Antibody Drug Conjugate Manufacturing
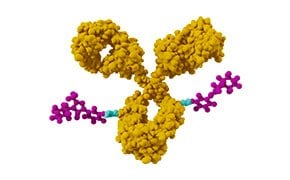
Antibody-drug conjugates (ADCs) are therapeutics that use monoclonal antibodies (mAbs) to deliver highly potent active pharmaceutical ingredient (HPAPI) to target cells. ADCs comprise a monoclonal antibody (mAb) conjugated to a payload, via a stable linker. The linker ensures that the payload remains attached to the antibody until it reaches the target site, thus minimizing off-target toxicity. Although most approved ADCs, and those in development, target various cancer indications, these complex therapeutics hold significant promise for treating a variety of other diseases.
Contact us if you need more information on raw materials or equipment for your in-house ADC development or production, or if you are interested in outsourcing to a CDMO.
Featured Categories
Our complete range of Mobius® single-use mixing solutions can meet your needs for mixing pharmaceutical ingredients from intermediate to final drug products…
Ultrafiltration & diafiltration are important steps throughout bioprocessing to increase capacity, concentration, and recovery.
Ion exchange (IEX) chromatography separates biomolecules based on difference in charge...
Biologics are therapeutics that can be based on proteins, peptides, viruses, viral vectors, or nucleic acids. They require a defined environment to remain intact and functional throughout the manufacturing and formulation process, as well as during long-term storage.
Challenges of ADC development and manufacturing
The development and manufacturing of ADCs is more complex than that of mAbs, requiring significant technical expertise and robust containment measures to maintain operator safety. Typically, expertise in HPAPI and large molecule development, linker chemistry, and conjugation is needed, combined with analytical capabilities to characterize and demonstrate purity, homogeneity, and stability of the ADC product. In addition, manufacturing suites usually contain specialized equipment designed to mitigate the risk of operator exposure to the highly cytotoxic payloads.
Successful development and consistent production of the desired ADC molecule depends on several factors including:
- Conjugation: Must not affect mAb functionality; can be non-site-specific or site-specific, dependent on the method of conjugation.
- Linker Design: Affects the ADC stability following administration to the patient, efficiency of payload release at the target site, pharmacokinetics, efficacy, and toxicity.
- Drug-to-Antibody Ratio (DAR): The desired average number of HPAPI or drug molecules conjugated to the mAb must be achieved. A low DAR can reduce effectiveness of the ADC while a high DAR can negatively impact the mAb structure, stability, target binding, and overall safety profile.
- Efficient Purification: Optimized to reliably remove process related contaminants, residual linkers and cytotoxic HPAPI payload.
- Consistent Purification: To maintain the desired therapeutic effect, for any given DAR there should be low variability in the ADC composition.
- Reliable Containment: Is critical throughout the manufacturing workflow to maintain operator safety. Single-use systems provide a flexible, safe, and reliable solution for successful ADC manufacturing.
- Stable and Safe Formulation: Parenteral administration requires the selection of high-quality excipients. ADC stability, solubilization, and administrability are required for optimal therapeutic efficacy.
Throughout the ADC manufacturing process, it is critical to select products and technologies that ensure high operator safety, reduce contamination risk, and support seamless scalability from development to GMP production. Single-use systems provide a safe, reproducible, and scalable solution, supporting high yields that meet target quality attributes. Comprehensive documentation on extractables and leachables from the supplier, facilitates risk assessment, and accelerates your path to successful and safe ADC manufacturing.
Visit our document search for data sheets, certificates and technical documentation.
Related Articles
- ADCs are a fast-growing drug modality used as a cancer therapy. Learn more about the parts of an ADC, how bioconjugates work, and the ADC manufacturing process.
- Meta description: ADC payload intermediates such as, DOLCore ™, MAYCore ™, and PBDCore ™, simplify payload synthesis for the most commonly used payloads: maytansine, dolastatin, and PBD dimers.
- See the data on how the chito-oligosaccharide ChetoSensar™ overcomes ADC solubility challenges.
- Find best practices for using Pellicon® Capsules in ADC processing as well as data from two studies using Pellicon® Capsules and Pellicon® cassettes in the ADC manufacturing process.
- See All (44)
Find More Articles and Protocols
How Can We Help
In case of any questions, please submit a customer support request
or talk to our customer service team:
Email custserv@sial.com
or call +1 (800) 244-1173
Additional Support
- Chromatogram Search
Use the Chromatogram Search to identify unknown compounds in your sample.
- Calculators & Apps
Web Toolbox - science research tools and resources for analytical chemistry, life science, chemical synthesis and materials science.
- Customer Support Request
Customer support including help with orders, products, accounts, and website technical issues.
- FAQ
Explore our Frequently Asked Questions for answers to commonly asked questions about our products and services.
Workflow


Conjugation
The HPAPI payload or payload-linker complex reagents are usually prepared separately. Successful conjugation optimizes reagent addition, ensures proper mixing with monitoring and control of the conjugation reaction.
Learn more about ADC manufacturing: Conjugation

Purification
Chromatography and/or tangential flow filtration (TFF) is used to purify the ADC. The goal is to remove unwanted species, such as molecules with an undesirable DAR, aggregates, residual unconjugated linker-payload, and reaction solvents. Conjugated payloads can promote aggregation of the ADC, especially if very hydrophobic, presenting an additional challenge for purification.

Further Purification and Final Formulation by TFF
Additional purification may be necessary to reduce contaminants and exchange the ADC to formulation buffer. Maintaining ADC solubility is crucial, especially given the typically high hydrophobicity. The use of high-quality chemicals such as buffers, pH adjusters, surfactants, stabilizers, and viscosity-reducing excipients supports efficient purification and a stable final formulat

Sterile Filtration
The formulated bulk ADC is sterile filtered prior to filling or shipment for filling offsite. Proper containment is critical to maintain sterility of the ADC bulk and assure operator safety from the highly toxic HPAPI payload.

Fill Finish
The bulk ADC drug product is sterile filtered prior to filling. Well-designed final filtration and filling assemblies can minimize product loss, maximize ADC yield while enabling filter integrity testing and maintaining sterility and the containment needed for operator safety.
To continue reading please sign in or create an account.
Don't Have An Account?