Lo sviluppo di film più durevoli e, in definitiva, di sacche monouso più resilienti ha richiesto un anno di scrupoloso lavoro trascorso ad armeggiare per mettere a punto la soluzione migliore, a effettuare i test necessari e a mettere a punto i test più efficaci.
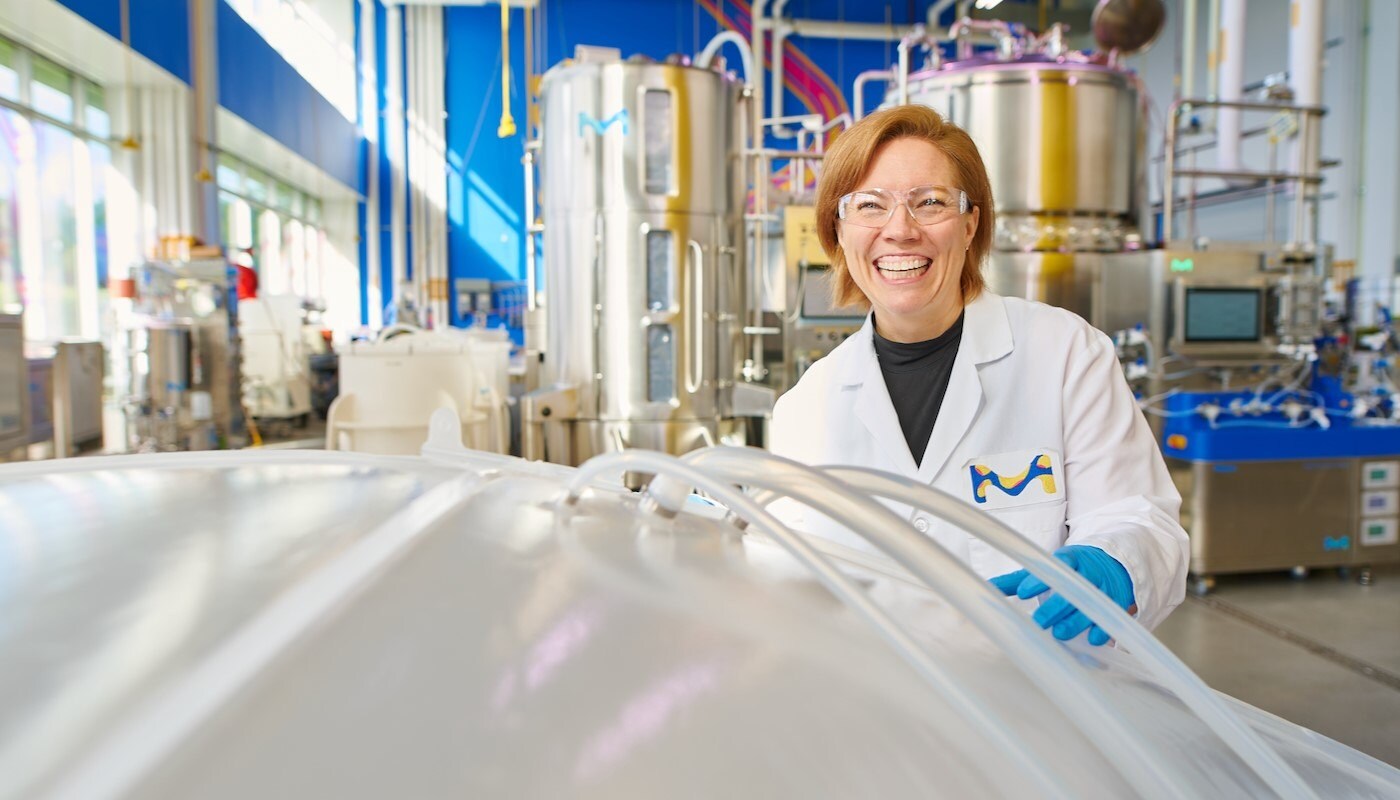
Shannon Cleveland è fotografata in un laboratorio M Lab vicino a una sacca monouso fabbricata con il film Ultimus.
18 settembre 2023 | 6 min
C’è molto di più di quanto si possa vedere.
Nei materiali multistrato, i diversi strati svolgono funzioni differenti. Alcuni forniscono integrità strutturale. Altri aiutano i materiali a sopportare le sollecitazioni termiche oppure conferiscono loro flessibilità. Tutto ciò è valido per gli pneumatici delle nostre auto, per le tute spaziali indossate dagli astronauti, ma anche per una nuova sacca monouso destinata ai produttori biofarmaceutici.
Negli ultimi anni, gli ingegneri Merck, tra cui Shannon Cleveland e David DeCoste, si sono occupati della progettazione di nuove sacche monouso con cui rivestire gli impianti per la produzione di farmaci. Lo sviluppo delle sacche monouso non è stato un’impresa da poco, perché è stato necessario capire quali materiali utilizzare e poi, cosa fondamentale, assicurare che i diversi strati si unissero tra loro perfettamente.
“Il film è costituito da tredici strati diversi ognuno dei quali svolge una funzione ben precisa,” dice DeCoste, il direttore della Ricerca e Sviluppo (R&D) di questo gruppo di lavoro. “Alcuni strati forniscono l’ambiente giusto per la crescita delle cellule, mentre altri assicurano robustezza e flessibilità. Raggiungere la commercializzazione del prodotto ha richiesto il lavoro di un grande team di sviluppo trasversale a numerosi dipartimenti.”
Si parte pensando già alla fine
In numerosi impianti di bioprocesso, le sacche monouso rivestono i bioreattori, componenti dell’attrezzatura che spesso assomigliano ai grandi fermentatori utilizzati nei birrifici. I bioreattori contengono le cellule e altri materiali utilizzati per produrre farmaci salvavita. Le sacche monouso accelerano la produzione farmaceutica perché, oltre ad apportare numerosi altri benefici, riducono i tempi di lavaggio tra due batch di produzione. Il che significa che gli impianti sono in grado di produrre un maggior quantitativo di farmaci in meno tempo.
Se si verifica una perdita in una sacca monouso contenente una miscela farmaceutica, l’errore è estremamente frustrante e costoso. Dovendo contenere grandi quantitativi di liquido, raggiungere temperature comprese in un ampio intervallo ed essere trasportate all’interno degli stabilimenti, le sacche sono costantemente esposte al rischio di abrasioni o forature.
Per Cleveland e i suoi colleghi, pensare al fatto che il loro lavoro alla fine abbia un impatto sui pazienti fa sì che ogni tanto valga la pena affrontare una lunga giornata di lavoro. “È profondamente gratificante sapere che con il mio lavoro contribuisco allo sviluppo di prodotti che fanno la differenza,” afferma.
I migliori contendenti
Nel corso di alcuni anni, il team di R&D team della sede Merck di Bedford, Massachusetts, USA, che comprende Cleveland e i suoi colleghi, ha sviluppato e confrontato attentamente diverse combinazioni di materiali per creare un nuovo film per le sacche monouso. È risultato chiaro abbastanza rapidamente che l’aggiunta di tessuto di nylon avrebbe aumentato robustezza e resilienza.
I film contenenti nylon erano eccellenti, ma i diversi strati non volevano stare insieme; così è cominciata la caccia ad altri polimeri. Avendo bisogno di sviluppare uno strato legante, ovvero che tenesse insieme la struttura, il team ha iniziato a testare attentamente le diverse combinazioni.
Gli ingegneri in laboratorio sottopongono il film a uno stress tremendo, torcendolo e comprimendolo ripetutamente, 2.700 volte per la precisione.
Dopo aver testato un pezzo di film con quello che descrive giustamente come lo “strizzatoio,” Cleveland ha quantificato il grado di stress esercitato sul materiale dalle torsioni. In un altro test, Cleveland e i suoi colleghi hanno calcolato il tempo necessario perché una punta metallica perfori il film.
Questi test e una serie di altre prove hanno portato i ricercatori a una conclusione insoddisfacente: i candidati che avevano raggiunto la fase finale si comportavano tutti allo stesso modo. I test non erano in grado di rilevare alcuna differenza tra una gran varietà di polimeri utilizzati nello strato legante. Tuttavia Cleveland era in grado di individuare visivamente una differenza tra i diversi materiali sottoposti a stress. Sapeva che la storia era più complessa.
“Avevo bisogno di nuovi dati per rilevare le differenze tra i vari film. Dovevo mettere a punto un nuovo test,” dice Cleveland.
Giorni di offuscamento
Dopo aver esaminato attentamente la letteratura, Cleveland decise di provare qualcosa di diverso. Trovare la combinazione di polimeri giusta e perfezionare il processo di unificazione dei diversi strati del film è stato sicuramente essenziale, ma trovare il modo per valutare le diverse composizioni è stato un momento di svolta fondamentale.
Invece di perforare i film con un oggetto appuntito, Cleveland decise di distenderli con l’ausilio di una punta smussata. I materiali così trattati apparivano un po’ torbidi e Cleveland volle provare a quantificare questo fenomeno. Più la pellicola si distendeva, più appariva sottile e torbida.
Nessuno nel suo laboratorio ci aveva mai provato prima, quindi non avevano accesso alle attrezzature giuste. Fortunatamente, in una posizione precedente, lei aveva lavorato in fondo allo stesso corridoio del suo attuale laboratorio, nel laboratorio di R&D Filtrazione, dove, invece, si occupano, e testano, la torbidità. Benché loro testino i liquidi e non i film, Cleveland decise di fare un tentativo.
Aveva quantificato la torbidità dell’acqua, perché non provare con quella della plastica?
Cleveland si recò al lavoro armata di una gran quantità di letteratura che le frullava in testa, forbici ed etichette. Tagliò minuscoli pezzi di plastica, li mise in alcune cuvette e accese il torbidimetro. Dopo un paio di giri, capì di essere sulla buona strada. Aveva trovato un modo per quantificare quali film erano meno torbidi, e quindi più resistenti, degli altri. Questo nuovo test ha portato il team a perfezionare e migliorare ulteriormente l’aspetto e la prestazioni del film.
Cleveland è attratta da problemi come questi, quelli che richiedono un pensiero iterativo e fuori dagli schemi. "Mi rende felice," dice, ripensando all’elaborazione concettuale creativa, sebbene per certi versi non ortodossa, che ha condotto alla produzione del film. "È gratificante essere in grado di pensare come faccio io e poter fare la differenza.”
A scuola, a tutti gli scienziati in erba si insegna a fare ipotesi, prove, prove e ancora prove. A volte è necessario mettere alla prova i test. Però questo è il tipo di rompicapo che rivitalizza Cleveland e i suoi colleghi. Dai primi giorni di lavoro in laboratorio, allo scale-up con il team della produzione fino al lancio finale, molto più di cento persone hanno lavorato in modo collaborativo per dar vita al film Ultimus e alle nuove sacche monouso.
Ma non si sono fermati con Ultimus. Il team è già alla ricerca di nuove soluzioni tra cui sacche più semplici da spedire e imballare. Tutto ciò che fanno ha un obiettivo comune: aiutare i produttori biofarmaceutici a produrre più rapidamente farmaci salvavita. All’orizzonte si prospettano film e sacche ancora migliori. E probabilmente anche altri test.
Per saperne di più su Ultimus
Il film Ultimus® è disponibile nelle sacche monouso per bioprocesso Mobius® 3D che costituiscono una soluzione più resistente e duratura per tutte le difficoltà della produzione monouso. Scopri di più sul film Ultimus®, su come può fornire maggior resistenza e sicurezza per le applicazioni del bioprocesso, esamina le sue specifiche e altro ancora.
Ringraziamenti speciali
Shannon Cleveland e David DeCoste ringraziano tutti i colleghi che hanno avuto un ruolo fondamentale nello sviluppo del film, specialmente i colleghi della R&D Joe Cianciolo, Joe Muldoon, Brian Pereira, Diana Perez, Marissa Maher e Kate O'Brien.
Altre storie

Mike D'Acquisto II, un soffiatore di vetro scientifico, dirige il fuoco sul collo di un pallone con fondo tondo.
A differenza delle provette e dei becher di vetro che vengono stampati in massa, la vetreria scientifica su misura viene realizzata a mano e riparata da soffiatori altamente specializzati in un processo in cui scintille, botti e momenti di tensione non mancano.
Per continuare a leggere, autenticati o crea un account.
Non hai un Account?