Virus-Based Vaccine Manufacturing

Process Train for both Inactivated & Live Attenuated Virus
Virus-based vaccines consist of either attenuated or inactivated virus. These vaccines can activate all phases of the immune system and offer rapid and durable long-term immunity by eliciting neutralizing antibodies against the target pathogen.
The process to manufacture attenuated virus-based vaccines is complex, consists of multiple steps and must maintain the infective potential of the attenuated virus. While there is a general workflow for production, a templated approach for manufacturing does not exist. Instead, each process must be tailored based on the shape, size, nature, physico-chemical behavior, stability, and host specificity of the virus.
Related Technical Articles
- Learn more one the attenuated viral vaccines manufacturing process: cell culture, clarification, nuclease treatment, chromatography, and sterile filtration.
- Influenza vaccines are commonly made using egg-based and cell-based manufacturing strategies. Find step-by-step information on the manufacturing process for each method.
- Cost Modeling Vaccine Manufacturing: Estimate Production Costs for mRNA and other Vaccine ModalitiesA custom-designed cost model is used to explore the economics of vaccine manufacturing across several different modalities including mRNA. The model enables greater process understanding, simulates bottlenecks, and helps to optimize production efficiency.
- Adjuvant selection is dependent on vaccine formulation and individual application. Effectiveness and safety are of primary importance in adjuvant selection, yet a number of other characteristics must be considered.
- See All (2)
Find More Articles and Protocols
Optimize Upstream Productivity and Clarification with Reliable Scale-up
Upstream culture processes developed for manufacturing of virus-based vaccines must be optimized to meet productivity requirements. This optimization includes the clarification step which is essential for removal of cells and cell debris and to ensure a robust virus harvest. The upstream process is only successful, however, if it can be reliably scaled in order to meet anticipated market demand.
Achieve Yield and Efficiency Goals with Robust Impurity Removal
Nucleic acids from lysed cells are a common contaminant in virus-based vaccine processes. Regulations require that the level of carry-over host cell nucleic acid must be below 10 ng/dose of attenuated virus-based vaccine. Benzonase® endonuclease treatment followed by tangential flow filtration is a robust and powerful combination to degrade and then remove residual nucleic acid components.
Maximize Downstream Recovery
Benzonase® endonuclease treatment is sufficient to achieve the desired level of purity for most virus-based vaccines during concentration and diafiltration. Chromatography is required, however, to achieve purity goals for next generation virus-based vaccines such as Japanese encephalitis virus (JEV) and dengue virus (DENV). Because each manufacturing process must be tailored to the characteristics of the virus, a toolbox of options for downstream purification is essential to deliver the desired purity while ensuring an optimal recovery.
Ensure Patient Safety
Even though virus-based vaccines are manufactured using attenuated viruses, ensuring the safety of patients remains an important concern. The final virus vaccine bulk is comparable to that of water. As such, the vaccine can be sterilized using 0.22 µm sterilizing filtration prior to the final formulation and fill finish steps.


Nuclease Treatment & Clarification
Ensure robust scalability:
- Nuclease Treatment with Benzonase® Suitable for Biopharmaceutical Production EMPROVE® Bio
- Benzonase® Detection with Benzonase® Elisa Kit II to Detect Left Over Benzonase® Endonuclease in the Process
- Primary/Secondary Clarification with Millistak+® HC POD Depth Filters
- Primary Clarification with Clarisolve® Depth Filters
- Secondary Clarification with Polysep II cartridges
- Secondary Clarification with Milligard® PES filters

Bioprocessing Liquid Cell Culture Media & Buffers
We offer the industry’s highest quality sterile filtered liquid capabilities, supplying ready-to-use cell culture media, buffers, CIP and SIP products from GMP facilities worldwide to optimize your biopharma production.

Downstream - Tangential Flow Filtration
Achieve yield, efficiency and virus recovery goals while ensuring robust impurity removal.
- Ultrafiltration / Diafiltration with Pellicon® 2 Cassettes
- Ultrafiltration / Diafiltration with Pellicon® 3 Cassettes
- Ultrafiltration / Diafiltration with Pellicon® Capsule with Ultracel® Membrane
- Mobius® TFF 80 System, Mobius® FlexReady Solution for TFF, Cogent® Lab Systems and Cogent® Process-scale Tangential Flow Filtration System

Downstream - Chromatography
- Membrane Chromatography with Eshmuno® Q Resin
- Membrane Chromatography with Natrix® Q Recon Mini Chromatography Membranes
- Membrane Chromatography with Natrix® Q Pilot Chromatography Membrane
- Capture and/or Polishing Chromatography with Fractogel® EMD DEAE Chromatography Resins
- Capture and/or Polishing Chromatography with Fractogel® EMD DMAE Chromatography Resins
- Mobius® FlexReady Solution for Chromatography
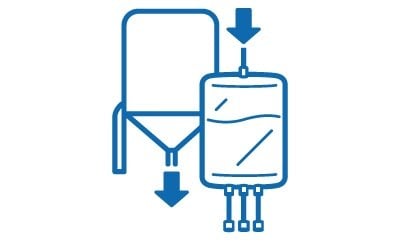
Virus Inactivation

Process Chemicals and Formulation

Final Sterile Filtration & Filling
Remove cross product contamination concerns while streamlining fill-finishing requirements and complying with current regulatory requirements.

Analytics Software & PAT Technology
Related Resources
- Application Guide: Biopharmaceutical
A search tool to help you overcome your manufacturing challenges.
- Brochure: Vaccine Bioprocessing Handbook
In this handbook, we explain the vaccine production processes and process improvements for all types of vaccine development platforms.
- Mini-Handbook: Cell-Based Vaccine Bioprocessing
Live attenuated viral vaccines can be created using a complex, multi-step cell-based manufacturing process. It is not a templated process. The manufacturing process for each viral vaccine is different.
- e-Book: Enabling Capabilities & Solutions for all Vaccine Platforms
From process development to full-scale GMP-manufacturing, our global vaccine capabilities can help you achieve these goals for all your modalities/platforms including virus-based, subunit, VLP, viral vector, pDNA and mRNA vaccines.
- White Paper: Filtration Strategies for Optimal Development and Purification of a Foot and Mouth Disease Virus
We collaborated with MEVAC to optimize upstream and downstream processes for FMD vaccine manufacturing to establish a scalable, cost-efficient and GMP compliant process. This white paper focuses on the integration of new filtration strategies in both upstream and downstream processes.
- White Paper: Downstream Process Intensification for Virus Purification Using Membrane Chromatography
This white paper provides an overview of the challenges presented by current approaches to virus production and the opportunities to develop a platform approach that can work across different viral modalities and accelerate process development.
- Application Note: Effect of Benzonase® Endonuclease Addition to Purification of Sabin Polio Virus Type 3
This application note summarizes the benefits of incorporating Benzonase® endonuclease in a polio virus type 3 production process.
- Article: Filter-Based Clarification of Viral Vaccines and Vectors
In this article, a comprehensive overview is provided on different filtration technologies and their application in viral vaccine clarification, outlining challenges and present current best practices.
To continue reading please sign in or create an account.
Don't Have An Account?