3D printing allows drug manufacturing to create personalized tablets rather than make a few billion of the same pills. Meet one scientist who’s driving the field forward.
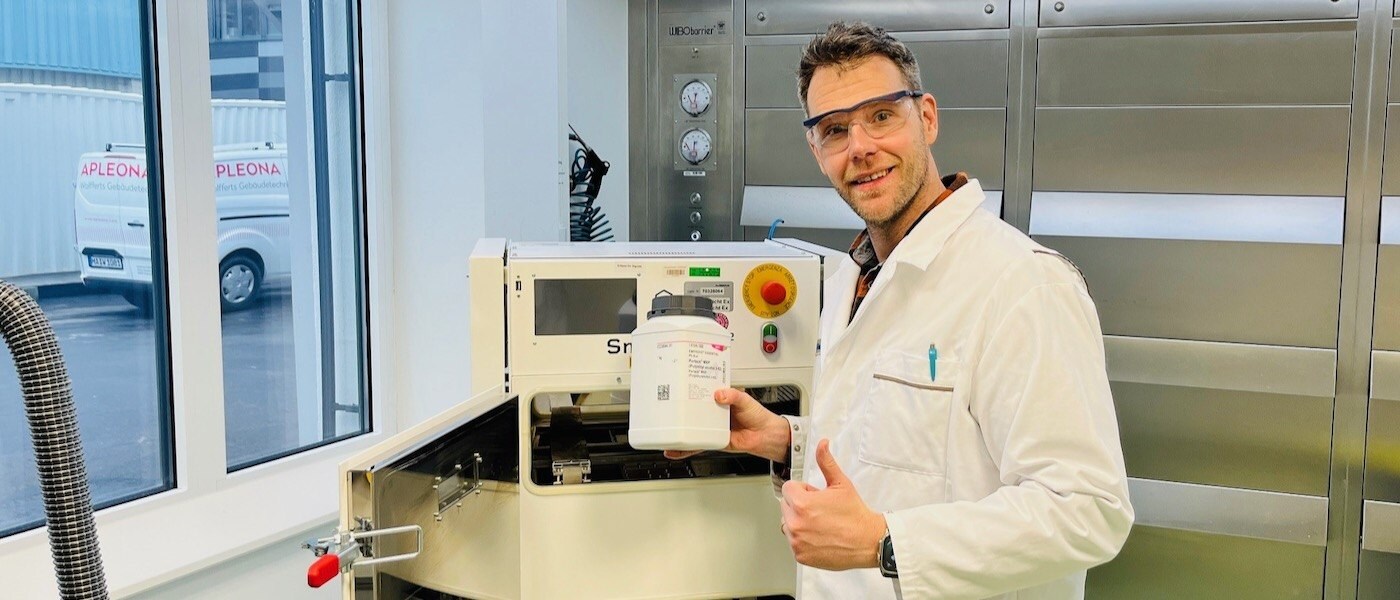
February 2, 2024 | 5 min
Most kids don’t know what their parents do at work. But Thomas Kipping doesn’t have a job like most parents. Kipping, at least some of the time, uses lasers to make pills.
For his eight-year-old son Léopol, the idea that lasers could be used outside of light sabers — as seen in his favorite movies — is mind-boggling. Even for most adults, the idea that lasers could produce drugs seems far off in the future. But it’s closer than you might think.
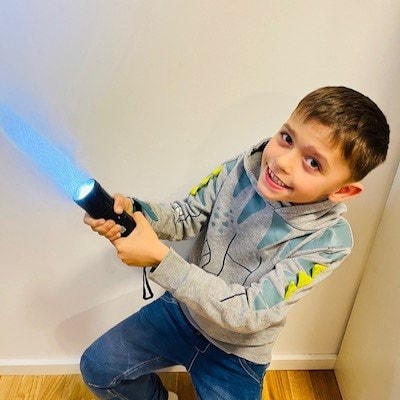
Léopol sports his own "laser” at home.
Lasers are just one of several techniques used in 3D printing — also known as additive manufacturing — that researchers are using to produce drugs at smaller scales. Kipping, alongside colleagues, looks to optimize existing techniques and hone new ones.
Figuring out how to effectively manufacture smaller batches of drugs is a major logistical hurdle to move the field of precision medicine forward. Precision medicine involves generating individualized treatment plans for patients based on their specific needs. For this to work, drugs will need to be tailored on a patient-by-patient basis and manufactured at smaller scales.
Out With the Old, Sometimes
Traditional drug manufacturing is aptly known as “batch processing” and can take weeks or even months, frequently resulting in billions of pills. It takes significant infrastructure, investment and a sizeable footprint. Essentially, large machinery compresses powdered raw ingredients into a solid layer, a tablet.
This is great for certain drugs, like ibuprofen, that have steady consumer demand and a dosage window that’s relatively forgiving. Adults take one or two pills — not 1.15 pills. Dialing specific dosage requirements is difficult and time-consuming in this traditional manufacturing setup.
It’s also a challenge to produce small quantities of a drug using traditional methods. Producing a couple hundred tablets for clinical trials or a few dozen for a specific patient is costly and inefficient. These are two key reasons why biopharmaceutical manufacturers are looking for a different way to produce drugs. Enter 3D printing.
3D printing, which first debuted in 1987, is already used extensively across numerous industries — from the food sector to plastics, 3D printed objects are all around us. While the first drug approved by the Food and Drug Administration was 3D printed in 2015, no drugs have followed, at least not yet. The technology leveraged in 2015 was initially designed for a very specific application so it has taken time to broaden the technology to other drugs.
Kipping and his colleagues work on a handful of different 3D printing concepts. They foresee more approvals on the horizon.
Pharmacy of the (Near) Future
One 3D printing approach — known as melt extrusion — has a few drugs now in clinical trials. By using high heat, active ingredients are mixed with other additives that help with delivery and absorption. Getting the right medley of “inactive” ingredients — known as excipients — is crucial. Without them, active ingredients won’t get absorbed and end up in the toilet, literally.
Optimizing excipients is an important aspect of Kipping’s work. Because the manufacturing style is different than traditional methods, customers need a unique combination of excipients and manufacturing know-how, which Kipping and his team help create.
The hot melt extrusion process, for example, is much easier to transport outside of industrial settings compared to other methods, including those that involve lasers. To enable personalized drug delivery in pharmacies, Kipping's team is closely working with a team from the University of Bari. They are evaluating direct extrusion printing technology which makes the technology more accessible in local pharmacies or hospital pharmacies.
Because of this, Kipping and others are optimistic that drug manufacturing will soon start happening outside of large manufacturing settings. Drug manufacturing close to the patient is another advancement that would make personalized medicine a bit more feasible.

Thomas Kipping (L) and Florian Hess (R) use a dissolution tester to see how a tablet might perform in the body when the drug is released.
Laser-Focused
Laser-based 3D printing — much to the delight of Kipping’s son — is another approach. Through close collaborations between research groups at the University of Uppsala and the University of Utrecht, the team is working to better understand the intricacies of using lasers to 3D print pills.
Essentially, a thin powder layer — including active ingredients and a variety of polymers — forms a powder bed. Then a laser uniformly melts the powders together. A new layer of powder enters, and the laser returns to melt again. This process repeats until a 3D form takes shape. While it sounds painstakingly slow, it runs at the speed of light.
“Lasers move super-fast through the print bed,” says Kipping.
Laser-based printing creates pills that are quite porous — or that have tiny holes throughout the pill. The fact that water can permeate through nooks and crannies means the pills will dissolve quickly after a patient swallows it. Because of this, laser-based printing is appealing for drugs that need to be released immediately once they’re swallowed.
“We see a lot of potential for laser-based printing, and that’s why we’re working at it from the early stages,” shares Kipping. Researchers are working hard to bring laser-based printing into the toolkits of drug manufacturers.
For Kipping and others working in the space, they’re right on the edge of what’s possible and plausible. The implications for personalized medicine and the future of healthcare are not interesting yet to his son. He’s still most excited about the lasers.
About Our Offerings
Poor solubility remains a major challenge in pharmaceutical formulation development. While there is no one-size-fits solution for small molecules, our teams work to hone techniques — including 3D printing —and develop new formulations to enhance solubility. Our Application Services help customers with a wide variety of challenges, including simplifying formulation design with the innovative Parteck® excipient portfolio.
To continue reading please sign in or create an account.
Don't Have An Account?