Proactive Solutions for Risk Mitigation
What is Risk Mitigation?
Risk mitigation is the process of assessing risks and taking one of the following actions: removing the risk, reducing the risk, or accommodating the risk. Global events such as the pandemic and military conflicts have led to supply chain shortages acutely demonstrating that managing risk is imperative to maintaining a sustainable business. Collaborative proactive risk mitigation with suppliers can better protect a company’s ability to reliably deliver their products and services to their customers with the high
quality expected.
Manufacturing and testing organizations actively work to avoid disruption to their operations as the impact could be significant. Such disruptions could include:
- Delays in manufacturing
- Customers backorders
- Batch failures
- Product recalls
- Patient misdiagnosis or harm
Underlying Causes of Risk Where Customers Can Partner With Suppliers

Typical Categories of Risk that Companies Address with their Suppliers
Supply Chain
- Delivery delays or disruption
- Supplier unable or unwilling to support current or furure demands for products and/or services
- Raw material discontinuation/consoldation/product number changes
- Significant/unexpected price changes
Quality
- Raw material quality failure
- Raw material specificiation change
- Unexpected change in final product
- Missing QA/QC documentation
Regulatory
- Regulatory Compliance

Measurement of Risk
Manufacturing and testing organizations would benefit by doing a risk assessment of their sourced raw materials, considering factors such as
- Availability
- Quality
- Scalability
- Alignment of suppliers’ understanding of the customer expectations
- Compliance
The development and manufacture of critical products is a complex process involving multiple suppliers and raw materials. Minimizing disruptions of any kind is vital to supply chain management.

Level of Risk Tolerance
Different organizations have different levels of risk tolerance. The level of risk tolerance impacts how they approach the topic of risk mitigation and how they work with their supplier to proactively address this topic. Our recommended approach for the partners we supply would be to consider becoming more risk-averse as a way of making their business more robust, and we would welcome the opportunity to collaborate with them.

Spectrum of Risk Tolerance
Suppliers need to understand their customer's approaches and needs.
PROACTIVE SOLUTIONS
How Can Suppliers and Customers Work Together to Reduce Risk?
The ideal combination of Strategic Partnership and Supply Assurance can best be achieved through ongoing communication and collaboration between the supplier and the customer. The more critical the application and the raw material, the more controls need to be embedded into the processes, supply chain, and quality management.
Supply Chain
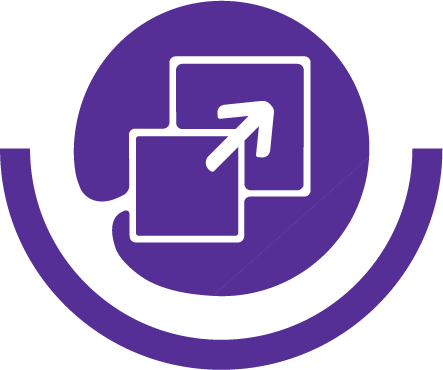
2. Consideration of alternative material with greater alignment to risk mitigation needs
Quality
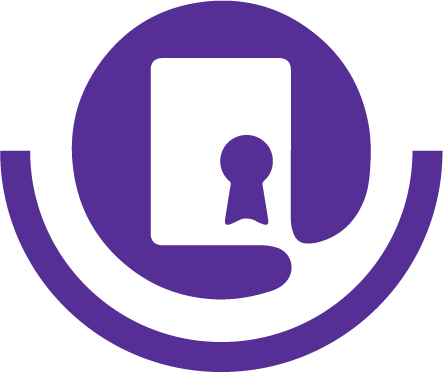
2. Quality Service Support
3. Regulatory Support
4. Documentation such as certificate of origin and specification comparison
Programs and Services
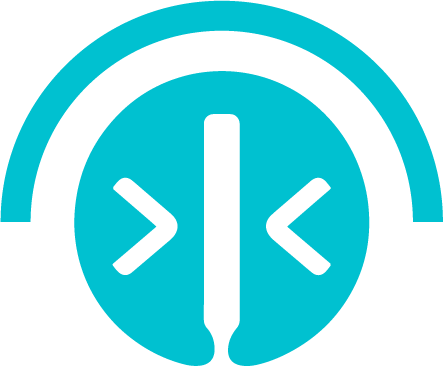
Custom and Contract Manufacturing

These capabilities help reduce your risk and accelerate your commercialization by providing a viable alternative to costly capital expenditure and facility expansion. Let us partner with you from the development of the initial concept, through scale-up and final manufacturing; ensuring that you have quality products, at the optimal scale and format, at the right time, to aid your rapid commercialization.
Streamline your production by leveraging our global manufacturing expertise. We offer unrivaled flexibility with customized filling and packaging. Visit our
Contract Manufacturing Resource Page to see example case studies and further explore how we can support your needs.
Specific Solutions for IVD & Diagnostic Assay Manufacturing:
Risk mitigation is a core focus for IVD manufacturers, driven by commercial best practices and regulatory requirements, such as the In Vitro Diagnostic Regulation (IVDR). The assessment of critical raw material performance, supply, and quality is important to minimize risk. Risk must be assessed and mitigated throughout the entire IVD commercialization process.
We can provide a range of ordering options, depending on where you are in your application process.
- R&D – often, a simple spot order is sufficient to fulfill your raw material needs.
- Pilot Scale - at this stage in your development, having a collaborative forecasting discussion with us, will support your smaller-scale manufacturing process.
- Manufacturing – There are different options available to you, to support your requirements for different raw materials. These include:
- Scheduling Agreement/Standing Order
- Supply Agreement
For more information on these various options, please contact your local account manager.
Risk assessment and risk mitigation begin with knowledge of the raw materials and incorporates performance, supply, and quality. We offer additional services for these critical applications, which require a formal risk assessment.
These discussions aim to create a common understanding between suppliers and our customers on topics such as:
- What is a critical raw material for your application(s)?
- Who defines a material as critical for your organization and what criteria do they use?
- How do you partner with your suppliers to manage change control and change control notifications?
- What are your expectations from your suppliers and how do you handle these requirements?
- How do you manage supply chain risk?
- What are the most important factors: consistency (quality, logistics, etc.), transparency, support, flexibility, and others?
Our Solutions
To continue reading please sign in or create an account.
Don't Have An Account?