of monolayers or several layers through a consistent external energy input. One of the typical methods is ultrasonication in appropriate liquids, including organic solvents or surfactantbased aqueous solutions. Exfoliated nanosheets, typically a few hundred nanometers in size, are stabilized in solution through the adsorption of molecules on the surfaces to avoid re-aggregation. A variety of 2D semiconducting nanomaterials, such as MoS2, MoSe2, WS2, and SnS2, have been produced in this way with proper choice of solvents (Figure 1A).18 This liquid exfoliation method can achieve defect-free nanocrystals, as evidenced by TEM images (Figures 1B and 1C).19 In order to increase the exfoliation efficiency, ionic species or small molecules have been intercalated between layers to allow subsequent exfoliation into monolayer nanosheets.20,21 However, this interaction can lead to irreversible phase changes, resulting in exfoliated materials with different electronic properties. In particular, 2H-MoS2 intercalated with lithium ions coverts into the metallic 1T-MoS2 phase.22 Extensive thermal annealing cannot completely restore this metallic phase back to the pristine semiconducting structure, limiting its use as a semiconducting component in electronics. In addition to sonication, it is possible to achieve further largerscale production of 2D materials through shear exfoliation (Figures 1D and 1E).23,24 The high-shear mixing of 2D crystals in suitable stabilizing liquids enables exfoliation of 2D materials in large volumes. Such scalable methods facilitate commercial production of 2D material dispersions.25–29 Using a similar strategy, chemically reactive 2D materials, such as black phosphorous (BP, Cat. No. 808970), have been exfoliated in anhydrous organic solvents in inert environments to avoid oxidation (Figure 1F and 1G).30 The production of BP nanomaterials can also be achieved in deoxygenated water with the assistance of suitable surfactants.31

Figure 1.Solution-based processing of 2D semiconductors. A) Stable dispersions of various 2D materials obtained from liquid exfoliation.18 B) TEM image showing an exfoliated MoS2 nanosheet.19 C) High-resolution TEM image of exfoliated MoS2.19 D) Setup of large-scale shear exfoliation of 2D materials.24 E) Shear-exfoliated dispersions of 2D materials.23 F) Setup of a sealed container to minimize exposure to ambient air during tip ultrasonication.30 G) High-resolution TEM image of an exfoliated black phosphorous nanosheet.30 H) TEM image showing synthesized MoS2 nanosheets. The inset shows the amount of MoS2 produced by large-scale synthesis.35 I) Comparison of XPS peaks of synthesized and exfoliated MoS2 nanosheets.35 Reprinted with permission: A, E, F, G copyright 2015 American Chemical Society; B, C copyright 2011 American Association for the Advancement of Science; D copyright 2015 MacMillan Publishers Ltd.; H, I copyright 2016 Wiley VCH.
In addition to the top-down exfoliation of 2D materials, it is possible to construct these nanomaterials using bottomup solution-based synthesis.15,32 This colloidal growth of 2D nanocrystals may enable their scalable production for various applications. However, the anisotropy of 2D materials requires special control, such as ligands or defect engineering, during the growth process to induce 2D shapes.32,33 Various 2D semiconductor materials, such as MoS2, MoSe2, Bi2Se3, and InSe, have been produced synthetically.15,34 For example, bilayer MoS2 nanosheets have been produced at the gram-scale using the thermal injection method from the precursors of MoCl5, CS2, and tetradecylphosphonic acid (Cat. No. 736414) dissolved in oleylamine.35 The resulting MoS2 nanosheets have similar structural and chemical properties to samples generated via exfoliation (Figure 1H and 1I), allowing the development of wafer-scale applications such as flexible nonvolatile memory devices.35
Since most exfoliation methods lack perfect control over nanosheet size, significant research efforts have been devoted to the development of separation and purification methods.8,36,37 In particular, the thickness-dependent electronic and optical properties of TMDCs and BP provide significant motivation for subsequent purification following exfoliation. Two essential attributes for purification methods are: (1) scalability in order to produce sufficient quantities for applications; (2) ability to maintain the pristine electronic properties of the original 2D semiconductor materials. Towards these ends, sequential centrifugation has emerged as a general method for separating 2D semiconductor materials by their area and thickness (Figure 2A).30,31,38 In contrast to techniques involving ultracentrifugation,7 sequential centrifugation offers greater scalability with processing volumes that range from few tens of milliliters to tens of liters. In addition, the use of centrifugation with low g-force requirement allows for compatibility with organic solvents, which is advantageous for tuning the rheology while maximizing the solid content of purified dispersions. These attributes enable application of enriched 2D materials, namely TMDCs and BP, with multiple film fabrication methods such as vacuum filtration, drop casting, and printing.

Figure 2.Scalable solution-phase purification of 2D semiconductor materials by sequential centrifugation. A) Schematic view of a general preparation method for dispersions of 2D materials with distinct distributions of area and thickness using sequential centrifugation steps.38 B) TEM and AFM images of representative WS2 flakes that have been enriched towards achieving large size (1.5-2 kilo rotations per minute) versus low thickness (6-7.5 kilo rotations per minute).38 C) Schematic view of a sequential centrifugation process for air-sensitive BP flakes.31 D) AFM image of as-prepared few-layer phosphorene (FL-P).31 E) Photoluminescence from the FL-P dispersion that shows the characteristic behavior of pristine BP flakes.31 F) SEM image of a FL-P FET. G) Transfer curve from a FL-P FET.31 Reprinted with permission: A-B copyright 2016 American Chemical Society; C-G copyright 2016 National Academy of Sciences, U.S.A.
Essentially, the purification process includes multiple centrifugation steps with varying sedimentation force applied to the suspended flakes. Once a dispersion is centrifuged minimally to sediment the large, unexfoliated aggregates, the supernatant is subjected to increasing centrifugal conditions and collected at different intervals. This step-wise approach enables the isolation of populations with different distribution of area and thickness, as demonstrated in Figure 2B. For instance, large and thick flakes are well-suited for applications where a percolating composite structure is needed, whereas a sample with the greatest distribution of thin flakes with reasonable lateral size enables transistor devices. Most recently, sequential centrifugation has been utilized to prepare purified dispersions of BP flakes (Figure 2C).30,31 Due to the high sensitivity of BP towards chemical degradation in air, exfoliation and centrifugation are performed with minimal ambient exposure. With these precautions, sequential centrifugation allows the preparation of few-layer phosphorene (FL-P) with average thickness of 4.5 nm (Figure 2D).30 Most importantly, the pristine optical and electronic properties of BP are preserved through the preparation process, as demonstrated in Figure 2E–G.30 Thickness-dependent photoluminescence of BP was observed from the enriched dispersions, and field-effect transistors fabricated with FL-P showed comparable ION/IOFF value to the devices based on micromechanically exfoliated BP flakes, thus showing that this approach produces electronic-grade 2D semiconductor materials.
High-Temperature Chemical Vapor Deposition
While solution-phase synthesis and processing have scalability advantages, these methods do not produce materials that can be assembled into continuous monolayer thin films.7 Instead, thin films assembled from solution-processed material have a percolating network of flakes with van der Waals electronic contacts that limit charge transport. For high-performance optical and electronic devices, superior crystalline quality is often required. In contrast to solution-phase approaches, hightemperature synthesis and deposition allows the growth of large crystals with high electronic quality in the resulting films. The elevated temperature of the growth permits thermal diffusion and kinetics necessary for crystallization with minimal defects. Chemical vapor deposition (CVD) is one such technique that has been widely used for synthesizing a range of 2D materials.9,10,13,39 CVD relies on the introduction of precursor vapors in the hotzone of a reactor where the deposition substrate is placed. The precursors undergo pyrolysis followed by chemical reaction in the gas phase and/or on the substrate to form the resulting film. Over the past decade, numerous results have been published on CVD synthesis of 2D materials ranging from graphene and boron nitride to TMDCs. Most of them have been summarized in comprehensive review articles.9,10,13,40 Here, we focus on the latest developments in the synthesis, manipulation, and control over growth of 2D materials. Special emphasis is given to growth parameters such as substrate, nucleation, and precursor engineering in addition to doping and heterostructure synthesis.
CVD is often classified based on the type of substrates and precursors that are used as well as the growth pressure. For synthesis of 2D materials such as graphene and boron nitride, catalytically active substrates have been the most widely and commonly used strategy. Foils or thin films of transition metals such as copper or nickel have been the most popular catalytic growth substrates for graphene13 and h-BN.40 For TMDCs, CVD does not necessarily require catalytic activity. Early reports of MoS2 growth used sulfurization of Mo thin films.41 Subsequently, high-quality growth was reported by pyrolysis of metal-organic compounds containing both Mo and S such as ammonium thiomolybdate42 (Cat. No. 323446) or by sublimation of powder precursors such as MoO3 and elemental S.43 Numerous reports detailing the growth and characterization of TMDC materials using the above methods have been summarized in recent reviews.9,10 A majority of the reported syntheses used amorphous SiO2 substrates. Due to the weak interaction of the growing 2D layer with the substrate, the individual islands tend to be randomly oriented.43,44 However, the use of a single-crystal substrate such as epitaxial graphene on SiC45 or (0001) sapphire46 (Cat. No. 634875) leads to quasi van der Waals epitaxy of the TMDC lattice and helps align the individual islands along the same crystallographic orientation (Figure 3A). The aligned islands then merge together to form a macroscopic, continuous monolayer sheet that is single crystalline.46

Figure 3.Substrate and nucleation engineering for growth control. A) Sapphire substrates control van der Waals epitaxy in a manner that results in crystallographic alignment of all MoS2 islands, allowing the formation of a single-crystal monolayer.46 B) Catalytically active substrates such as Au foils allow growth at lower temperatures, and different crystal orientations of the Au support provide different nucleation and growth rates.49 C,D) Soda lime glass (C) has been used to trap/dissolve small amounts of MoO3 precursor in the glass substrate which when passed over by S results in the growth of monolayer MoS2 crystals.50 Likewise, molten silica glass (D) presents an atomically smooth surface enhancing diffusion for the growth of millimeterscale single crystals of MoS2 and MoSe2.51 E) Powder precursor growth often results in a TMDC fullerene nucleus encapsulating an oxide crystal that gets consumed and results in lateral 2D growth upon further sulfurization.52 F) Metal organic chemical vapor deposition (MOCVD) helps overcome the shortcoming of conventional CVD using powder precursors, but also requires nucleation assistance by alkali metals such as K and Na.54 G) MOCVD has also been demonstrated in a cold-walled vertical reactor using induction heaters to grow WSe2.55 H) Careful design of the metal organic precursor can allow incorporation of the metal source and seeding layer in the same molecule to promote uniform nucleation and growth.56 Reprinted with permission: A-F copyright 2015, 2016, 2017 American Chemical Society; G copyright 2016 Institute of Physics Publishing; H copyright 2016 The Royal Society of Chemistry.
Likewise, substrates can also influence the growth in terms of nucleation density and rate of growth. For example, Au foils are catalytically active for sulfurization reactions and hence are used to grow large-area, single crystals of TMDCs and polycrystalline films.47 The advantage of using catalytic metal substrates is the growth is limited strictly to a monolayer since the catalytic activity is diminished upon completion of monolayer growth.48 Furthermore, the crystallographic orientations of the underlying Au foil affect the nucleation and rate of growth. Specifically, the (100) and (110) facets are more favorable for large grain growth (Figure 3B) due to differences in binding energy of the precursors to the facets.49 In addition to catalytic activity, dissolution of precursors in the substrate can help restrict the thickness of grown films towards the monolayer limit. At high temperatures, molten soda-lime glass dissolves a small amount of MoO3. The dissolved MoO3 can then be sulfurized at lower temperatures to grow MoS2 and WS2 monolayers (Figure 3C).50 Substrate smoothness and precursor solubility also play critical roles in nucleation since molten glass/SiO2 provides a much smoother surface for growth, leading to large single crystals of MoSe2 with record field-effect mobilities at room temperature (Figure 3D).51
Precise control over nucleation is thus key to the synthesis of high-quality monolayers with minimal line defects such as grain boundaries. This challenge has led to several studies to investigate the fundamental structure and nature of nucleation for TMDC growth. High-resolution electron microscopy has recently revealed that the initial nucleation event resembles a MoO3 nanoparticle encapsulated by a MoS2 fullerene (Figure 3E).52 Upon sulfurization, 2D atomic layer growth occurs depending on the interaction of this fullerene-encapsulated nanoparticle with the underlying substrate. This lends credibility to prior observations of the influence of moisture in the creation of MoO3 seeds that ultimately promote nucleation of MoS2. While sublimation of powder precursors provides a viable solution for laboratory-scale experiments, the use of solid powder sources leads to inhomogeneous nucleation and thus uncontrolled thickness of the resulting TMDC. Therefore, recent efforts have focused on metal-organic gas-phase precursors for uniform large-area growth. In particular, metal-organic chemical vapor deposition (MOCVD) allows the growth of monolayer TMDCs over large areas with high quality.53 Molybdenum and tungsten hexacarbonyls are the preferred metal sources while dimethyl and diethyl sulfides and selenides as well as hydrogen sulfide and selenide have been used as the chalcogen precursors.53–55 However, nucleation of the crystals from the gas phase onto the solid substrate remains a challenge. While highly aromatic perylene-based molecules with a graphite-like core have served as nucleation centers in powder precursor CVD, the MOCVD precursors have also worked well with alkali metal salts.54 The early presumption was that alkali metal salts serve as moisture desiccants. More recently, though, it was discovered that they serve as nucleating agents if the substrate is exposed to alkali metal halides such as KI or NaCl and then to the metal precursor before preforming the actual growth (Figure 3F).54 Control over nucleation has also been achieved in a cold-walled MOCVD setup (Figure 3G) where an extra temperature step is added between 550-700 °C below the growth temperature of 900 °C to form small clusters (15-40 nm) of the precursor material that act as the nucleation sites.55 Furthermore, with the wide variety of metal-organic compounds available, more complex precursors such as molybdenum dimethyldithiocarbamate (Mo DMDTC) have been used that act as both the source of metal atoms and organic nucleation promoters (Figure 3H).56
The previous paragraphs discussed recent developments in CVD and MOCVD synthesis of high-quality, pure, stoichiometric TMDC compounds as atomically thin layers. Modern semiconductor technology, however, heavily depends on the ability to manipulate the properties of semiconductor materials and integrate them with other semiconductors, metals, or insulators into heterostructures. In this regard, several attempts have been made to directly synthesize doped or alloyed semiconducting 2D materials and heterostructures. Since previous review articles have commented on doping and heterostructure growth of 2D semiconductors,57–59 here we focus primarily on the most recent developments in substitutional doping and heterostructure growth of 2D semiconductors.
Doping is critical for most semiconductor applications. The ability to tune electron and hole concentrations lies at the heart of semiconductor electronic and optoelectronic devices. A majority of 2D TMDCs naturally occur as n-type doped.1,60 In contrast p-type 2D semiconductor materials are relatively rare, aside from ambient-exposed black phosphorus.61,62 Therefore, substitutional doping of TMDC lattices is critical to achieve complementary semiconductor technology from purely 2D TMDCs. Recently, such substitutional doping was systematically achieved in WS2 and MoS2 through the use of solid-state dopant precursors during growth. For example, the addition of niobium chloride enabled small amounts of Nb to replace W in the WS2 lattice (Figure 4A). The dopant precursor was supplied along with the chalcogen (S) to ensure uniform delivery and doping. Since Nb has one less valence electron (5) than W (6), it is expected to be a p-type dopant for WS2. Likewise, rhenium (7 valence electrons) instead of 6 for Mo serves as an n-type dopant for MoS2.63 The doping in TMDCs can be extended further into heavy alloying of atomic components both on the metal as well as the chalcogen side. While ternary alloys have been synthesized and characterized in great detail,64,65 only recently quaternary alloys of the Mo-W-S-Se system have been synthesized. High-resolution electron micrographs indicate that Mo dominates the metal sites in the MX2 configuration, while a hybrid Se-S configuration dominates the chalcogen (X) sites followed by Se2 and a minority of S2 sites (Figure 4B).66 All four elements were found to be in random solid-solution typedistribution with no obvious nanoscopic domain formation.66 While solid-solution alloys are useful for obtaining materials with precise and tunable band gaps, an ordered structure often results in intrinsically novel properties. In an MX2 TMDC layer, such an ordered structure can be visualized by having all top chalcogen atoms being S and all bottom chalcogen atoms being Se to obtain a Janus monolayer semiconductor.67,68 Such Janus TMDCs have recently been achieved through a growth method where the top layer of S or Se is etched away by hydrogen plasma to leave a meta-stable hydrogen terminated H-Mo-S or H-Mo-Se monolayer. Subsequently, the introduction of Se or S vapors leads to the formation of ordered Se-Mo-S or vice versa (Figure 4C). The high out-of-plane structural asymmetry results in large second-order susceptibility ratios and an out-of-plane piezoelectric response.68
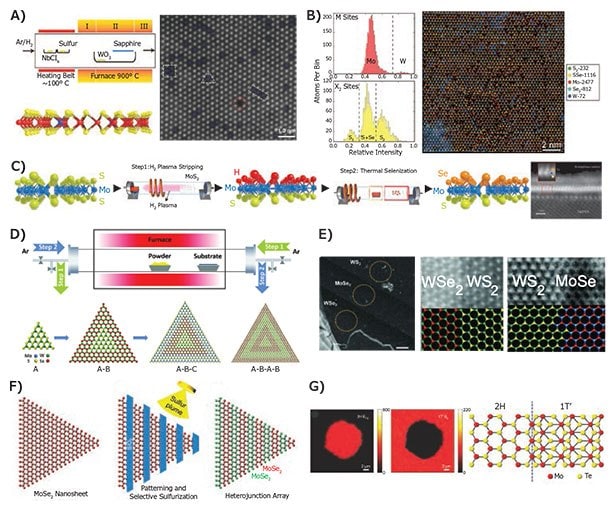
Figure 4.Controlled doping and growth of heterostructures. A) Schematic setup for doping a WS2 monolayer with Nb atoms (left). Atomic-resolution micrograph showing the Nb dopants in blue in addition to other defects such as vacancies (right).63 B) Quaternary solid solution of Mo, W, S, and Se atomic layer with the respective distributions of metal and chalcogen atom sites (left). Atomic-resolution micrograph with color coded atoms (right).66 C) Schematic synthesis procedure for a Janus TMDC monolayer that consists of Se-Mo-S layered sequentially within a single three-atom thick layer.68 D) Schematic dual-direction carrier gas flow setup for sequentially growing in-plane TMDC multi-heterojunctions and superlattices. E) Ball and stick atomic structures of multi-heterojunctions and high-resolution electron micrographs of junction interfaces.73 F) Schematic of top-down superlattice synthesis using lithographically patterned sulfurization of MoSe2.74 G) Raman maps showing in-plane heterojunctions of the 2H semiconducting and 1T metallic phase of MoTe2 with corresponding ball and stick schematic.76 Reprinted with permission: A, B, G copyright 2016, 2017 Wiley VCH; C, F copyright 2015 MacMillan Publishers Ltd.; D, E copyright 2017 American Association for the Advancement of Science.
Ordered structures can also be grown in-plane resulting in lateral heterojunctions from two lattice matched 2D materials stitched together in the same plane. Numerous reports of such in-plane epitaxial heterojunctions exist already.69,70 However, little is known about the growth control parameters that lead to in-plane epitaxial growth of heterojunctions. Some observations suggest the cleanliness of the initial seed-island71 or the presence of alkali metal salt (e.g., NaCl) are important in the lateral nucleation and growth of the next layer from the edge of the seed.72 Yet, there remains a need for a systematic synthetic pathway to highly scaled heterojunctions, multi-heterojunctions, and superlattices. Recent work has made progress towards these goals via several different methods. For example, reversing the gas flow during growth provides unique synthetic control (Figure 4D), resulting in epitaxial, defect-free, multi-heterojunction and superlattice interfaces (Figure 4E).73 Another method utilizes top-down lithography for masking and conditions where S replaces Se to create superlattices and heterojunctions of desired dimensions (Figure 4F).74 A related strategy etches out the desired pattern using a focused ion beam and then regrows another material in the etched pattern.75 Finally, controlled heterostructures between structural and electronic phases (2H semiconducting and 1T metallic) have been achieved in MoTe2 by controlling the vapor pressure and flux of tellurium (Figure 4G).76
Applications, Summary, and Outlook
In summary, recent developments in solution-phase and hightemperature growth and processing of 2D materials have resulted in significant progress towards achieving precise control over the quality, interface, polydispersity, structure, and doping in 2D semiconductors. These improvements are having direct impact on practical applications, even at the technology levels. In particular, the expansion of large-scale solutionphase synthesis of 2D materials has enabled thermoelectric,77 photovoltaic,78,79 electrochemical,80,81 and photocatalytic82 applications. For the case of thermoelectrics, 2D TMDCs have much higher thermoelectric power factors77 compared to the bulk, and composites of TMDCs and graphene show high Seebeck coefficients.83
For optoelectronics, the absorption cross sections of TMDCs are among the highest reported for semiconductor materials. This superlative optical absorption combined with their self-passivated and atomically thin nature makes them attractive candidates for photovoltaic acceptors in heterojunction solar cells.84 Likewise, the high catalytic activity of defect sites allows them to play dual roles of absorbers and catalysts for photocatalytic82 and photoelectrochemical reactions. The availability of high-quality monolayer to multilayer thin films with controlled doping and heterostructuring has further presented new opportunities in solid-state devices. Specifically, 2D semiconductors with direct band gaps in the visible portion of the electromagnetic spectrum are facilitating unprecedented performance enhancements in optoelectronic devices such as photovoltaics78,79 and lightemitting diodes (LEDs).85,86 For thin-film inorganic photovoltaics, atomic-scale thickness enables superior charge collection upon photoexcitation. This attribute combined with light trapping techniques results in photovoltaics with few-nanometer thick absorber layers that are ideal for mobile and space-based solar power. The absence of dangling bonds also minimizes nonradiative recombination in 2D semiconductors, leading to the observation of near-unity photoluminescence quantum yields, with clear implications for high-efficiency light-emitting diodes.85 Furthermore, given the covalent and inorganic nature of 2D materials, they possess higher thermal and ambient stability compared to organic emitters.
This review is largely centered on applications of 2D materials in mainstream devices and technologies. Moving forward, one of the key challenges will be to identify device structures and applications where the use of 2D semiconductors has a unique advantage over incumbent materials or technologies. Many of the most promising directions are attempting to exploit the defect-free van der Waals interfaces beyond purely layered 2D materials in mixed-dimensional heterostructure architectures,87 where properties can be actively tuned under the application of electric fields and strain. Further improvements in 2D material quality and optimization of buried van der Waals interfaces will help accelerate progress in this regard.
References
Para seguir leyendo, inicie sesión o cree una cuenta.
¿No tiene una cuenta?