Developing more durable films and, ultimately, more resilient single-use bags took years of careful tinkering, testing and tinkering with testing.
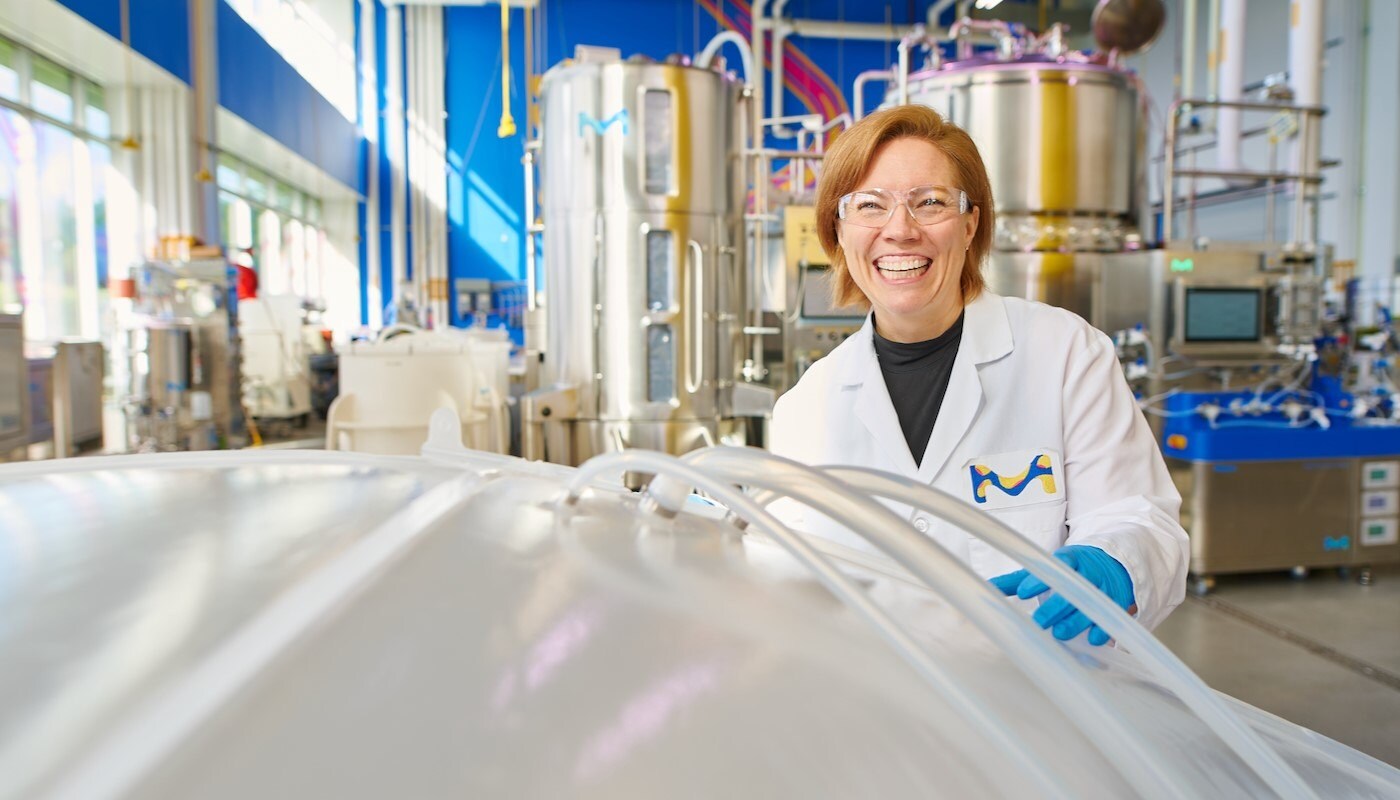
Shannon Cleveland stands in the M Lab holding a single-use bag made with Ultimus film.
September 18, 2023 | 6 min
There’s more than meets the eye.
In multi-layered materials, different layers serve different purposes. Some provide structural integrity. Others help materials withstand temperature stressors or allow them to flex. You could say this about tires on the cars we drive, spacesuits astronauts wear — or a new single-use bag for biopharmaceutical manufacturers.
Over the last several years, MilliporeSigma engineers — including Shannon Cleveland and David DeCoste — worked on designing new single-use bags that line equipment used in drug manufacturing. Developing the single-use bags was no small feat, as the team needed to figure out what materials to use and then, critically, ensure those layers came together seamlessly.
“The film has thirteen distinctive layers, and every layer serves a specific purpose,” says DeCoste, who is the Research and Development (R&D) Director of the team. “Some layers provide the right environment to grow cells, while others provide strength and flexibility. Bringing the product to market took a large development team represented by many departments.”
Start with the End in Mind
In many bioprocessing facilities, single-use bags line bioreactors — pieces of equipment that often resemble large fermenting tanks in breweries. Bioreactors hold cells and other materials used to manufacture life-saving drugs. Single-use bags speed up drug manufacturing because, alongside several other benefits, they reduce the clean time between batches. This means facilities can produce more drugs in less time.
If a single-use bag holding pharmaceutical mixture leaks, it’s an extremely frustrating and costly mistake. Because the bags hold large amounts of liquids, experience a wide range of temperatures and get hauled around facilities, they are at constant risk for abrasions and punctures.
For Cleveland and others, thinking about the fact that their work ultimately impacts patientsmakes the occasional long day worthwhile. “It’s deeply rewarding to know I help develop products that make a difference,” she says.
Top Contenders
Over the course of a few years, the R&D team at MilliporeSigma Bedford, Massachusetts, USA site — including Cleveland and her colleagues— carefully developed and compared different combinations of materials to create a new film for single-use bags. They figured out pretty quickly that adding woven nylon would increase strength and resilience.
Films containing nylon excelled, but the separate layers didn’t want to stay together — so the hunt for additional polymers began. The team needed to develop a tie layer — or a layer that would keep the structure together. They started testing combinations carefully.
Engineers put film under tremendous stress in the lab, twisting and compressing the film repeatedly — 2,700 times to be exact.
After a piece of film was put through what Cleveland aptly describes as the “wringer,” she quantified how the twists stressed the material. In a different test, Cleveland and colleagues calculated how long it took a metal point to puncture the film.
These tests — and a suite of others — led researchers to an unsatisfying conclusion: the final set of candidates all performed equally. The tests couldn’t discern a difference between a variety of polymers in the tie layer. Yet, Cleveland could spot a difference visually between the stressed materials. She knew there was more to the story.
“I needed new data to see differences between films. I needed to come up with a new test,” Cleveland says.
Hazy Days
After carefully reviewing the literature, Cleveland decided to try something else. Coming up with the right combination of polymers and refining the process of bringing film layers together was critical, yes — but finding a way to evaluate different compositions was a key breakthrough moment.
Instead of puncturing the films with a pointed object, Cleveland decided to stretch the different films using a dulled point. The displaced materials looked a little hazy, so Cleveland decided she should try to quantify that. The more the film stretched, the more it looked hazy and thin.
Nobody in her lab had tried that before, so they didn’t readily have access to the right equipment. Fortunately, in a previous position, she worked in the filtration R&D lab down the hall from her current lab, where they do think about — and test — haziness. While they test liquids, not films, Cleveland decided to give it a try.
She quantified haziness in water, so why not try plastic?
Equipped with a vast amount of literature swirling in her mind, scissors and labels, Cleveland went to work. She cut tiny pieces of plastic, dropped them into cuvettes and powered up the haze meter. After a couple of rounds, she knew she was onto something. She found a way to quantify which films were less hazy — and, ultimately, more resilient — than other films. This new test led the team to further refine and improve the appearance and performance of the film.
She's drawn to problems like these. Ones that require iterative out-of-the-box bag thinking. "It makes me happy," she says, reflecting on the creative, albeit somewhat unorthodox, thought process that produced the film. "It's gratifying that I can think the way I do and make a difference.”
In school, budding scientists are all taught to hypothesize, test, test and test again. Sometimes, they need tests for tests. It's the kind of puzzle that invigorates Cleveland and her colleagues, though. From early days in the lab, to upscaling with the manufacturing team, the ultimate launch, well over one hundred people worked collaboratively to bring Ultimus film — and the new single-use bags — to life.
They haven’t stopped with Ultimus, though. The team is already looking for new solutions, including bags that ship and pack more easily. Everything they do has a common goal in mind: helping biopharmaceutical manufacturers produce life-saving drugs faster. Even better films and bags are on the horizon. And likely more tests, too.
More About Ultimus
Ultimus® Film is available in Mobius® 3D single-use bioprocess bags providing a stronger, more durable solution for all single-use manufacturing challenges. Learn more about Ultimus® film, how it can provide additional strength and safety for bioprocessing applications, review the specifications and more.
Special Thanks
Shannon Cleveland and David DeCoste thank all their colleagues who played a pivotal role in the development of the film, especially R&D colleagues Joe Cianciolo, Joe Muldoon, Brian Pereira, Diana Perez, Marissa Maher and Kate O'Brien.
Read More Stories

Mike D'Acquisto II, a scientific glassblower, directs fire to the neck of a round-bottom flask.
Glass vials and beakers are molded by mass production, but customized scientific glassware is handcrafted and repaired by highly-trained scientific glassblowers in a process filled with sparks, pops and tense moments.
To continue reading please sign in or create an account.
Don't Have An Account?