Organic Photovoltaics in IoT, Architecture, and Wearables
Graham Morse1, Richard Harding1, Agnieszka Pron1, Nicolas Blouin2, Hannah Buerckstrummer2, Stephan Wieder,2, David Mueller2, Stephane Berny3
1Merck Chemicals Ltd, Chilworth Technical Centre, University Parkway, Southampton. SO16 7QD, U.K., 2Merck KGaA, Frankfurter Str. 250, 64293 Darmstadt I Germany, 3Merck Selbstmedikation GmbH, Frankfurter Str. 250, 64293 Darmstadt, Germany
Material Matters, 2017, 12.3
The development of high performance carbon-based semiconductors has enabled organic photovoltaics (OPVs) to become an important source of alternative energy over the past few years. The newly developed active materials used in OPV are non-toxic and enable cost effective and eco-friendly rollto- roll manufacturing with orders of magnitude lower energy consumption compared to the manufacturing process for classic photovoltaics. As a result, OPV systems have significantly faster payback times versus other solar technologies.1–3 OPV modules are thin and flexible laminates that can easily be added to a variety of substrates and building materials, including standard lamination onto glass. Furthermore, OPV systems do not exhibit a drop in performance caused by typical outdoor conditions such as diffuse light and high temperatures. The versatility to adapt and tune active materials enables the creation of modular designs that meet specific requirements including a choice of colors, shapes, and degrees of transparency. This allows OPV to meet many more functional and aesthetic demands required by product designers and architects.4 OPV technology was recently used to fabricate a >250 m2 flexible power system reaching an average performance of ~5% power conversion efficiency (PCE) in a semi-transparent configuration, as illustrated in Figure 1.4
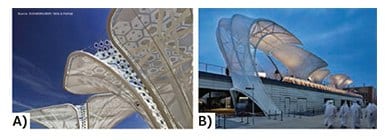
Figure 1.OPV Solar Trees at EXPO 2015 in Milan. A) Series of OPV solar modules fabricated by solution-deposition techniques (blue hexagons on the picture) are connected to form a network of >250 m>sup>2 charging batteries during daylight. B) OPV-powered lights coming from the trunk of the Solar Trees create aesthetic shades during the night.
The Internet of Things (IoT) is rapidly developing and connecting everyday physical objects to the internet in order to identify and communicate with other devices. The IoT has attracted tremendous interest because of its potential positive impact on quality of life and the enormous pool of new business opportunities that it is expected to enable. Early benefits of IoT can be found in engineering, logistics, transportation, and operation processes.5 A recent analysis by McKinsey summarized the potential business impact of IoT and concluded that the market for these technologies is expected to increase as much as 11 trillion USD by 2025.6 One key technical prerequisite for the growth of IoT is the ability for developers to create innovative hardware infrastructure using cost-effective, lowenergy, and maintenance-free power sources for use in offices, human wellness, and retail. Photovoltaic (PV) technologies are seen as particularly interesting energy-harvesting systems for IoT because of its potential for low-power output and portability in miniaturized and grid-independent applications.
For these reasons, interest in OPV as an energy source for architectural elements, IoT, and wearable devices is increasing. In this review, we outline some recent progress in OPV materials and device design, and detail examples of where OPV technology can act as an energy source, potentially enabling larger deployment of low-power, low-maintenance, and environmentally friendly hardware solutions.
OPV Solar Cell Design
Solution processed organic photovoltaic systems were first tested by Heeger and Sariciftci.7 The bulk heterojunction (BHJ) concept was later developed8 to minimize the mean path length that excitons must diffuse while maximizing light absorption within the device. The accessibility of modern synthetic techniques and tools for molecular engineering of aromatic systems has allowed for a great material diversity in BHJ solar cells. BHJ solar cell efficiencies in the lab have increased from ~3%8 to better than 12%9 over the past 20 years. As a result, OPV is now generating significant commercial interest and promises to have an impact on a number of new applications, both large and small.
BHJ Concept
BHJ solar cells are fabricated by the coating or printing of subsequent layers to form a multilayered stack in which each layer plays a specific role in charge generation, separation, or extraction. Since each layer is printed from inks of soluble components, it is essential that each layer be designed to avoid dissolution of the underlying layers — a property known as orthogonality. Two main device configurations exist for BHJ solar cells, commonly referred to as standard and inverted architectures (Figure 2). These architectures are constructed starting with a transparent conductor, usually indium tin oxide (ITO) or ITO-metal-ITO (IMI) patterned on top of a transparent substrate such as glass or plastic (PET or PEN). Next, a layer designed to selectively allow the passage of holes or electrons is applied to the transparent surface of the conductor. These layers, known as interlayers, blocking layers, or transport layers come from a wide variety of material classes, ranging from organic molecules and polymers, to metals and metal oxides. The most popular blocking layers are PEDOT:PSS, or molybdenum oxide (Cat. No. 203815) as electron blocking layers (EBL) that form the anode and zinc oxide, PFN, and PEIE as hole blocking layers (HBL) that form the cathode. These materials are designed to be soluble in polar solvents to facilitate their orthogonality with the subsequent BHJ, which is most soluble in non-polar aromatic solvents.

Figure 2.Schematic view of common standard and inverted BHJ solar cell architectures.
The bulk heterojunction is formed from two components. Both the donor and acceptor are mutually dissolved in a common solvent system. Upon drying of the ink, donor- and acceptorrich phases form in the resulting film, giving rise to the bulk heterojunction, an interdigitated donor and acceptor network. The donor component is designed to transport holes, and the acceptor component is designed to transport electrons. Excitons separate into free charges at the interface making a high surface area between these two components desirable. These materials can be either organic small molecules or polymers, but the most popular systems contain polymeric donor materials and soluble small molecule acceptors. The polymers employed in high performance BHJ solar cells are not limited in design and diversity, the best of which cover a range of band gaps which dictate the ability of the material to absorb light and give rise to a wide variety of colors. Finally, the complementary blocking layer is applied on top of the BHJ, followed by a top electrode which can either be opaque or transparent. In a majority of cases the top electrode is fabricated from silver, aluminium, or PEDOT:PSS, either alone or in combination.
OPV Materials Development
Materials Design
Tremendous progress has been made in the field of OPV materials over the last 20 years.8,9 These improvements are the result of both a better understanding of the working principles of OPV devices and the development of new, more suitable organic materials. Since BHJ is a mixture of donor (designed to transfer holes) and acceptor (designed to transfer electrons) materials (Figure 3), interdigitation allows an efficient separation of excitons into free charges. Commonly, BHJ consist of polymeric, oligomeric, or defined small molecules, pi-conjugated donors and fullerene acceptors.10

Figure 3.Working principle of OPV using the concept of the difference between the highest occupied molecular orbital (HOMO) and lowest unoccupied molecular orbital (LUMO) creating the band-gap for a donor polymer (same applies to oligomers and small molecules).
When blended with a fullerene derivative, the optimal donor polymers have (1) highest occupied molecular orbital (HOMO) energy levels below -5.1 eV to ensure air stability and effective charge separation at the polymer:fullerene/small molecule interface, which results in high open circuit voltage (Voc), (2) lowest unoccupied molecular orbital (LUMO) energy levels in the range of -3.6 to -4.0 eV to create enough driving force to promote an exciton dissociation, and (3) relatively low energy band gap (1.2 to 1.9 eV) with a broad absorption spectrum to absorb as much sun light as possible to generate high closed or short circuit current (Jsc). Additionally, materials should be readily soluble in common non-chlorinated organic solvents to allow easy processability.
There are two main approaches used to achieve low-band gap conjugated materials. The first involves incorporation of units that promote formation of quinoid structures in the excited state. The second approach is based on incorporating alternating electron donating and electron accepting moieties in the material backbone (Figure 4). Usually, the HOMO energy level of the polymer is derived from the electron rich moiety, whereas the LUMO energy level is derived from the electron poor unit. This approach allows very precise tuning of both energy levels as well as solubility profile of the resulting materials.

Figure 4.Design principles of low-band gap OPV materials
OPV materials can be synthesised by various transition metal catalyzed cross-coupling reactions. The three main approaches shown in Figure 5 are used for the synthesis of these semiconducting polymers.

Figure 5.Polymerization reactions used for OPV polymers
Stille polymerization is the most versatile method for the synthesis of conjugated polymers. It is a very robust technique that works for most of the known highly electron rich monomers, such as thiophene and related derivatives. However, a key drawback is the extra cost required for the safe handling of the precursors and waste stream.11 An alternative method involves Suzuki polymerization.12 However, the suitability of the monomers, or functional groups towards Suzuki conditions is limited, particularly for electron rich monomers like thiophene and related derivatives used in OPV. More recently, direct heteroarylation polymerization has been used.13 It does not require preparation and purification of organometalic species, thus making synthesis shorter and more cost effective. Yet only a handful of monomers were found suitable for direct heteroarylation polymerization and much more in depth research is needed to fully understand the potential and limitations of this synthetic method. Many modern small molecules and oligomers have been prepared using similar coupling methodologies.
Future Prospects
There has been significant focus by the research community on the design of new donor materials. Some of the most important donor polymers are shown in Figure 6. This figure perfectly illustrates the changes in material design.14–19 Alongside polymer development, small molecule donor materials have also been developed. Bazan et al. achieved efficiencies above 7% from their small molecule donor materials.20

Figure 6.Examples of donor materials for OPV
Until recently, acceptor materials have been almost exclusively based on fullerenes (Figure 7). Much research in this field has focused on fine-tuning the HOMO-LUMO energy levels in order to gain higher Voc in BHJ OPV and increase the solubility of the materials.21,22
However, since 2014, the performance of OPV cells using nonfullerene acceptors (NFA) has increased dramatically, with efficiencies increasing from 5% in 201423 to 12% in the end of 2016.24 Moreover, the solubility and energy levels of NFA materials have the potential to be tuned to give more flexibility than conventional fullerene acceptors. NFA are also strong light absorbers, meaning that they contribute to the overall EQE of the device. All of these points add to the versatility of these materials.25 The field of NFA is still very immature, but it is believed that use of NFA will enable researchers to reach power conversion efficiencies up to 20%.

Figure 7.Examples of OPV acceptor materials
OPV Applications
OPV technology can be tuned to create a unique choice of colors and shades (Figure 8A). It also inherently enables greater design freedom, because OPV systems are lightweight and manufactured from solution-deposition techniques in which printing or laser structuration can easily be incorporated (Figure 8B and 8C). These properties are key enablers for lowpower IoTs, since many applications require: (1) customized design and form factors, (2) higher performance and lifetime, (3) low-maintenance energy-harvesting systems and interoperability between devices and locations. Here, we will focus on three applications of OPV including urban architecture, indoor IoY, and wearables.

Figure 8.Inherent freedom of design of OPV. A) PV-F series (OPV active inks developed by EMD Performance Materials) offer a choice of colors and shades while maintaining compatibility with large schale roll-to-roll processing equipment for manufacturing OPV modules. B) Customized design elements on OPV printed system by OPVIUS. C) Elektree: OPVpowered lamp by OPVIUS GmbH, made by connecting a series of leafshaped OPV modules.
OPV Urban Facades
One aim of integrating OPV technology into facade elements is to reduce both the energy consumption and CO2 emission of a building. This global trend is demonstrated in the United States by schemes like the Leadership in Energy and Environmental Design (LEED) program. The European Union has set a target for new buildings to be nearly zero energy by 2021. This requires significant effort in energy managements systems and smart building envelopes. The recently updated EU legislative package, includes a proposal for a “Smartness Indicator” (SI) to characterize a building’s ability to interact with its occupants as well as to manage the overall energy consumption of connected energy assets by itself.26
Modern smart buildings are expected to contain a manifold of interacting systems, extending beyond the heating, ventilation, and air conditioning systems commonly found in current buildings. Systems for managing lighting, security and safety, energy demand, and personalization features will become much more common. The use of energy-harvesting surfaces (glass or membranes) in urban environments is expected to be a key enabler for the larger deployment of the various IoT applications that currently rely on power from the grid or from batteries with limited lifetime and require frequent maintenance. Examples of these wireless solutions are sensors and small motorized systems for ventilation27 and shading.6
Compared to classic PV technology, OPV can better serve both the functional and aesthetic demands of designers and architects while also enabling the use of building-integrated photovoltaics. OPV modules have been integrated into various glass facades and into structural membrane architectures. One example is the African Union Peace and Security Building in Addis Ababa where OPV is used to power lights throughout the building, significantly reducing its thermal load (Figure 9A). A more recent example of OPV integration into building elements was developed by a collaboration between OPVIUS GmbH and BGT Bischoff Glas Technik AG, supervised by Timo Carl Architecture, Kassel in 2016 (Figure 9D). Here, OPV modules were laminated into glass-facades of an exterior elevator shaft attached to an existing building in Marburg, Germany. The electricity produced is used to ventilate the shaft and prevent heat accumulation. A major breakthrough was achieved by demonstrating these glass-facades comply with German safety standards and building regulations. Another more recent example of OPV installation is the OPV facade created by SUNEW, Brazil.

Figure 9. A)OPV sail in shape of African continent using EMD Performance Materials PV-F series and OPVIUS technology at the African Union Peace and Security Building in Addis Ababa. B) Gray-colored OPV modules made with PV-F series from Lisicon, by OPVIUS GmbH, demonstrating efficiencies of 50 W/m2. Picture taken at the Adaptative Architectures and Smart Materials Conference in Chicago, USA. C) OPV elements installed by SUNEW in a building in Sao Paolo, Brazil. D) OPV glass-façade used to ventilate an exterior elevator in Marburg, Germany.
In the urban context new applications are expected to emerge with wider distribution of smart parking meters, centralized traffic-control systems, active displays, or even the management of autonomous vehicles. One interesting approach takes advantage of the lightweight property of OPV modules through integration into bus shelters or other infrastructure to support the development of “connected cities” (Figure 10A). Such applications not only increase consumer safety by providing power for lighting during the night, but also enabling other devices such as sensors for probing air quality or temperature, connected hardware for real-time traffic monitoring, or electronic charging stations.

Figure 10. A)Conceptual design for off-grid kiosks and display invented by JCDecaux in collaboration with Armor that combine mobile technology, e-paper display and ASCA© photovoltaic films. B) Artist view of the interior of a concept car equipped with multiple IoT applications that use OPV to harvest energy. C) Roof of a car equipped with OPV that could be used to block the sun, improve energy efficiency, and supply energy for IoT devices. Concept A is equipped with ARMOR ASCA OPV film and concepts B and C) with OPVIUS GmbH Technology.
OPV for Indoor IoT
While a reference standard light spectrum has been developed for outdoor applications (AM1.5), such a standard is missing for indoor light tests due to the large variations in light sources such as fluorescent light, LED, incandescent lamps, sun coming through windows (Figure 12A).28 The most commonly used light sources in home or office environments are fluorescent lamps or white LEDs, and as a result they are the most commonly used lighting for technical studies. Their illuminance is usually in the region of 200 lux (living room environment) to 1000 lux (office environment), corresponding to a light intensity of around 100 to 500 times lower than 1 Sun condition. Under indoor conditions, low power indoor devices such as wireless sensor network nodes consume power in the region of few mW.29 Well established photovoltaic technologies such as silicon solar cells have already been shown to provide adequate power under such low-light levels. The use of photovoltaic technologies in this type of environment is promising for the fabrication of low maintenance devices, in addition to being more environmentally friendly than commercial batteries. As a result, a number of indoor products have emerged within the last few years using photovoltaic technologies, including several that integrate OPV (Figure 11).29,30

Figure 11. A) Philips remote control B) Solar computer mouse by Wholesale C) Indoor lighting made with a curved OPV module by .STOOL. D) ‘Citigami’ , the latest creation from LITOGAMI in collaboration with Armor, is a collection of poetic, entertaining, educational, and decorative cards neatly incorporating an ultra-light and ultra-flexible ASCA© photovoltaic film as its sole source of energy.
In the case of indoor IoT applications, OPV addresses several inherent weaknesses in PV systems by enhancing design flexibility and aesthetic appeal, reducing weight, and most importantly, increasing efficiency under low-light conditions, leading to a smaller system footprint. In a recent study, Cutting et al. reported that the efficiency of OPV devices can be increased up to 350% under LED light intensity relative to outdoor conditions (Figure 12B). This performance is significantly higher than that of competing Si-technologies or Perovskite-type cells under the same irradiance. OPV devices used in this study can reach efficiencies of more than 20% PCE, higher than their inorganic counterparts.31

Figure 12A) Normalized power spectra of different light sources: 1 Sun AM1.5G (line), incandescent light bulb 2800 K (red squares), solar simulator with xenon lamp (brown diamond), CFL 6500 K (purple triangles), LED (green diamond), and the normalized absorption spectrum of an organic solar cell using a BHJ made of PBTZ-stat-BDTT-8 donor material and PV-A600 acceptor material (blue circle). B) The percent increase in power conversion of various photovoltaic systems under white LED relative to outdoor conditions. Data for graph B compiled from reference 31 with permission.
Another study by Lee et al., shows some specific OPV systems using a combination of the donor polymer PCDTBT (Cat. 753998) and the PCBM[70] acceptor materials (Cat. No. 684465) can reach more than 16% PCE under 300 lux fluorescent lamp.32 Interestingly, this BHJ system is not the highest performing under outdoor conditions. The researchers explain that the best performing system benefits here from an optimal energy gap that matches the irradiance spectrum of the light source.32 This system delivers a power output of 13.9 μW/cm2 under 300 lux, which is higher than gallium arsenide and polycrystalline silicon cells reported by Teran et al. at 12.5 μW/cm2 and 2.5 μW/cm2, respectively, under the same conditions.33 In another study, De Rossi et al. extracted powers of 12.5 μW/ cm2 and 9.1 μW/cm2 under 300 lux fluorescent lamp irradiance from DSSC and a-Si, respectively.34 Finally, Lee et al. showed the power output obtained with OPV modules of 100 cm2 can reach almost 1 mW, opening the door to multiple use in photorechargeable systems under low light conditions, also recently demonstrated by Lechene et al.28 with super capacitors.
Overall, these studies highlight that OPV systems already achieve high efficiency in low-light environments. Contrary to other PV technologies, the optical absorption profile of OPV systems can be finely tuned by various means, such as by varying the molecular design of the donor and/or acceptor components, changing their ratio in the BHJ, or by defining a process window that favors certain defined morphologies. These intrinsic properties increase the freedom of design and ease of integration, making OPV technology ideal for future indoor IoT applications.
The integration of flexible and highly-sensitive energy harvesting systems such as OPV is expected to benefit a number of aspects in future smart homes, including connected thermostats or wireless sensors. The potential applications become even broader when considering the retail industry where IoT applications have the potential to revolutionize inventory management processes and sales analytics. In this sector, IoT is seen as a game changer throughout the value chain, including improved store layouts and live-tracking of inventory, to name just a few applications.
OPV for Wearables IoT
Ever since the semiconducting properties of organic materials were first demonstrated in devices, significant attention has been devoted to integrating these technologies into wearable systems. In the case of OPV, Krebs et al. first described a series of fundamental strategies for the integration of OPVs into garments and textiles.35 This work was followed by a variety of approaches by other researchers that tried to solve the challenges of integrating OPV with wearable surfaces. To do so, researchers have focused on developing new materials, new deposition techniques, and innovative stacks for OPV devices.
To this end, O’Connor et al. developed a system on a polyimide substrate that can be worn on the skin. The authors sacrificed the charge transport properties of the OPV materials by integrating non-optimized donor polymer material into the BHJ and additives to the other layers in order to increase plasticization behavior.36 By doing this, they demonstrated a vast improvement in mechanical robustness (stretchability) of the OPV devices when submitted to cycles of deformation bending compared to standard devices that use P3HT as the donor material (Figure 13A). Another approach reported by Lee et al., used organic solar cells stitched onto a textile functionalized by conductive fibers.37 A PCE of about 2% was obtained for the system. Digging deeper into stack prototyping, Gaudiana et al. published a breakthrough approach with the design of OPV wires that could be used as textile fibers.38 The optoelectronic viability of the stack is ensured by a customized co-axial design of the wire, which enables the device to exceed the performance of standard planar geometries (Figure 13B). For the most part, these studies demonstrated the potential of OPV integration with fabrics, but did not advance beyond single lab prototypes. In an effort to accelerate the application and scalability of the technology, the Advanced Structures and Composite Center at the University of Maine has produced 40,000 feet of OPV wires with an efficiency of 7%, and created 40 ft2 of woven fabric from OPV wires.39

Figure 13. A) Schematic view describing a working OPV cell. B) Photograph showing woven cloth comprised of OPV wires. Image and photo courtesy of the Advanced Structures and Composite Center at the University of Maine
In parallel to these efforts, several electronic wearables and portable products have been developed for commercial use over the past few years, paving the way for IoT technologies. Markets where these technologies are expected to have an impact include healthcare (diagnostics, wellness monitoring), clothing, augmented reality, fitness, and security. Figures 14B, C, and D, show commercial examples in which OPV has been used in outdoor gear such as tents, backpacks and waterproof jackets. Figure 14A shows a smart bag, which connects via Bluetooth to a smartphone, powered by OPV. The bag highlights incoming messages and calls and sounds an alarm if the phone is left behind.

Figure 14. A) Tailor-made smart bag by Kolon Industries, integrating organic solar module energy-harvester (wrapped by red rectangle) and NFC technology. B) Star Tent by Kolon Industries, integrating LED lighting with OPV as the energy-source. C) Smart jacket integrating an OPV module, LED, and Bluetooth by Kolon Industries. D) Backpack by Kolon Industries, integrating OPV as power source for cooling fans. E) Solar bag designed and manufactured by Armor using ASCA© photovoltaic films as source of energy.
Conclusion
OPV technology demonstrates a number of enabling properties for products that require energy harvesting systems. Compared to existing power source alternatives, OPV offers added value in terms of performance, environmental friendliness, design customization, and form factor.
To date, the first applications of OPV technology have started to emerge with installation in smart buildings, urban facades and membranes, indoor/low-light products, as well as wearables and portables. We anticipate the continuous improvement of OPV systems will further enable its implementation in a wider scope of markets including retail, worksites, homes, and transportation.
References
To continue reading please sign in or create an account.
Don't Have An Account?