Solar Cells: Towards Printable, Ultra-Lightweight, and Flexible Solar Technologies
Conventional energy sources used globally include coal, oil, natural gas, and hydropower. The EIA estimates that the world’s consumption of energy will grow by 50% between 2018 and 2050.1 Renewable power contributions must triple to achieve average projected net zero rates by 2050. Consequently, governments and businesses alike are investing in sustainable energy solutions. Solar energy will play a critical role in the increasing demand for electricity and the escalating necessity for cleaner and more eco-friendly energy sources. Sufficient sunlight reaches the earth’s landmass every 40 minutes to power the planet for a year, with the sun generating 2-6 kWh m2 per day.
Photovoltaic Power: The Optimization of Solar Cell Efficiency
A photovoltaic power station, also known as a solar park, solar farm, or solar power plant, is a large-scale grid-connected photovoltaic power system (PV system) designed for the supply of merchant power. They are differentiated from most building-mounted and other decentralized solar power systems because they supply power at the utility level rather than to a local user or users. Projects of this type are typically referred to as utility-scale solar. Unlike concentrated solar power, which employs heat to power conventional generator systems, photovoltaic technology directly converts sunlight into electrical current. Both technologies have their respective advantages and disadvantages, but photovoltaic technology, for several reasons, has been more commonly used to date. As of 2019, about 97% of utility-scale solar power capacity was PV.2 In some countries, the nameplate capacity of photovoltaic power stations is rated in megawatt peak (MWp), which refers to the solar array's theoretical maximum DC power output. The largest sites under construction have capacities of hundreds of MWp and some have more than 1 GWp.3
It has taken over 40 years for solar photovoltaic panels to reach their current efficiency, cost-effectiveness, and large-scale manufacturability. The Shockley-Queisser limit is the theoretical maximum efficiency of a solar cell. Thus, semiconductors with a band gap between 1 and 1.5 eV (827 nm to 1240 nm; near-infrared) have the greatest potential to form an efficient single-junction cell. The three criteria for a material to be used in solar cells are: a band gap from 1 eV to 1.8 ev, high optical absorption and high electrical conductivity.
Maximum solar cell efficiencies reported in the literature can vary depending on manufacturing technologies and architecture. For instance, first-generation technology, which is based on thick crystalline-type films (single, polycrystal) and monojunction architecture using wafer-based manufacturing processes, was reported to have 27.6% maximum efficiency when a single/monocrystal concentrator architecture was used [4]. Thin-film solar cells, categorized as second-generation technology, are distinguished by their use of amorphous silicon, CIGS, or Cd/Te/CdS as active materials, along with a monojunction design and roll-to-roll production process. The highest solar cell efficiency reported for the second-generation technology was 23.4% by using Cu-In-Ga-Se2 (CIGS) as active materials in the manufacturing process.5 The third generation of manufacturing technology encompasses dye-sensitized (DSSC), perovskite (PSC), organic (OSC), and quantum dot (QDSC) solar cells. Often called “emerging technologies,” the third generation distinguishes itself by utilizing either mono- or polyjunction (also called multi-junction) architecture in the manufacturing process. Among the emerging technologies, the maximum solar efficiency reported in the literature for a solar cell was 47.6% if a polyjunction with concentrator architecture was used.6 The fourth generation of manufacturing technology is also known as hybrid technology. It incorporates as active materials various nanomaterials, such as metal and oxide nanoparticles, carbon nanotubes, graphene, and its derivatives. Hybrid technology in the latest generation can adopt either mono or polyjunction architecture, and the manufacturing approach can vary depending on the materials and architectural design.
Material Solutions: Solar Panel Recyling and Greener Solar Cells
In relation to active materials, solar cells are classified as shown in figures 1-37:

Figure 1:Solar cell types by active materials, non-organic photovoltaic.
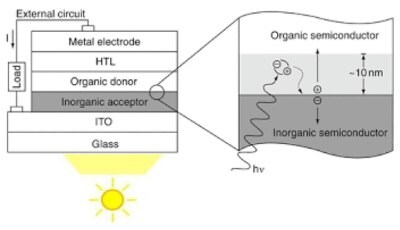
Figure 2:Solar cell types by active materials, hybrid photovoltaic.

Figure 3:Solar cell types by active materials, organic photovoltaic.
(A) Specific solar cell layers of organic photovoltaic devices.
(B) Molecular Donor-Acceptor* Interfaces.
Despite the various progressions in manufacturing technologies, it is worth highlighting two trends that are applicable to all types of manufacturing methods: recycling of solar panels and the development of solution-processable, eco-friendly technology that facilitates the construction of ultra-lightweight and flexible solar cells in large volumes via cost-effective printing techniques.
The solar panel recycling trend is driven primarily by rising environmental concerns as well as government policies for the safe disposal of solar panels. Around the globe, millions upon millions of solar panels are destined for the local dump. Each panel is a toxic cocktail of gallium arsenide, tellurium, silver, crystalline silicon, lead, cadmium, and other heavy metals.
Among the solution-processable greener technology trends for solar cells include the use of greener solvents during the manufacturing process to decrease the quantity and toxicity of solvents.8 Printable solar cells, also known as printed solar cells, are a type of solar technology that can be produced using printing techniques. These solar cells are made from materials such as organic polymers or inorganic compounds, which can be deposited in thin layers onto flexible substrates such as plastic, metal, or paper. The printing process can be carried out using various techniques, such as screen printing, inkjet printing, or roll-to-roll printing. This market is significantly expanding, given the rapid advancement of printing technology. Printable solar cells provide a scalable and cost-effective solution to address the growing demand for renewable energy. In addition, their adaptable nature allows them to harness energy from a range of sources, such as walls, rolling blinds, umbrellas, curtains, and tents, which sets them apart from other technologies.
Regardless of whether a solar cell is non-organic, organic, or hybrid, it is composed of the following fundamental elements: cathode, anode, donor layer, acceptor layer, and buffer layer. We provide a comprehensive range of materials for every component, comprising optically transparent and electrically conductive substances, specific substrates equipped with electrically conductive compounds, organic electron transport materials and n-type inorganic semiconductors (associated with inks and precursors), organic hole transport materials, p-type inorganic semiconductors, and semiconductor inks and precursors. Further, we offer a specialized selection of greener solvents for energy/electronic applications (ElectroGreen™ solvents), silane coupling agents, and nanostructured materials (from carbon nanomaterials to MXenes).
We offer unmatched, unique, and comprehensive solutions for your solar cell development workflow technology, including in-house customization/development capabilities for focus product groups.
References
Pour continuer à lire, veuillez vous connecter à votre compte ou en créer un.
Vous n'avez pas de compte ?