Continued Process Verification for Quality
Section Overview
- Overview of Continued Process Verification
- Parameter Classification and Statistical Treatment of Data
- Determining Control Limits
- Determining Cpk and Ppk
- Parameter Monitoring
- Trending Rules
- Documentation and Reporting
The Food and Drug Administration (FDA) guidance on continued process verification and the EU GMP Annex 15 requirements for ongoing process verification direct pharmaceutical and biopharmaceutical manufacturers to ensure that their processes remain in a continual state of control (a validated state) during the lifecycle of the product so that the strength, quality, and purity of the final drug product is maintained. Both regulatory agencies instruct manufacturers to develop sustained programs which collect and analyze product and process data to evaluate the state of control and to identify product or process problems as opportunities to implement improvements.
Process validation of a therapeutic product consists of 3 stages:
- Process design: initial design and development of the commercial process is defined based on development and scale-up activities
- Process qualification: process design is assessed to make sure that it can consistently produce the product
- Continued process verification (CPV): ongoing monitoring and analyzing of the manufacturing process to ensure it remains in a state of control
Process validation’s first two stages have a distinct endpoint while CPV is sustained throughout the commercial life of a drug molecule and requires a comprehensive strategy.
CPV necessitates continued and routine monitoring of the commercial manufacturing process to detect any variation from historical data or adverse trends, and to understand the sources of variation. If variation is detected, the biomanufacturer must determine the impact of the variation on the process and the product attributes and control the variation as needed to maintain product quality.
Overview of Continued Process Verification
The CPV process flow consists of procedures, tools, and processes summarized in the eleven steps outlined below. Specifically, CPV consists of collecting process parameter data, trending it against statistical control limits, and calculating process capability and process performance (Cpk and Ppk) at defined intervals or after every few batches. CPV programs typically include the following components:
- Parameter classification and statistical treatment of data
- Determination of Cpk and Ppk
- Parameter monitoring
- Out-of-trend detection rules
- Documentation and reporting
To learn more on CPV, read our eBook “Implementing Continued Process Verification”.
CPV Process
- Identify CPPs, KPPs and MPs
- Identify parameters that need to be trended periodically
- Set CPP, KPP, and MP validation ranges and specification limits
- Establish statistical control limits and frequency for updating control limits
- Establish trending rules
Automated by Bio4C ProcessPad™ Software:
- Publish in-process control and monitoring documents
- Monitor parameters against set limit
- Evaluate root cause of any rule violation and its impact on product & process. If needed, initiate corrective and preventative actions (CAPA).
- Publish quarterly process reports with recommendations for process improvements and control limit updates
- Update control limits
- Implement updated control limits and incorporate them in change control process
For more information on our software platforms and how they can help simplify CPV, visit our data analytics software web page.
Parameter Classification and Statistical Treatment of Data
The initial step in designing a robust CPV program is the classification of parameters and the statistical treatment of data.
Parameter classifications are defined by process characterization, process validation, or in-process control description documents. These documents also set initial action or specification limits. Performance or input parameter types include:
- Critical process parameters (CPPs): directly impact product identity, purity, quality, or safety and must be routinely monitored
- Key process parameters (KPPs): directly impact CPPs or are used to measure consistency of a process step and must be routinely monitored
- Monitored parameters (MPs): may or may not impact KPPs and are used to measure consistency of a process step or are routinely trended for troubleshooting; MPs are monitored on a case-by-case basis
Once the parameters are classified, limits for each are defined and applied. Specification limits and action limits are defined during process design and qualification stages. The first 15 to 30 batches (statistically significant) can be trended against these limits. Alert or statistical control limits are then defined based on these initial batches.
Statistical treatments are performed on the data to determine the respective statistical control limits for the performance parameters. Most process parameters will follow the distribution of a normal/Gaussian bell shaped curve while some will follow a skewed distribution.
Determining Control Limits
How the data are distributed determines the procedure for setting up in-process control limits for the continued process verification.
- If the data are not normally distributed, control limits are based on percentile methodology for upper control limit (UCL)/lower control limit (LCL) and centerline.
- If the data are normally distributed, control limits are based on standard deviation (SD) for UCL/LCL and average for centerline.
Statistical process control (SPC) is an important element of CPV and a process control chart (Figure 1.) plays the most important role in SPC and any process monitoring program. A successful CPV system should not only create SPC charts from validated data, but it should also store, display, and evaluate control chart statistics based on historical limit changes.
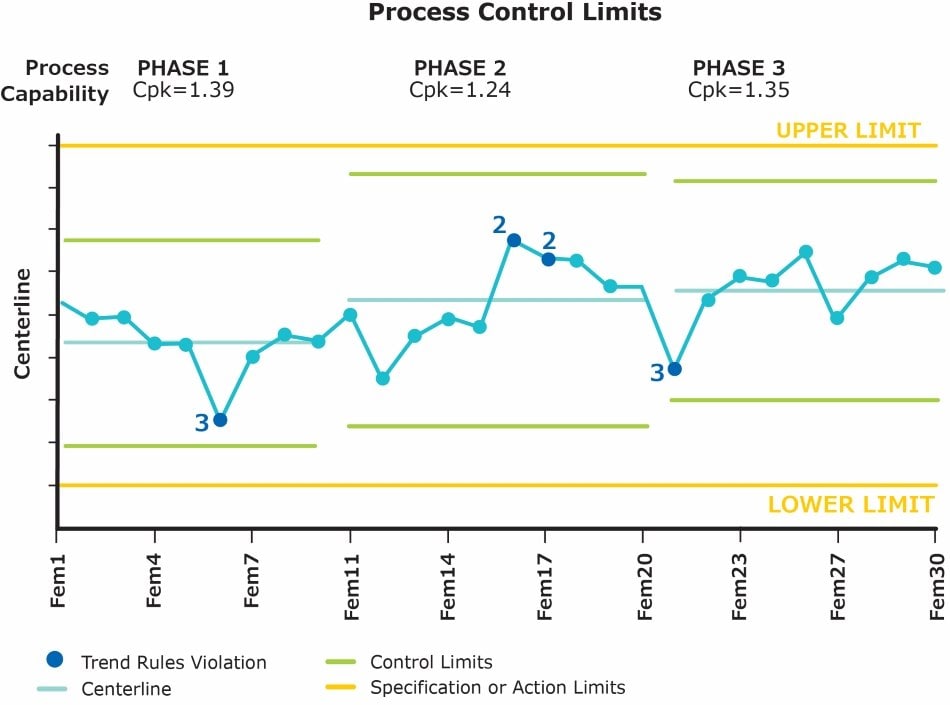
Figure 1. Example of a process control chart.
Determining Cpk and Ppk
A manufacturing process is a unique combination of its manufacturing environment comprised of machines, methods, and people engaged in the production process.
Process capability indices have been used in manufacturing to provide quantitative measures on process potential and performance. The output of a process can be a product characteristic or a process output parameter. Process capability indices (Ppk, Cpk) provide a common metric to evaluate and predict the performance of processes and summarize process performance relative to a set of specifications (i.e., quality boundary).
Process capability (Ppk, Cpk) for a normally distributed monitoring process parameter is calculated using the following equation:
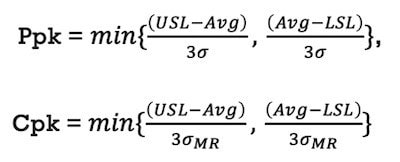
Figure 2.Ppk and Cpk equations.
Where:
USL = Upper Specification Limit (for CPP) or Upper Action Limit (for KPP)
LSL = Lower Specification Limit (for CPP) or Upper Action Limit (for KPP)
Avg = Average or mean of the population under analysis
σ = Standard deviation of the population under analysis
σMR = Moving Range Standard Deviation
Cpk cannot be estimated for non-normal data as the average and standard deviations will not represent the non-normally distributed data correctly. Instead, Ppk is evaluated based on all of the data points in terms of percentile ranges. The following equation is used to estimate Ppk for a non-normally distributed monitoring process parameter.

Figure 3. Ppk equation for non-normally distributed monitoring process parameter.
Where:
USL = Upper Specification Limit (for CPP) or Upper Action Limit (for KPP)
LSL = Lower Specification Limit (for CPP) or Upper Action Limit (for KPP)
X0.50 = Median of the population under analysis
X0.99865 = 99.865th Percentile of the population under analysis
X0.00135 = 0.135th Percentile of the population under analysis
Parameter Monitoring
During process monitoring, a performance parameter will be subject to different monitoring modes depending upon the number of data points and accumulated history of the parameter.
Monitoring phases including:
- Preliminary process monitoring (PPM): data are collected to obtain sufficient historical information to make reasonable assumptions on inherent variability of the parameter and estimate a statistical control limit with reasonable confidence
- Statistical process control (SPC): once the basic history of a parameter is accumulated, control limits are established
- Resetting or revising control limits: control limits should be periodically re-evaluated, revised, or reset when enough batch history is generated or if changes are introduced to the process
Trending Rules
Nelson or Western Electric rules should be established and used for out-of-trend detection and to determine if any process parameters are out of control. A batch violating any of the trending rules should be properly investigated and closed with appropriate corrective and preventative actions (CAPA).
Documentation and Reporting
Several types of reports are generated in support of CPV including:
- In-process control and monitoring (IPCM) – an IPCM document should be prepared for each commercial process for each manufacturing location. The document includes performance process parameters (CPP, KPP and MP) and process limits (specification, action, and control limits) for all monitored parameters along with suggestions on statistical treatment of each parameter based on distribution of data.
- Process trends – all monitored parameters should be routinely trended on a weekly basis for each commercial process with respect to each processing location.
- Process summary reports – these reports should be published quarterly for each commercial process and manufacturing location.
- Site trend violation and CAPA reports – trend violations and CAPA reports should be prepared at periodic intervals for all products and processes for all manufacturing locations. The reports should highlight the differences or similarities of violations across products, processes, and locations.
Data Management and Software Tools Simplify and Automate Continued Process Verification
Successfully executing CPV requires end-to-end data management throughout the process validation life cycle and can be extremely challenging if the appropriate tools and software are not used to facilitate data integration, analysis, and sharing across the manufacturing network.
Manually tracking critical batch data in spreadsheets and transferring it between systems is time-consuming, error prone, and can lead to data integrity issues. In addition, siloed data prevents teams from efficiently identifying causes of a deviation or an adverse trend, as well as tracking important trends that could lead to process improvement.
An integrated data software environment automates and simplifies CPV including:
- Data management: collect and store data from sources throughout the product lifecycle such as manual records, quality control data, LIMS, QMS, or MES systems, data historians and streaming data
- Data aggregation from disparate sources into a single, contextual, analysis-ready format
- Automation of:
- data distribution predictions
- Cpk and PpK calculations
- statistical trend rule violation calculations
- control limit management
- CPV reporting
- Data visualizations to help identify trends and outliers to better understand process performance
Para seguir leyendo, inicie sesión o cree una cuenta.
¿No tiene una cuenta?