La solution est dans la (nouvelle) poche
Il a fallu des années d'ajustements, de tests et de réajustements minutieux pour développer des films plus durables et, en bout de chaîne, des poches à usage unique plus résistantes.
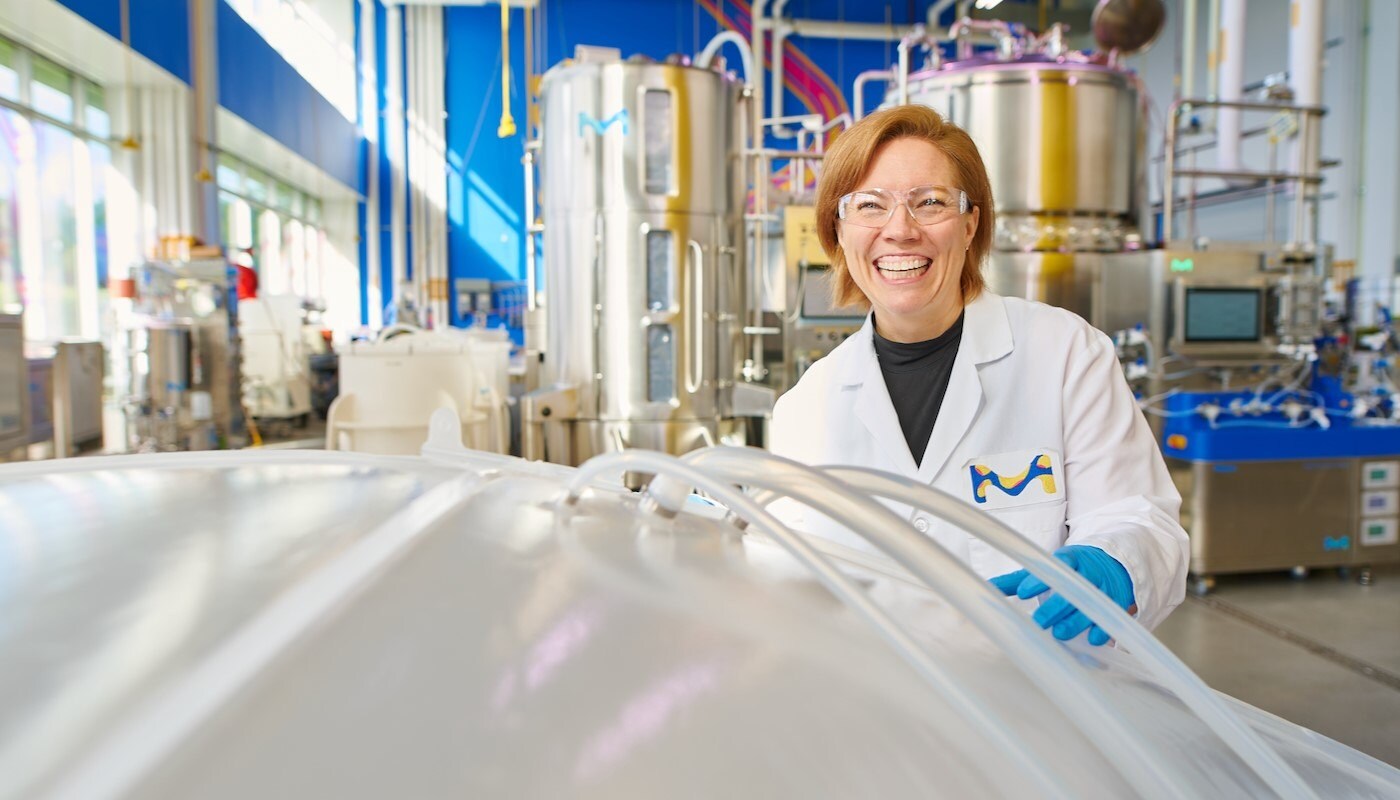
Shannon Cleveland se tient au M Lab™. Elle tient une poche à usage unique fabriquée en film Ultimus.
18 septembre 2023 | Temps de lecture : 6 min
L'œil ne voit pas tout.
Dans les matériaux multicouches, chacune répond à des objectifs différents. Certaines assurent l'intégrité structurelle. D'autres permettent au matériau de résister aux contraintes thermiques ou de rester souple. On peut en dire autant de nos pneus de voiture, des combinaisons d'astronautes ou de la nouvelle poche à usage unique destinée aux fabricants de produits biopharmaceutiques.
Ces dernières années, les ingénieurs de Merck, dont Shannon Cleveland et David DeCoste, ont travaillé à concevoir de nouvelles poches à usage unique utilisées comme doublures (liners) dans l'équipement de fabrication de médicaments. Le développement des poches à usage unique n'a pas été une mince affaire, car l'équipe devait identifier les matériaux à utiliser et, surtout, s'assurer que ces couches étaient dûment assemblées.
"Le film possède treize couches, chacune ayant une fonction spécifique", explique D. DeCoste, directeur Recherche et développement (R&D) de l'équipe. "Certaines couches constituent l'environnement idéal pour la culture des cellules, tandis que d'autres assurent la résistance et la souplesse. La mise sur le marché du produit a nécessité une vaste équipe de développement dont les membres proviennent de nombreux services."
Commencer en pensant à la fin
Dans bien des sites de bioprocessing, les poches à usage unique sont utilisées comme doublures dans les bioréacteurs, des machines souvent comparables aux grandes cuves de fermentation présentes dans les brasseries. Les bioréacteurs contiennent des cellules et d'autres composants utilisés pour fabriquer des médicaments qui sauvent des vies. Les poches à usage unique accélèrent la fabrication, car, entre autres avantages, elles réduisent le temps de nettoyage entre les lots. Les sites peuvent ainsi produire davantage de médicaments en moins de temps.
Une fuite au niveau d'une poche à usage unique contenant un mélange pharmaceutique constitue une erreur extrêmement frustrante et coûteuse. Puisque les poches contiennent de grandes quantités de liquides, subissent de fortes fluctuations de températures et sont transportées d'un point à l'autre de l'usine, elles présentent un risque permanent d'abrasion et de perforation.
Quand les journées de travail sont longues, S. Cleveland, comme d'autres, se réconforte en pensant que son travail est utile à la santé des patients. "C'est très gratifiant de savoir que j'aide à développer des produits qui font la différence", explique-t-elle.
Uniquement les candidats les plus sérieux
Ces dernières années, l'équipe R&D du site Merck de Bedford (Massachusetts, États-Unis), où travaillent S. Cleveland et ses collègues, a minutieusement développé et comparé différentes combinaisons de matériaux pour créer un nouveau film destiné aux poches à usage unique. Assez vite, ils se sont rendu compte que l'ajout de nylon tissé augmenterait l'élasticité et la résistance.
Les films contenant du nylon étaient très performants, mais les différentes couches avaient tendance à se détacher. La chasse aux polymères supplémentaires a donc commencé. L'équipe cherchait à développer une couche de liaison capable d'assurer la solidarité des éléments structurels. Elle a commencé à tester attentivement de multiples combinaisons.
Les ingénieurs ont soumis le film à d'énormes contraintes en laboratoire, avec de nombreuses torsions et compressions, 2 700 pour être précis.
Après le passage d'un échantillon de film dans ce que S. Cleveland qualifie à juste titre d'essoreuse, elle a quantifié l'effet des torsions sur le matériau. Lors d'un autre test, S. Cleveland et ses collègues ont calculé le temps nécessaire à une pointe métallique pour percer le film.
Ces tests, et une série d'autres, ont amené les chercheurs à une conclusion plutôt frustrante : tous les derniers candidats potentiels offraient les mêmes performances. Les essais n'ont permis d'identifier aucune différence parmi les polymères destinés à la couche de liaison. Pourtant, S. Cleveland pouvait observer visuellement des disparités entre les matériaux soumis à contraintes. Elle savait que l'histoire n'était pas terminée.
"J'avais besoin de nouvelles données pour caractériser les différences entre les films. Je devais trouver un nouveau test", explique-t-elle.
Du flou à la clarté
Après une étude attentive de la littérature scientifique, S. Cleveland a décidé de tenter une autre approche. Certes, il était essentiel de trouver la bonne combinaison de polymères et le moyen de solidariser efficacement les couches de film, mais c'est la découverte d'une méthode permettant d'évaluer les différentes compositions qui s'est avérée décisive.
Au lieu de percer les films avec un objet pointu, S. Cleveland a décidé d'étirer chacun d'eux au moyen d'une pointe émoussée. Les matériaux distendus avaient un aspect un peu trouble, alors S. Cleveland a cherché à quantifier le phénomène. Plus le film était étiré, plus il avait l'air trouble et fin.
Jamais personne dans son laboratoire n'avait travaillé de la sorte. Il était donc difficile d'accéder à l'équipement adéquat. Heureusement, lors d'un emploi précédent, S. Cleveland avait travaillé dans le laboratoire R&D de filtration à quelques portes de là. C'est un lieu où la turbidité est un sujet de réflexion et d'essais à part entière. Les scientifiques y testent des liquides et non des films, mais S. Cleveland a voulu tenter l'expérience.
Elle avait déjà quantifié la turbidité de l'eau, alors pourquoi pas celle du plastique ?
L'esprit imprégné d'une importante littérature scientifique et les mains armées de ciseaux et d'étiquettes, elle se mit au travail. Elle coupa de petits morceaux de plastique, les plaça dans des cuvettes et mit en route le néphélomètre. Après quelques cycles, elle se savait sur une piste intéressante. Elle avait trouvé un moyen de quantifier les films les moins troubles, et donc les plus résistants. Grâce à ce nouveau test, son équipe a pu affiner et améliorer l'aspect et les performances des films.
Les problèmes comme celui-là, voilà ce qui la motive. Ceux qui nécessitent une réflexion itérative loin du prêt à penser. "C'est un bonheur", explique-t-elle en réfléchissant au processus de pensée créative, bien qu'assez peu orthodoxe, qui a présidé à l'invention du film. "C'est gratifiant de pouvoir réfléchir à ma façon et de faire la différence."
À l'école, les scientifiques en herbe apprennent à formuler des hypothèses, à tester, retester et tester encore. Parfois, ils ont besoin de tester les tests. C'est exactement le genre de casse-tête qui stimule S. Cleveland et ses collègues. Depuis les premiers pas en laboratoire jusqu'au lancement final, en passant par la mise à l'échelle avec l'équipe de production, plus d'une centaine de personnes ont collaboré pour donner naissance au film Ultimus et à la nouvelle génération de poches à usage unique.
Mais Ultimus n'a pas marqué la fin du parcours. L'équipe recherche déjà de nouvelles solutions, notamment des poches qui s'emballent et s'expédient plus facilement. Tous ses efforts ramènent à un même objectif : aider les fabricants de solutions biopharmaceutiques à produire plus rapidement des médicaments vitaux. Des films et des poches encore plus performants sont à venir. Et probablement encore plus de tests.
En savoir plus sur Ultimus
Le film Ultimus® est l'un des composants des poches à usage unique Mobius® 3D pour les bioprocédés. Il en fait une solution plus robuste et plus durable pour relever tous les défis de production. En savoir plus sur le film Ultimus®, ses capacités supérieures de résistance et de sécurité dans les applications des bioprocédés, ses spécifications, etc.
Remerciements
Shannon Cleveland et David DeCoste remercient tous leurs collègues qui ont joué un rôle clé dans le développement du film, en particulier ceux du département R&D : Joe Cianciolo, Joe Muldoon, Brian Pereira, Diana Perez, Marissa Maher et Kate O'Brien.
Lire d'autres témoignages

Mike D'Acquisto II, verrier de matériel scientifique, dirige sa flamme vers le col d'un ballon à fond rond.
Les béchers et les flacons en verre sont moulés sur des lignes de production de masse, mais la verrerie scientifique à façon est fabriquée et réparée à la main par des verriers hautement qualifiés, spécialisés dans le matériel à usage scientifique, selon un procédé qui foisonne d'étincelles, d'éclats et de moments de tension.
Découvrez comment les verriers scientifiques domptent la chaleur.
Pour continuer à lire, veuillez vous connecter à votre compte ou en créer un.
Vous n'avez pas de compte ?