Lithography Nanopatterning Tutorial
Introduction
Lithography, based on traditional ink-printing techniques, is a process for patterning various layers, such as conductors, semiconductors, or dielectrics, on a surface. Nanopatterning expands traditional lithographic techniques into the submicron scale.
We will meet your materials needs for lithography and nanopatterning with our complete line of monomers, polymers, resins, inks, surfactants, silanes and related products. We offer resist materials, photoacid generators (PAGs), polyelectrolytes for self-assembled monolayers (SAMS), fluorine-containing monomers for 157 nm UV resists, and our high-purity norbornadiene. Research and bulk quantities of all materials are available.
Section Overview
Lithography
Nanoimprint Lithography
Soft Lithography
Photochemical Acid Generators
Nanopatterning
Nanopatterning via Phase Separation of Polymers
Self-Assembled Monolayer Systems (SAMS)
Norbornadiene
Lithography
A typical integrated circuit consists of various patterned thin films of metals, dielectrics and semiconductors on various substrates such as silicon, gallium arsenide, or germanium. Such a device is fabricated by a technology known as lithography, in which radiation sensitive polymeric materials called resists are used to produce circuit patterns in the substrates. Figure 1 depicts the lithographic process sequence.

Figure 1:Schematic representation of the lithographic process.1
The resist material is applied as a thin coating, typically by spin coating over the substrate (wafer) and then heated to remove the casting solvent (post-apply bake, pre-exposure bake, or pre-bake). The resist film is subsequently exposed in an image-wise fashion through a mask (in photo- and X-ray lithography) or directly with finely focused electron beams. The exposed resist film is then developed typically by immersion in a developer solvent to generate three-dimensional relief images. The exposure may render the resist film more soluble in the developer, thereby producing a positive-tone image of the mask. Conversely, it may become less soluble upon exposure, resulting in generation of a negative-tone image. When the resist image is transferred into the substrate by etching and related processes, the resist film that remains after the development functions as a protective mask. The resist film must "resist" the etchant and protect the underlying substrate while the bared areas are being etched. The remaining resist film is finally stripped, leaving an image of the desired circuit in the substrate. The process is repeated many times to fabricate complex semiconductor devices.1
For a resist material to be useful in device fabrication:
- it must be capable of spin casting from solution into a thin and uniform film that adheres to various substrates such as metals, semiconductors, and insulators
- possess high radiation sensitivity
- possess high resolution capability, dictated by solubility/insolubility characteristics
- withstand extremely harsh environments, for example, high temperature, strong corrosive acids, and plasmas such as used in subsequent etching, doping and sputtering operations.
In earlier generations of resists (often based on novolok phenolformaldehyde polymers), each absorbed quantum of radiation induced on average less than one chemical reaction within the material. "Photosolubilizable compositions" for photographic and photoresist applications with overall quantum yields greater than one were described by Smith as early as 1973.2 The idea was limited in practice, however, until thermostable yet photosensitive onium salts of strong acids were developed by Crivello as PAGs for cationic photopolymerization.3 The first CA resist for microlithography was reported by the university industry team of Frรฉchet (University of Ottawa) and Willson and Ito (IBM Inc.),4 who combined onium salts with the acid-deprotectable poly(4-[t-butyloxycarbonyloxy]styrene) (poly-TBOCST), and coined the term chemical amplification. Over 200 articles and several reviews have appeared on this topic between January 1992 and June 1994 alone.5-10
In chemical amplification (CA) resists, the primary photochemical event produces a mobile catalyst that, typically during later postexposure baking (PEB), goes on to induce a cascade of material transforming secondary catalytic events within a 5-25 nm radius. Such chemical amplification thus makes possible an overall quantum yield (the number of material reactions divided by number of absorbed photons) of up to several hundred. Thus, a CA resist must contain:
i. a small amount (ca. 1-5 wt%) of radiation-sensitive catalyst precursor, generally a photoacid generator (PAG);
ii. many chemical groups that can react by elimination, addition, or rearrangement only in the presence of catalyst;
iii. polymer matrix able to disperse all other components in a smooth clear film; and
iv. optional additives to improve performance or processability; e.g., surfactants, photosensitizers, and etch resistors.
Although in most reported compositions the catalyst-sensitive groups are polymer-bound and the catalyst precursors are free (i.e., i + ii~iii), components i-iii or iv can in principle be interconnected in any combination, as small molecules, homopolymers, copolymers or blends (e.g., i + ii + iii, i~ii + iii, i~ii~iii).1-4 Along with their higher sensitivity and contrast in forming images, CA are also better than earlier resists in being more flexible in design and formulation, versatile in radiation source (electromagnetic or particle beams), and compatible with dry (plasma), multilayer, and other advanced pattern transfer techniques. In general, resist systems can be classified on the basis of their design, namely, one-, two-, or multi-component systems. One-component resist systems consist of pure polymers that must combine all the necessary attributes such as substrate protection, radiation sensitivity, and film-forming characteristics. The most popular resist designs in modern lithography are based on two-component systems in which resist functions are provided by two separate components.
Resist systems can also be divided into three groups on the basis of the radiation source: UV or photoresists, electron-beam resists, and X-ray resists. Photolithography that utilizes UV light has been the predominant technology in semiconductor manufacture and will continue to be so in the foreseeable future. X-ray lithography is capable of producing high-resolution, high-aspect-ratio (height-width) images and is considered to be the technology of the future, whereas electron-beam lithography is used in photomask fabrication. Photolithography can be further subdivided into near-UV (350-450 nm), mid-UV (300-350 nm), and deep-UV (< 300 nm) technologies, depending on the wavelength of the exposure. The resolution is proportional to the exposing wavelength and inversely proportional to the numerical aperture (NA) of the lens. Thus the i-line (365 nm) with a high-NA lens shifting from the g-line (436 nm), has been regarded as the dominant technology in the manufacture of 16-megabit (Mbit) dynamic random access memory (DRAM) devices with a minimum feature size of 0.5 mm. Krypton fluoride (KrF, 248 nm), argon fluoride (ArF, 193 nm), and F2 (157nm) excimer laser technologies are emerging as the minimum feature size continues to shrink far below 0.5 mm down to 80 nm.11
The breakthrough that ultimately led to the adoption of 248 nm lithography as the technology of choice for advanced device fabrication was the development of CA resists. The consensus candidate for the next generation of optical lithography tools has been photolithograpy using 193 nm light. At this wavelength, the opacity of traditional aromatic-based materials precludes their use. Alternate resist materials based on aliphatic polymers and dissolution inhibitors have been examined.10 The introduction of monomers bearing cyclic side groups such as adamantyl or norbornyl significantly improves the etch resistance over that of simple acrylic polymers. Alternately alicyclic structures have been incorporated directly into the polymer backbone offering a second route to 193 nm single layer resists.12
The next generation of optical lithography at 157 nm has necessitated new developments in resist technology. Due to their high optical absorbance at 157 nm, single-layer 248 nm and 193 nm photoresists are not a viable alternative. The incorporation of fluorine into polymers have led the way to suitable resist materials.13
Nanoimprint Lithography
Imprinting, or embossing, is a well-known technique to generate microstructures in hard polymers by pressing a rigid master containing surface-relief features into a thin thermoplastic polymer film that is then heated close to or, more generally, above the Tg (Figure 2).14 Nanoimprint lithography (NIL) has the potential of high-throughput due to the parallel processing, does not require sophisticated tools, and allows nanoscale replication for data storage.15,16 NIL is also compatible with conventional device processing techniques. The quality of the nanoimprinting process depends on a number of experimental parameters like T, viscosity in the melt, adhesion of the polymer to the mold, etc.17 PMMA has been most widely used as the imprintable material, but a range of thermoplastic and thermosetting polymers is under investigation to optimize the imprinting and subsequent etching steps.18,19

Figure 2.Schematic overview of nanoimprint lithography.
The rigid master is usually prepared via e-beam lithography and has feature sizes in the 10โ100 nm size range. After imprinting the polymer film, further etching can transfer the pattern into the underlying substrate. Alternatively, metal evaporation and lift-off of the polymer mask produces nano scaled patterned metal features.
Soft Lithography
Nanoimprint lithography (NIL) has primarily been used to emboss hard thermoplastic polymers. The micromolding and embossing of elastomers has attracted considerable interest as these materials have found important applications in softlitho graphic techniques such as microcontact printing (mCP).20,21 In this technique, a monolayer of a material is printed off an elastomeric stamp [made of poly(dimethylsiloxane) (PDMS)] after forming conformal contact between stamp and substrate (Figure 3). Sub-micron surface relief structures can easily be introduced in PDMS by curing the polymers against a lithographically prepared master. The advantage of mCP is the ability to pattern surfaces chemically at the sub-micron level.
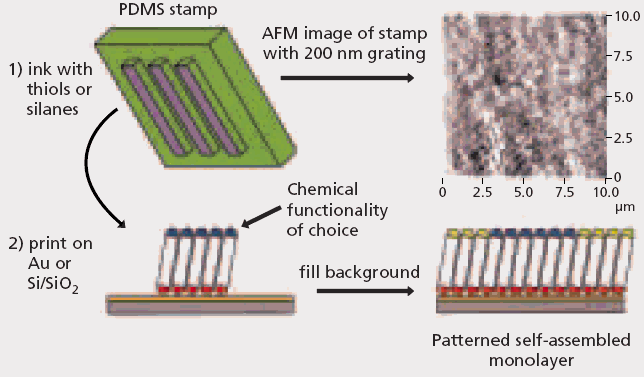
Figure 3.Schematic overview of microcontact printing (mCP). (Images courtesy of Hongwei Li, Wilhelm T. S. Huck; University of Cambridge , Department of Chemistry , Melville Laboratory for Polymer Synthesis.)
An elastomeric stamp is inked with small molecules (thiols or silanes) and pressed against a clean substrate (gold or silicon wafer). Where the stamp is in contact with the surface, a monolayer of material is transferred to the substrate. A second thiol or silane is used to fill in the background to provide a chemically patterned surface.
Photochemical Acid Generators
Photoacid generators (or PAGs) are cationic photoinitiators. A photoinitiator is a compound especially added to a formulation to convert absorbed light energy, UV or visible light, into chemical energy in the form of initiating species, viz., free radicals or cations. Cationic photoinitiators are used extensively in optical lithography. The ability of some types of cationic photoinitiators to serve as latent photochemical sources of very strong protonic or Lewis acids is the basis for their use in photoimaging applications. The continuing decrease in device dimensions in the microelectronics industry is being achieved by pushing the limits of optical lithography. In chemically amplified resist technology, the radiation-sensitive material (resist) in which patterns are delineated typically includes a matrix polymer and an onium salt photoacid generator (or PAG).10 There are several materialsโ issues to be considered in the choice of the PAG: sufficient radiation sensitivity to ensure adequate acid generation for good resist sensitivity, absence of metallic elements, temperature stability, etc.22
The usual photo-supplied catalyst has been strong acid. Triarylsulfonium and diaryliodonium salts have become the standard PAG ingredients in CA resist formulations, because of their generally easy synthesis, thermal stability, high quantum yield for acid (and also radical) generation, and the strength and nonvolatility of the acids they supply.23 Simple onium salts are directly sensitive to DUV, X-ray and electron radiations, and can be structurally tailored, or mixed with photosensitizers, to also perform well at mid-UV and longer wavelengths. However, onium salts are ionic and many will phaseseparate from some apolar polymers, or not dissolve completely in some casting solvents. Nonionic PAGs such as phloroglucinyl and o,o-dinitrobenzyl sulfonates, benzylsulfones and some 1,1,1-trihalides are more compatible with hydrophobic media in general, although their thermal stabilities and quantum yields for acid generation are often lower.24
The phenomenal rate of increase in the integration density of silicon chips has been sustained in large part by advances in optical lithography โ the process, as described above, that patterns and guides the fabrication of the component semiconductor devices and circuitry. Although the introduction of shorter-wavelength light sources and resolution enhancement techniques should help maintain the current rate of device miniaturization for several more years, a point will be reached where optical lithography can no longer attain the required feature sizes.25 Several alternative lithographic techniques under development have the capability to overcome these resolution limits โ EUV, X-ray, electron beam and ion beam lithographies, but, at present, no obvious successor to optical lithography has emerged.
Nanopatterning
Techniques for fabricating on sub-micron length scales span a wide range, from sophisticated lithographic methods that have their origins in the semiconductor industry to more recent materials and chemical advances that rely on self-organization. For delineating patterns below 100 nm, several approaches have been proposed (and indeed demonstrated). These include nano-imprint lithography (including micro-contact printing, mold-assisted lithography, and hot embossing lithography), near-field optical lithography, direct patterning on a nanometer scale with scanning-probe microscopes, self-assembly of monolayers, pattern formation based on phase separation of polymers, etc. The search is on for nonphotolithographic methods that could provide technologically simpler and cheaper nanofabrication strategies. Some of these approaches are better suited for producing individual nano-structures for the investigation of nanometer-scale devices; the throughput is likely to always remain impracticably low for commercial application. Others such as nanoimprint lithography have the potential of high throughput due to parallel processing, do not require sophisticated tools, and allow nanoscale replication for data storage.15,16
The natural length scales of polymer chains and their morphologies in the bulk, which lie in the nanometer domain, make polymers ideal building blocks for nanopatterning. Recent developments in the use of polymers for the fabrication of nanostructures via lithographic and self-assembling strategies have been reviewed.26
Nanopatterning via Phase Separation of Polymers
Block copolymers of flexible, chemically incompatible, and dissimilar blocks can microphase separate into a variety of morphologies with nanometer scale dimensions. This self-assembly process is driven by an unfavorable mixing enthalpy and a small mixing entropy, while the covalent bond between the two blocks prevents macrophase separation. When the microphase separated morphology can be controlled and turned into a useful structure, phase separation of block copolymers can be a powerful tool for fabricating nanostructures without additional lithography and processing steps.27 In addition, to block copolymers copolymers, random copolymers comprising sufficiently dissimilar components based on size and chemical nature, for e.g., SSQ-MMA copolymer, SSQ/Polypropylene blend, or physical blends of hydrophobic and hydrophilic polymers driven by an underlying pattern of incompatibility have been shown to yield functional and arbitrary patterns.26,28 The use of surfactants in such blends may be used to accentuate the areas of different surface tension.
Soft lithographic approaches have been combined with surfactant and particulate templating procedures to create to create hierarchically ordered oxides.29 A recent report combines molecular scale, evaporation-induced self-assembly (EISA) of organically modified mesophases with macroscopic, evaporative printing procedures. This allows the rapid fabrication of hierarchical structures exhibiting form and function on multiple length scales and at multiple locations. The formulation of the "ink" in such hierarchial assembly strategies is complex and may use a variety of surfactants.30
Self-Assembled Monolayer Systems (SAMS)
Polyelectrolytes are defined as materials for which the solution properties in solvents of high dielectric constant are governed by electrostatic interactions over distances larger than typical molecular dimensions.1,31 These materials are widely used in industrial applications as dispersants in aqueous media, flocculating agents to coagulate slurries and industrial wastes, for sizing in textile and paper manufacture, and as conditioning additives to drilling muds and soil to prevent abrasive damage. More recently, they have been applied in molecular self-assembly techniques for thin film deposition of electrically conducting polymers,32 conjugated polymers for light emitting devices,33 nanoparticles,34 and noncentrosymmetric-ordered second order nonlinear optical (NLO) devices.35
The technique of Self-Assembled Monolayers or SAMs is an ingeniously simple, yet powerful nanoscale approach for the fabrication of functional supramolecular assemblies for various device applications.36-40 It involves the alternate adsorption of anionic and cationic polyelectrolytes onto a suitable substrate. Typically, only one of these is the active layer, while the other enables the composite multilayered film to be bound by electrostatic attraction. Alternatively, the oppositely charged polyelectrolytes may serve as a barrier for the sustained release of an active core. Controlled formation of highly ordered, three-dimensional, multifunctional, reactive, thin films containing biological molecules is seeing widespread application in the areas of biotechnology and biomaterials science.41,42
Of the potential polyanionic candidates, poly(styrenesulfonic acid) (PSSA) and its salts have been used extensively.40 Why? Excellent adsorption properties, water solubility, smooth films with easily controllable thickness, controlled level of loading/penetration of active componentโall properties essential in realizing high performance devices based on supramolecular structures in terms of selectivity, sensitivity, response time, and stability. In addition, PSSA has been used to dope thiophene-based conjugated polymers to make them conducting, e.g., PEDOT/PSS (Product No. 483095 and 560596). Post treatment of polyaniline (emeraldine salt), grafted to lignin (see Product No. 561096; 561118; 561126; 561134), with PSSA may also be used to enhance electrical conductivity.
Norbornadiene
A scan of the scientific and patent literature reveals that this versatile monomer has been applied over a vast spectrum of high technology applications, in fields ranging from materials science, ag-related, and pharmaceutical, to being used as a model system in fundamental research activity (for example, in testing new nanocatalysts - in single-step hydrogenations,43,44 tandem cycloaddition reactions,45 Pauson-Khand annelation46,47 as well as in comprehensive theoretical studies.48,49 The unique set of properties offered by Norbornadiene along with its transformations driving some of the reported applications are highlighted in the following table.

Scheme 1.Conversion between norbornadiene (NBD) and quadricylane (QC).
References
๊ณ์ ์ฝ์ผ์๋ ค๋ฉด ๋ก๊ทธ์ธํ๊ฑฐ๋ ๊ณ์ ์ ์์ฑํ์ธ์.
๊ณ์ ์ด ์์ผ์ญ๋๊น?