Five Ways Packages are Getting Greener
A lot more goes into packaging than you might think. We unpack some ways that your deliveries are getting greener and why changes can take time.
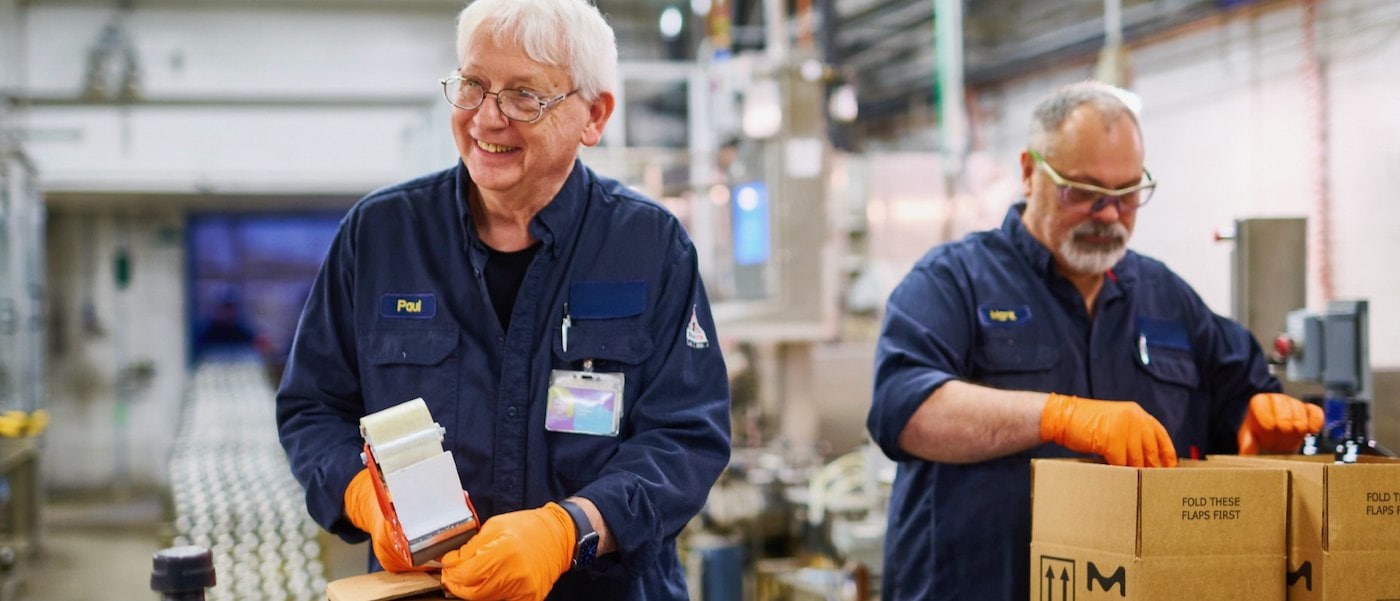
May 22, 2024 | 4 min
“Why is this bottle inside a plastic bag that’s inside a box?”
"Why do orders come in different boxes?”
“Why do some of my packages come with crumpled paper and others come with air pillows?”
Customers have a lot of questions about why products arrive the way they do. They come in boxes, cans and envelopes of all different sizes. They sometimes come together, yet other times they arrive separately.
With more than 300,000 products — and about 50,000 packages shipped worldwide daily — it shouldn’t be a surprise that we think a lot about packaging. We have team members who source packaging materials, stay up to speed on regulations and design new packages. These designers — or packaging engineers — devise new ways to ship products, test their ideas and, then, test some more. They oversee all elements of packaging, from selecting the smallest bottle and cap to organizing how products are arranged on cargo ships, and, of course, designing boxes in between.
It takes time to redesign packages — from the box size to the tape, the padding materials to the labels. Here are some reasons why these changes take time:
Packaging changes should not impact the product in any way. It needs to arrive at its destination in the same state that it departed the warehouse.
Shipping breakable, sensitive and hazardous goods, is tightly regulated. In some cases, rules differ based on geography — both where the package is coming from and where it is headed. In fact, the same product might need to be shipped differently depending on these regulations.
Packaging engineers must run any packaging change through tests to ensure the change is safe. In the United States, for example, packages that transport hazardous goods must be re-tested every two years.
Given these challenges, we test any change on a small scale first. Packaging engineers often start with a single product line from a single distribution center. Over time, they work to rollout the changes at other sites.
Safety is our top priority when we redesign packaging, and sustainability — guided by SMASH Packaging principles — is a central driver, too. We focus on how changes can reduce emissions, wood products and plastic, to name just a few.
Here are five ways we’re making packages greener:
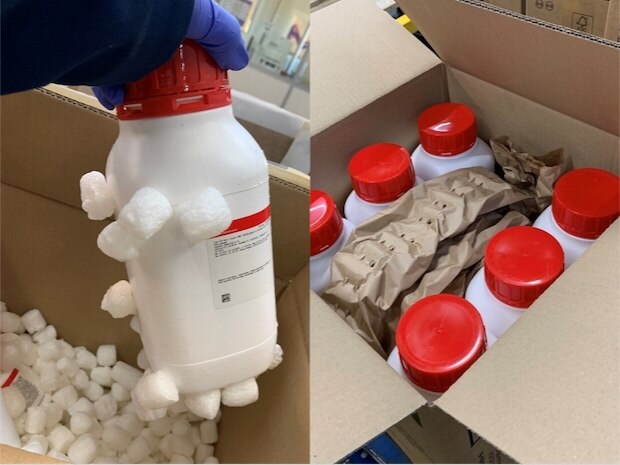
1. Goodbye packing peanuts
They stick to everything. They end up everywhere. And they’re hard to recycle. You hated them and so did we. Years ago, we started looking for alternatives to packing peanuts and after countless hours of testing, we phased them out at many sites. Instead of peanuts, you’ll often find 100% recycled plastic air pillows or crumpled paper.
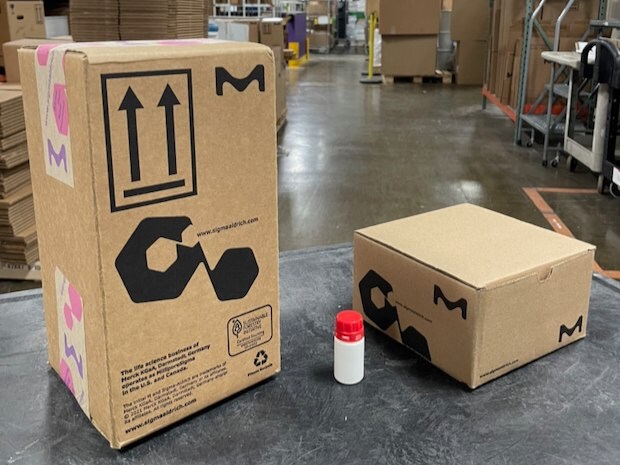
2. Looking to downsize
Sometimes, all you need are a couple of *specific* droplets to continue your work. When that tiny vial comes in a massive box, it can be downright confusing. Our teams are working hard to get those small orders into smaller boxes and envelopes. Smaller packages mean more can fit on delivery vehicles and less cardboard is needed for the box itself and filler materials. Ultimately, this has dramatic impacts on paper usage, reducing it by over half for each shipment. For customers receiving orders from our Milwaukee, WI, USA site, you might have already noticed this downsizing.
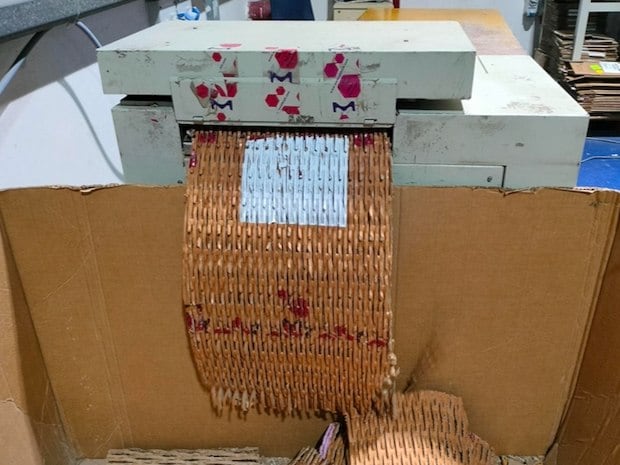
3. New life for old boxes
Nobody wants products flying around an empty box, which is why boxes are stuffed with filler material. Filler material — like air pillows or bubble wrap — is often purchased, but some sites are getting creative about how to fill their boxes. In the Jigani, India, distribution center, instead of purchasing paper to fill up boxes, they are taking advantage of boxes shipped to the site. Rather than breaking down and recycling those boxes, now they shred them and reuse them as filler for boxes shipping off. This saves 14 tons of paper annually.
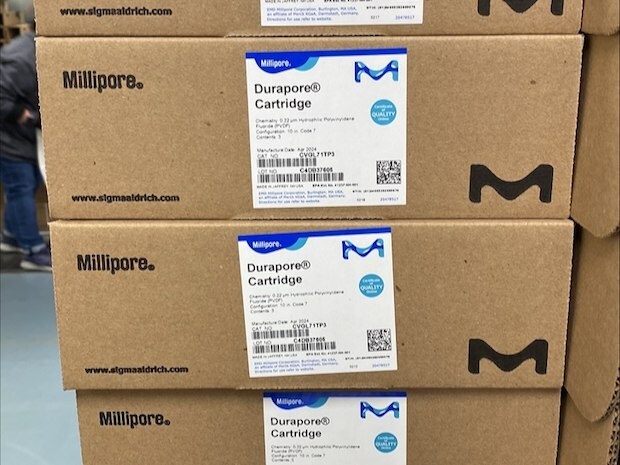
4. So long paper slips
Ensuring our products are of the highest quality is a top priority. As part of this commitment, nearly every product we ship is accompanied by a Certificate of Quality. For decades, we’ve included a paper slip inside the box alongside products. At our Jaffrey, NH USA site, the team ditched paper in lieu of QR codes, saving 3 million sheets of printer paper annually. Down the road in Danvers, MA, a similar change was implemented.
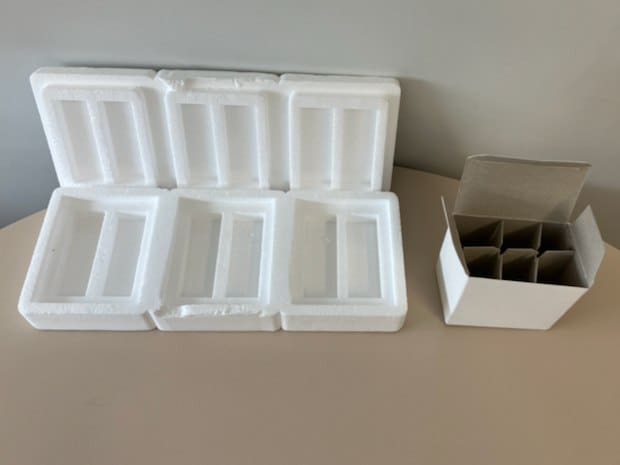
5. Protecting glass without expanded polystyrene
To keep glass bottles safe during shipment, packaging teams separate them using dividers. Expanded polystyrene — known as EPS — makes a great cushion, but is difficult to recycle. Given this, the team at Buchs, Switzerland worked to replace the EPS inserts with corrugated cardboard inserts. Annually, this means about 1,500 kg of EPS — or about the weight of two compact cars — is swapped for greener options. Sites around the world are cutting down EPS usage in lieu of greener alternatives.
Our Greener Packaging Commitment
In 2019, we established a program known as SMASH Packaging to increase the sustainability of our packaging while meeting safety, quality and performance requirements. It’s a challenge given our portfolio of 300,000-plus diverse products with distinct needs, but SMASH helps identify opportunities to make packaging greener. Not only are we revisiting past products, but we also carefully consider greener packaging solutions for all new products thanks to the Design for Sustainability framework. With more than 100 packaging improvement projects driven by colleagues across the company, SMASH has already reduced over 400 metric tons of packaging annually.
To continue reading please sign in or create an account.
Don't Have An Account?