From Form to Function: Molding Porous Materials in Three Dimensions by Colloidal Crystal Templating
Melissa A. Fierke, Fan Li, Andreas Stein, Prof.
Department of Chemistry, University of Minnesota
Material Matters 2008, 3.1, 10.
Overview
Methods of structuring materials with submicrometer features in two dimensions have become highly sophisticated. For example, lithographic methods are now capable of carving out several hundred million electronic components on an integrated circuit the width of a fingernail. Extending similar architectures into the third dimension by using these topdown engineering methods is possible only to a limited degree and at great expense. Bottom-up chemical methods involving self-assembly and templating provide promising alternatives to 3D structures with critical dimensions on the length scale of nanometers to micrometers. One such approach, colloidal crystal templating, is particularly versatile, and has been demonstrated for materials that target applications such as photonic crystals, sensors, power storage devices, artificial bone materials and multifunctional catalysts.1
A colloidal crystal is an ordered array of particles with diameters ranging from tens of nanometers to micrometers. In typical templating syntheses, these are arrangements of close-packed, uniformly sized polymer or silica spheres. Such colloidal crystals resemble natural opals, both in their geometries (face-centered cubic sets of spheres) and in their beautiful opalescent appearances caused by diffraction of light. In both cases, the interstitial volume between the spheres can be filled with a second phase. When colloidal crystals are used as a template, the original spheres are then removed, leaving an inverse replica of the opal structure, known as an inverse opal or three-dimensionally ordered macroporous (3DOM) structure (Figure 1). These structures consist of solid walls surrounding an ordered array of spherical voids with windows connecting the pores where template spheres were in contact (Figure 2). The walls are typically tens of nanometers thick, while the void sizes depend on the diameter of the template spheres.
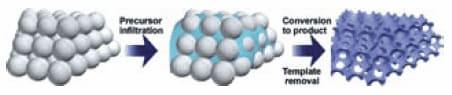
Figure 1.Scheme of the general colloidal crystal templating process. A colloidal crystal is infiltrated by a precursor material, followed by conversion of the precursor to the final product and sphere removal.

Figure 2.(a) Scanning electron micrograph of a 3DOM carbon monolith showing the periodic porosity of the structure. Dark circles are windows between the pores. (b, c) Transmission electron micrographs of 3DOM silica. The light areas correspond to the macropores space. In the higher resolution image (c) additional mesopore channels are visible within the wall structure.
Porous nanostructures synthesized by colloidal crystal templating can offer several advantages over porous materials made by other methods. Unlike materials produced using less regular templates, inverse opals are highly periodic in three dimensions. Changing the size of the spheres in the colloidal crystal template easily controls pore sizes. Inverse opals typically have relatively large surface areas, and the open structure offers easy access to the entire surface. These materials have continuous wall skeletons with thicknesses on the order of nanometers, so they can exhibit some properties of nanoparticles, including confinement effects and high surface-to-volume ratios.2 Also, the synthesis methods for inverse opal materials are quite versatile, producing materials of various compositions and morphologies with a wide range of pore sizes, which are being investigated for many distinct applications (see Table 1).
Preparing the Colloidal Crystal Template
The colloidal crystal templates are formed by packing monodisperse spheres into close-packed arrays. Typically, silica spheres are synthesized by variations of the Stöber-Fink- Bohn method,3 while polymer, poly(methyl methacrylate) (PMMA) or poly(styrene) (PS) spheres are made by emulsion polymerization,4,5 with or without added emulsifier (see Sphere Preparation Note on p. 13). Spheres ranging in size from tens of nm to hundreds of μm can be employed. A partial list of the possible methods to order spheres into colloidal crystal templates includes gravity sedimentation, centrifugation, filtration, two-dimensional deposition, slit fitting, and pressing.6 The most common packing arrangement is based on hexagonally close-packed (hcp) layers and face-centered cubic (fcc) packing which provides nearly one-quarter of the template volume as interstitial space available for subsequent infiltration.
The Templating Process
Most colloidal crystal templating processes involve three general steps. First, a precursor material is infiltrated into the void spaces of the colloidal crystal template. Next, the precursor is converted into the desired solid product. Finally, to create the porosity within the sample, the spheres are removed during or after precursor conversion (Figure 1). The technique is quite versatile and is used with many types of precursor materials. Some of the reported synthesis techniques include sol-gel, infiltration with a metal salt, solvothermal synthesis, electrochemical deposition, electroless deposition, chemical vapor deposition, melt imbibing, and organic polymerization.1 Porous silicates can be made using the sol-gel method with tetraethoxysilane (333859) or tetramethoxysilane (679259). Other oxides prepared by sol-gel methods include those of Ti, Zr, Al, W, Fe, and Sb. Additional elements can be incorporated by subsequent doping or by employing mixed metal precursors or alkoxide/acetate mixtures. For example, yttria-stabilized zircionia can be made from a mixture of zirconium n-propoxide (333972) and yttrium tri-isopropoxide (665916).7 Templated precipitation of metal salts (acetates, oxalates, etc.) provides a route to macroporous oxides, metals, and metal carbonates. For example, periodic macroporous hematite (Fe2O3) was made by 3DOM templating using an aqueous solution of iron (III) oxalate (381446).8 The 3DOM NixCo1–x alloy was templated from a PMMA array using methanol solutions of nickel(II) acetate (379883) and cobalt (II) acetate (437875).9 In this case, metal oxalates were formed by soaking PMMA-salt composites in oxalic acid (658537) solution, followed by processing at 400 °C in a reducing atmosphere.
Another option is co-deposition of nanoparticles with the colloidal crystal spheres. After the nanoparticles settle within the array of spheres, they can be sintered to form a continuous skeleton. Co-deposition is typically used when nanoparticles of the desired product phase are easier to synthesize ex-situ than within the confinement of the template. The third technique currently used to produce inverse opal materials involves coreshell materials that are assembled into ordered arrays. After the spheres are removed, the remaining material consists of hollow close-packed shells. Macroporous titania was produced by this method by coating PS spheres with polyelectrolyte multilayers infiltrated with titanium (IV) isopropoxide (377996).1
Following infiltration of the colloidal crystals, the precursor materials must be converted to the desired products. This can be accomplished by drying, pyrolysis or calcination, chemical conversion, crosslinking, cooling, etc., depending on the precursor materials used. In order to create the characteristic porosity in the inverse opal structure, the template spheres need to be eliminated. If polymer spheres are utilized as the template, they are typically removed by combustion, which may coincide with thermal conversion of the precursor. Polymer spheres can also be removed by solvent extraction. Silica spheres are typically removed by etching with a strong base or hydrofluoric acid.
The Compositional Spectrum
Because of the versatility of this templating method, possible product compositions are bounded largely by our imagination. One of the few restrictions is that the product must be able to withstand template removal without being damaged or deformed. The first inverse opals synthesized were simple oxides, including titania, zirconia, alumina, and silica.11-13Since then, many oxides have been prepared, including more simple oxides, as well as ternary and mixed oxides with much more complicated compositions. Non-oxides, such as carbon have also been synthesized. Various allotropes of carbon have been created with inverse opal structures, including graphitic, diamond, and glassy carbons.14,15 Other non-oxides include various carbides, nitrides, and chalcogenides. For example, the 3DOM chalcogenide CdS was prepared galvanostatically in silica opals from DMF or DMSO solutions of sulfur (213292) and CdCl2 (202908).1 Metallic and semiconducting macroporous materials are other classes of inverse opals that have been created. Macroporous gold was prepared from solutions of 15–21 nm colloidal gold (e.g. G1652), and the 3DOM semiconductor CdSe was made from solutions of CdSe nanocrystals (e.g. 662550).
Polymeric 3DOM materials can also be synthesized, including hydrocarbon polymers, as well as conducting and semiconducting polymers. Polymeric 3DOMs can be made either by templating monomer solution, or by filling colloidal crystals with solutions of preformed polymers. Electrodeposition or oxidative polymerization was used to prepare 3DOM conducting polymers, such as poly(pyrrole), poly(aniline), and poly(bithiophene) from pyrrole (131709), aniline, and bithiophene (241636), respectively.1 Inverse opal hydrogels that respond to external stimuli, including pH, temperature, humidity, and the surrounding chemical environment have been developed. By combining multiple synthesis techniques or through functionalization of the finished structures, inverse opal materials with hybrid organic-inorganic compositions are possible.
Tuning Morphologies
Product structures can be controlled at both nanometer and bulk length scales by choosing appropriate forms of the template and the precursors. Changes in the colloidal crystal packing method and synthesis techniques have been used to create products of varying morphologies, including monolithic materials, powders, thin films, and wires, all with long-range, ordered porosity. By adding secondary templates, such as block copolymers or surfactants, it is possible to introduce smaller mesopores into the walls that surround the macropores formed by the colloidal particles.16 Such hierarchical porosity introduces extremely large surface areas while keeping diffusion paths short and surfaces readily accessible. Recently, dual templating processes have even been used to create porous nanoparticles with specific shapes (cubes, tetrapods, spheres).17 A few examples of these materials are shown in Figure 3.
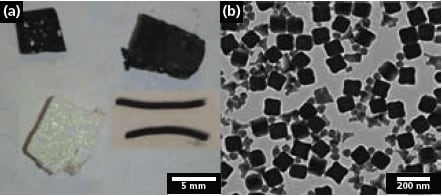
Figure 3.Examples of possible morphologies of materials prepared by colloidal crystal templating: (a) inverse opal monoliths composed of carbon (top left), tungsten (top right), and silica (bottom left). 3DOM carbon filaments are also shown (bottom right). (b) Mesoporous silica nanocubes, spheres and tetrapods prepared by dual templating with both colloidal crystals and surfactants.
From Form to Function
Inverse opals are being investigated for a wide range of applications because of their unique properties. The highly periodic structure with repeat distances coinciding with the wavelength of visible or infrared light makes them desirable as photonic crystals that can guide and manipulate light.18,193DOM materials are also being examined for use as sensors because they can give a measurable response to different stimuli, including a change in refractive index, a change in pore spacing or geometry, or a change in surface electronic states.20,21 They are being considered for electrochemical power systems, including early development of a nanostructured Li-ion battery with an interpenetrating anode, electrolyte, and cathode components—a paradigm shift in battery architectures intended for small devices with little available footprint area for a power source.22 Another possible application of these materials is their use as non-toxic, colorfast pigments that can be prepared with any color of the spectrum, depending on the composition of the material, the pore size within the structure, and the refractive index of the material filling the pores (Figure 4). Such pigments can even change their colors reversibly if pores are filled with a liquid.23Reactive applications that take advantage of the large surface area of 3DOM materials and ready access to the pores include complex catalyst supports and bioglasses for bone repair.24

Figure 4.Photographs of 3DOM zirconia, silica (top middle) and titania powders (bottom left). The different colors of the 3DOM zirconia samples arise from the different pore sizes.
The Bottom Line
Colloidal crystal templating is a simple, highly versatile synthetic technique for creating periodic structures with nanometer-to-submicrometer features in three dimensions. It is used to synthesize highly ordered porous materials with a wide range of pore sizes, morphologies, and compositions. The inverse opal products are being investigated by scientists around the world for a variety of applications, where they can provide features and functionalities that are either difficult to obtain by other methods or (in the case of 3D photonic crystals) much less expensive than alternative techniques. As the field of colloidal crystal templating continues to grow, more unique materials and applications are sure to be developed.
References
Pour continuer à lire, veuillez vous connecter à votre compte ou en créer un.
Vous n'avez pas de compte ?